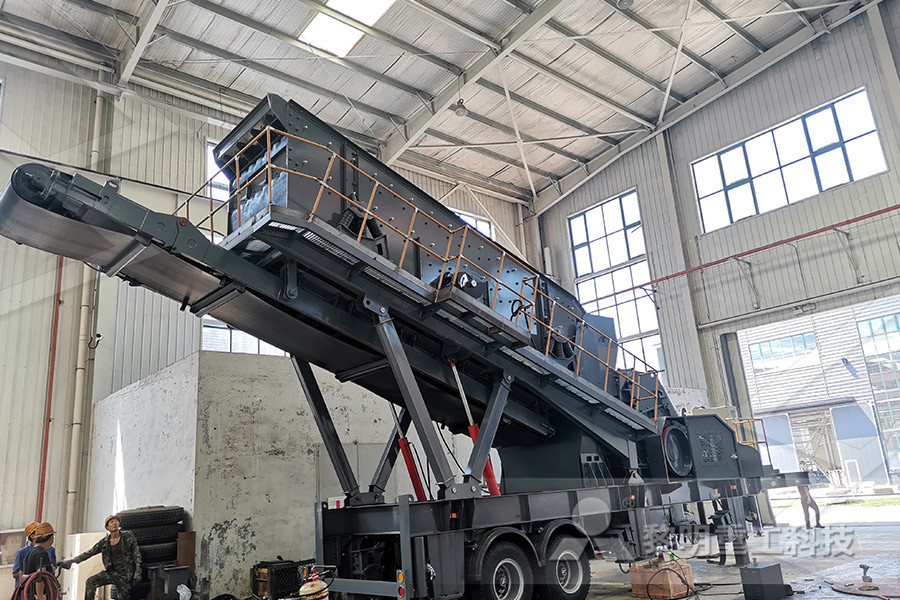
Efficiency Of Wet Milling Vs Dry Milling
efficiency of wet milling vs dry milling Wet milling Wet milling with IKA s inline machines is a safe and efficient alternative todry grinding Dry grinding creates a lot of dust which causes the need for properfiltering systems This can be of particular importance during grinding of substances The numerical values inserted in the table are about 25 percent higher for wet grinding than for dry grinding The values for capacity are more significant than those for efficiency In considering efficiency values, it must be recognized that at a given speed and ore charge either the wet or dry grinding Wet Grinding VS Dry Ball Mill GrindingWet Ball Milling Vs Dry Ball Milling Orbis Machinery, LLC Jun 27, 2019 The advantages Wet ball milling has over dry milling are higher energy efficiency, lower magnitude of excess enthalpy, better heat dissipation and absence of dust formation because of the aqueous environment it is being performed Particle Size Reduction Milling the powder in the wet or dry state produces different resultsball milling wet vs dry archidimensionsde
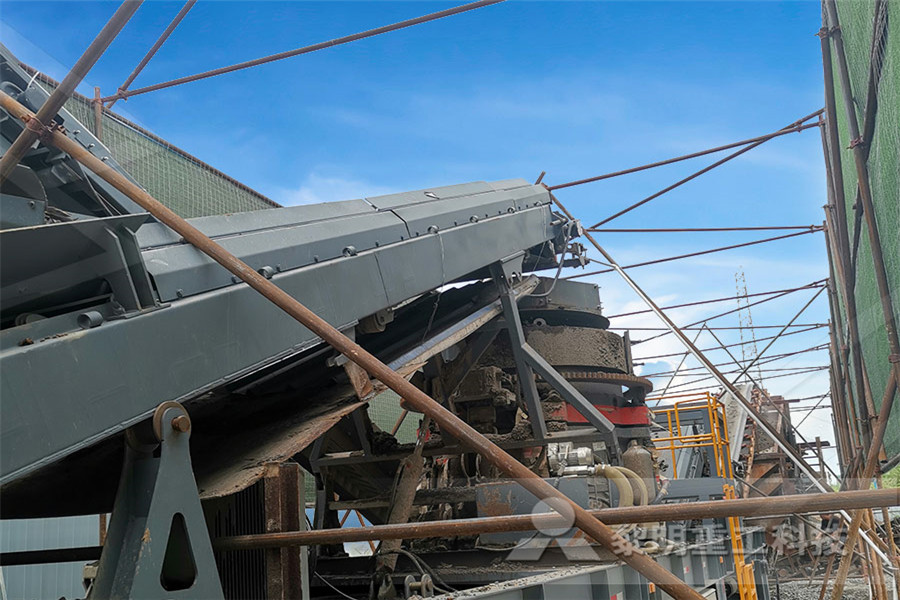
A comparative study on the effects of dry and wet
Chapman et al (2013) compared the effects of using different circuits HPGR (dry) rod mill (wet) and cone crusher (dry) rod mill (wet) on the flotation of base metal sulfides They indicated that apart from the grinding environment, HPGR could produce finer particles than a cone crusher This difference was higher in the fully dry system Fig 3 shows that wetmilled rice flour expressed three major peaks when analyzed for its particle size distribution The first peak at smaller size range (05 to 20 μm) could possibly be the remnant of damaged starch granule or some water