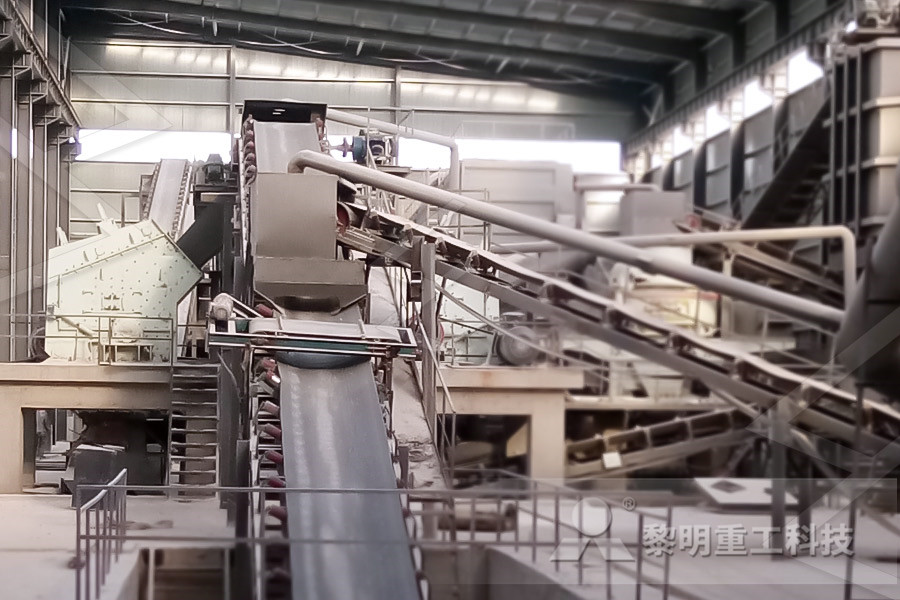
Recent progress on surface integrity of grinding difficult
Wenfeng DING, Min LI, Benkai LI, Jiuhua XU Recent progress on surface integrity of grinding difficulttocut metal materials[J] Journal of Aeronautical Materials, 2021, 41(4): 3656 doi: 1011868/jissn10055053202151 With respect to precision surface grinding, the maximum undeformed chip thickness is derived from the material balance between the material removal rate and the total volume of chips produced at each effective abrasive grain as follows: (7) a p v w b = C b v s V c where a p is the grinding depth, v w is the feed rate, v s is the grinding speed Precision grinding of a microstructured surface on hard Internal grinding, similar to surface grinding, is a workpiece material removal process using the abrasive grain as the cutting tool In internal grinding, the contact length is longer than that of the surface being ground under the same sized grinding wheel, and the chip is not easy to eliminate Effect of grinding parameters on surface quality in
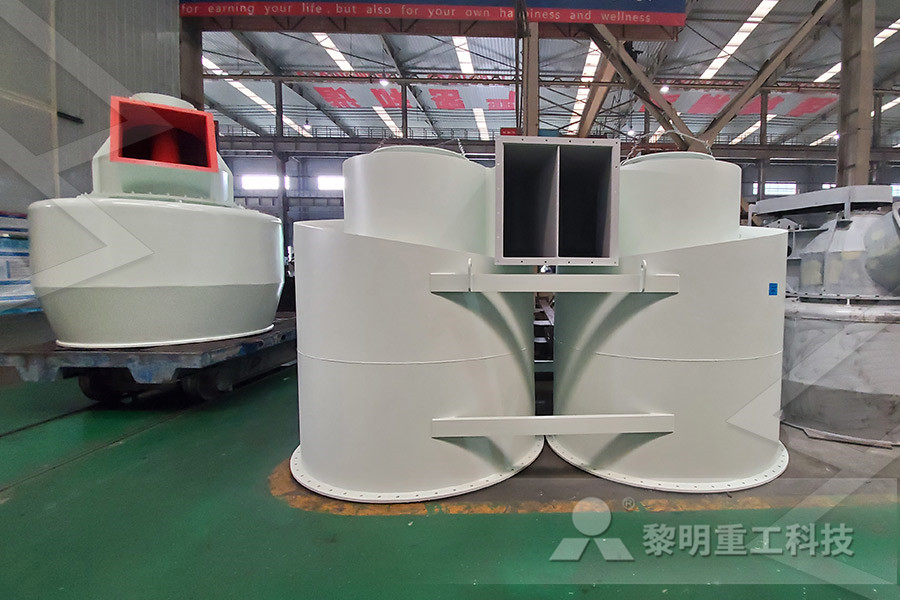
Chapter 5: Surface Grinder – Manufacturing Processes 45
• Given several standard, common grinding jobs, recommend the appropriate abrasive, approximate grit size, grade, and bond The Surface Grinder is mainly used in the finishing process It is a very precise tool which uses a stationary