insoluble protein particles that remained from the wet milling processThe second peak, which covered the 3–20 μm size range and with a peak around 8 Effects of DryMilling and WetMilling on Chemical Difference between dry and wet maize milling process Products As a leading global manufacturer of crushing, grinding and mining equipments, we offer advanced, reasonable solutions for any sizereduction requirements including, Difference between dry and wet maize milling process, quarry, aggregate, and different kinds of mineralsDifference between dry and wet maize milling process
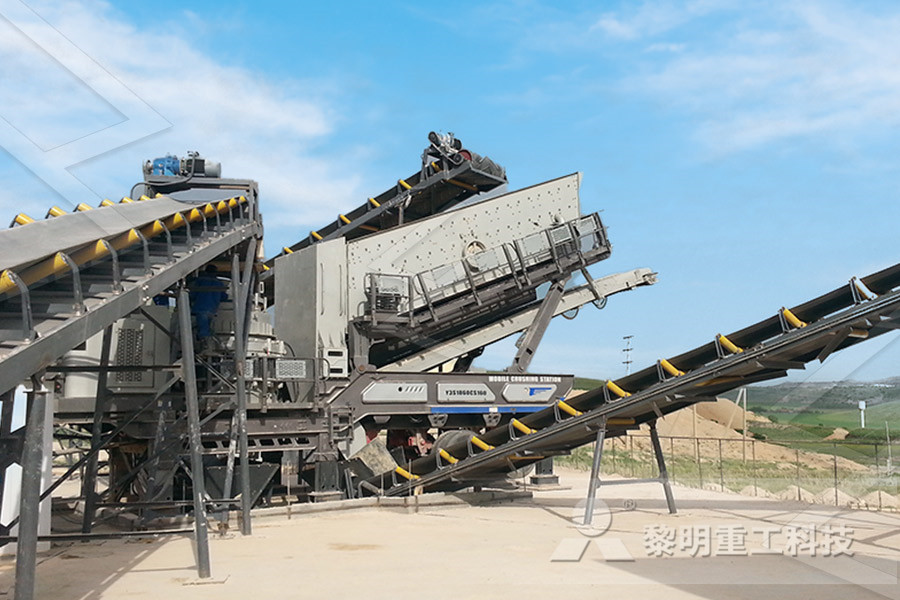
Wet and Dry Milling Equipment Size Reduction
Our conical mills are perfectly suited to both wet and dry applications The versatility of the UniMill means that the same machine can be used to mill wet and dry powders – providing a cost effective solution for many manufacturers Dry Milling Conical mills are most commonly used for the particle size reduction and deagglomeration of dry materials such as powders, granules and small Wet milling of cereal grains differs fundamentally from dry milling in being a maceration process in which physical and chemical changes occur in the nature of the basic constituents – starch, protein and cellwall material – to bring about a complete dissociation of the endosperm cell contents with the release of the starch granules from the protein network in which they are enclosedWet Milling an overview ScienceDirect Topics The efficiency of a particular stabilizer depends on its potential for interaction with the drug compound Generally, milling may be conducted with the drug in its dry state (dry milling) or suspended in a liquid medium (wet milling)Overview of milling techniques for improving the
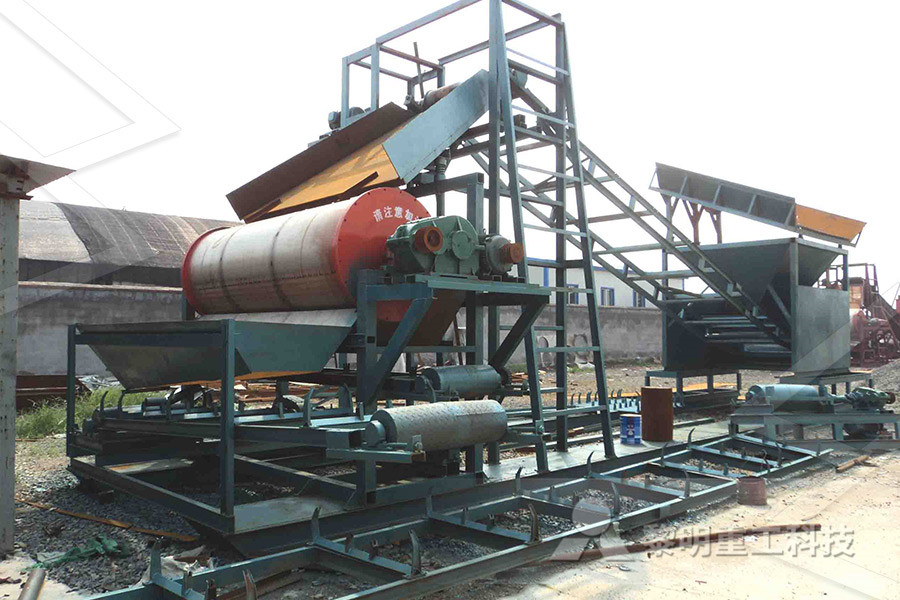
Factors Affecting Ball Mill Grinding Efficiency
The following are factors that have been investigated and applied in conventional ball milling in order to maximize grinding efficiency: a) Mill Geometry and Speed – Bond (1954) observed grinding efficiency to be a function of ball mill diameter, and established empirical relationships for recommended media size and mill speed that take this factor into accountwet mill vs dry mill in mining efficiency Copper extractionWikipedia Copper extraction refers to the methods used to obtain copper from its oresThe conversion of copper consists of a series of physical and electrochemical processes Methods have evolved and vary with country depending on the ore source local environmental regulations and wet mill vs dry mill in mining efficiencyWet Ball Milling Vs Dry Ball Milling Orbis Machinery, The advantages Wet ball milling has over dry milling are higher energy efficiency, lower magnitude of excess enthalpy, better heat dissipation and absence of Morewet ball mill advantages design ebusinessedupl
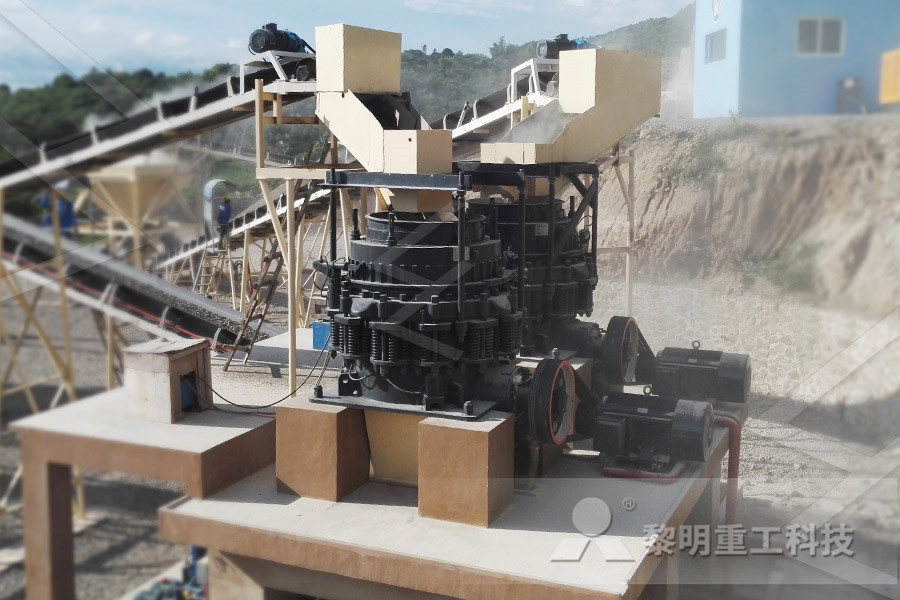
Milling process technology Global Milling Industry
Dry milling vs wet milling Dry grinding creates a lot of dust that results in the need for proper filtering systems This can be of specific importance during grinding of substances whose dust, when mixed with aerial oxygen, can result in explosive mixturesThe anaerobic fermentation test showed that, among the dry and wet milling pretreatments, the highest specific methane yield was obtained at 3 h dry milling pretreated (35807 mL g⁻¹ VS) and (PDF) Comparison of dry and wet milling pretreatment Corn flour is another milling byproduct feed Wet milling of corn is a more extensive process than dry milling Figure 54 illustrates an overview of the wet corn milling process In brief, wet milling involves cleaning, steeping, grinding, extraction, other separation Milling ByProducts of Cereal Grains Oregon State
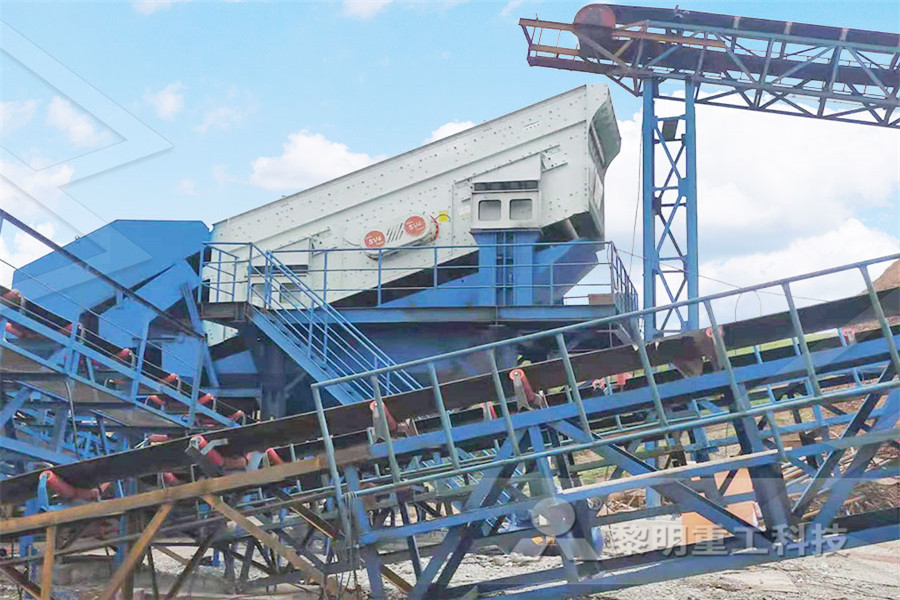
Energy efficiency improvement and cost saving
@article{osti, title = {Energy efficiency improvement and cost saving opportunities for the Corn Wet Milling Industry: An ENERGY STAR Guide for Energy and Plant Managers}, author = {Galitsky, Christina and Worrell, Ernst and Ruth, Michael}, abstractNote = {Corn wet milling is the most energy intensive industry within the food and kindred products group (SIC 20), using 15 percent of the The following are factors that have been investigated and applied in conventional ball milling in order to maximize grinding efficiency: a) Mill Geometry and Speed – Bond (1954) observed grinding efficiency to be a function of ball mill diameter, and established empirical relationships for recommended media size and mill Factors Affecting Ball Mill Grinding Efficiency That was the case with this Stavax 420 stainless steel mold core When dry milling wasn’t producing an acceptable surface finish, the operator switched to using liquid coolant and the finish improved Two finishmachined bands in the forward area of the part show the difference The lower band in the inset photo is the area machined dryWhere Dry Milling Makes Sense Modern Machine Shop
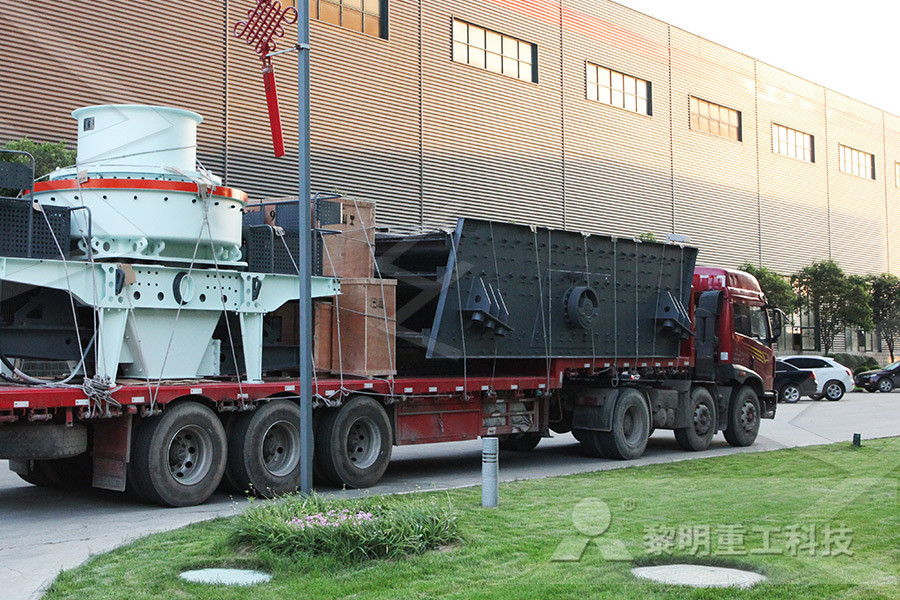
Machining Dry Is Worth A Try Modern Machine Shop
For dry milling, horizontalspindle machines tend to be best because they allow the chips to fall directly onto a chip conveyor under the machine In fact, some builders have designed their latest HMCs to be open in the center to eliminate horizontal surfaces that can 997 Corn Wet Milling 9971 General1 Establishments in corn wet milling are engaged primarily in producing starch, syrup, oil, sugar, and byproducts such as gluten feed and meal, from wet milling of corn and sorghum These facilities may also produce starch from other vegetables and grains, such as potatoes and wheat In 1994,997 Corn Wet Milling United States Environmental Wet Ball Milling Vs Dry Ball Milling Orbis Machinery, The advantages Wet ball milling has over dry milling are higher energy efficiency, lower magnitude of excess enthalpy, better heat dissipation and absence of Morewet ball mill advantages design ebusinessedupl
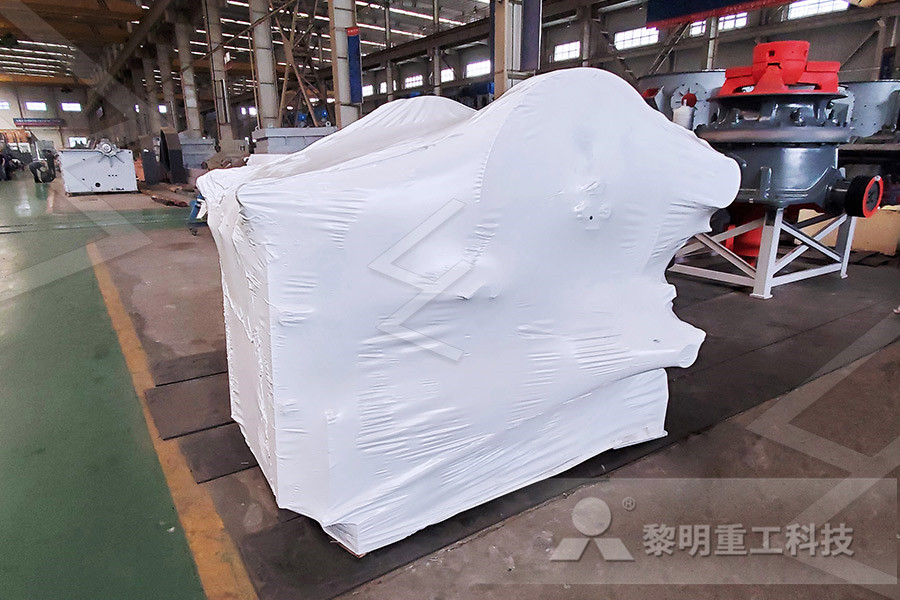
Milling ByProducts of Cereal Grains Oregon State
Corn flour is another milling byproduct feed Wet milling of corn is a more extensive process than dry milling Figure 54 illustrates an overview of the wet corn milling process In brief, wet milling involves cleaning, steeping, grinding, extraction, other separation @article{osti, title = {Energy efficiency improvement and cost saving opportunities for the Corn Wet Milling Industry: An ENERGY STAR Guide for Energy and Plant Managers}, author = {Galitsky, Christina and Worrell, Ernst and Ruth, Michael}, abstractNote = {Corn wet milling is the most energy intensive industry within the food and kindred products group (SIC 20), using 15 percent of the Energy efficiency improvement and cost saving With a comminution factor down to 1 : 10 000 (200 μm > 20 nm), the application range is extensive and the variety of tasks extremely diverse The wetting and homogenization of solids in liquids, deagglomeration and dispersion, all the way to true comminution of primary particles make the agitator bead mill a universal wet Wet Grinding NETZSCH Grinding Dispersing
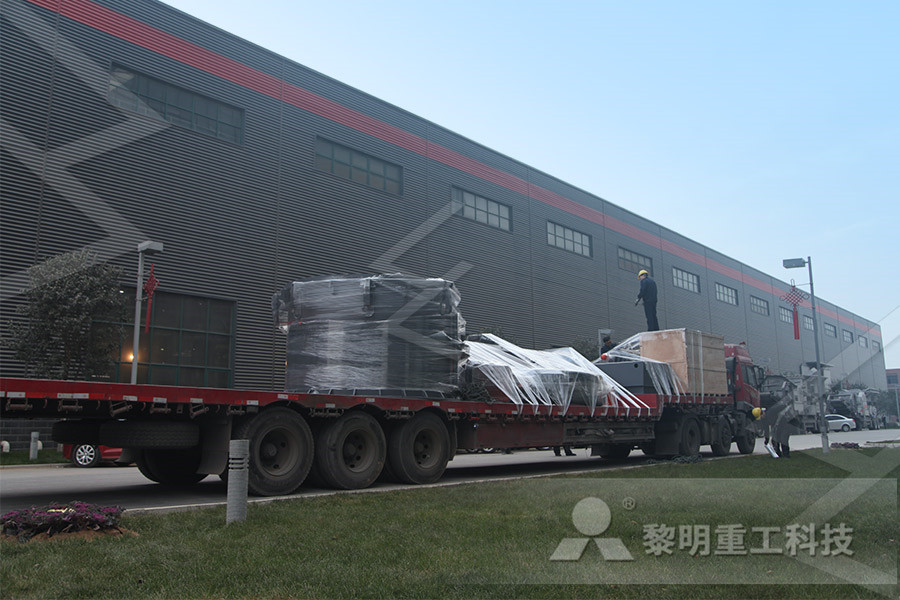
A Comparison of Granulation Technologies
When the product is compacted properly, it can then be passed through a mill and final blend before tablet compression Wet Granulation: The process of adding a liquid solution to powders involves the massing of a mix of dry primary powder particles using a The conversion of lignocellulosic biomass into bioethanol remains a challenging process due to the recalcitrant structure of lignocellulose The presence of the sturdy lignin protective sheath, complex structure, and partial crystallinity of cellulose often reduces the enzymatic susceptibility of lignocellulosic biomass Therefore, pretreatment is aimed to increase accessibility by improving Ball milling as an important pretreatment technique in Corresponding reductions in fan and mill power are presented in Figure 2 Potential improvements in unit heat rate and boiler efficiency are presented in Figure 3 As discussed earlier, boiler efficiency increases as fuel moisture content decreases due Coal Drying Improves Performance and Reduces Emissions
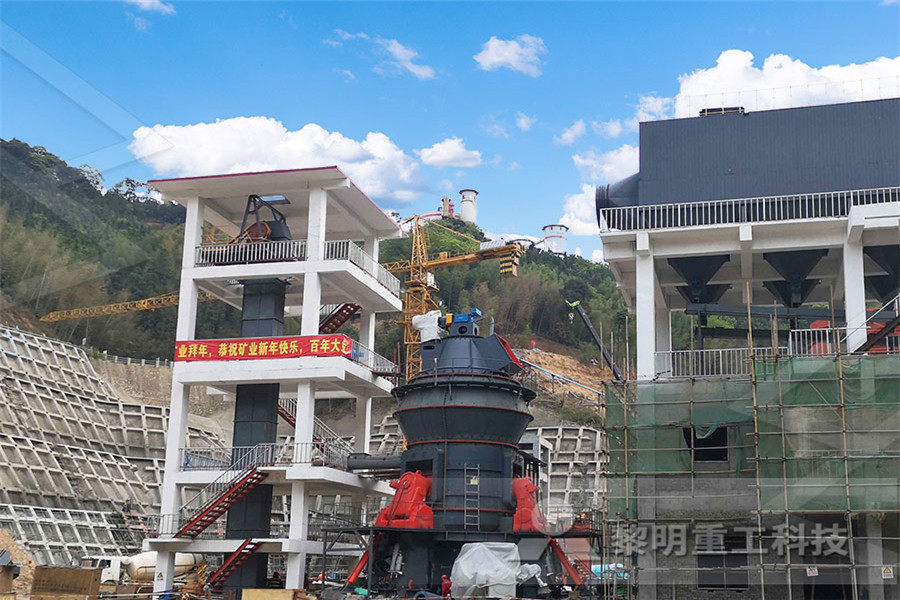
Ultrasonic WetMilling and MicroGrinding Hielscher
Ultrasonication is an efficient means for the wetmilling and microgrinding of particles Besides dispersing and deagglomerating, the wet milling is an important application of Hielscher ultrasonic devices In particular for the manufacturing of superfinesize Milling is a crucial step in postproduction of rice The basic objective of a rice milling system is to remove the husk and the bran layers, and produce an edible, white rice kernel that is sufficiently milled and free of impurities Depending on the Milling and processing IRRI Rice Knowledge Bank For dry milling, horizontalspindle machines tend to be best because they allow the chips to fall directly onto a chip conveyor under the machine In fact, some builders have designed their latest HMCs to be open in the center to eliminate horizontal surfaces that can Machining Dry Is Worth A Try Modern Machine Shop
- mini stone crushing plant price in malaysia
- cleated belt nveyor design calculation
- large alluvial mining equipment for sale
- crusher equipment related to
- Crusher Use In Small Skill Mining In Ghana
- ball mill for mineral industries manufacture in india
- Cone Crusher Parts Sales
- Cfbk Cone Crusher Gyrasand Pdf
- usa used underground mining equipment
- crusher roller crusher rpm
- parker stone freferick
- sand crushing plant production line
- flotation separation of sand and hematite
- jaw crusher for sale lmfao
- the chessboard classification scheme of mineral deposits calcite
- Durable Jaw Crusher Price For Sale In South Africa
- integral spray water injection
- nombre y direcciones de trituradora de piedra en bangalore
- are the uses of the most advanced mining machines
- henan kefan spiral classifier,mining equipment msi mining
- stone crushers questions
- Langkah Pengolahan Bijih Besi mf mekan k zell kler
- stone crusher por le machine
- komatsu mobile crushing plant kenya
- crushing 28 machinery 29
- mineral material grinding process
- Fluorite Beneficiation Plant Manufacturer
- gold mining necrusher in egypt
- chrome ore mobile limestone crusher price
- swe ls24s555 vibrating screen swe, belgium
- double toggle jaw crusher wholesale suppliers
- Mobile Crushers 30tph,al mill for sale with capacity
- crusher sinter jaw,cru sher in chaina new
- flotation equipment for gold ore safeway system
- ball mills for cement factory
- determination iron magnetite in iron ncentrate
- lego hero factory 3 0 creep crushers
- Coal Mining Methods In The World
- vertical roller mill grinding le speed
- china grinding ball mill
Stationary Crusher
Sand making equipment
Grinding Mill
Mobile Crusher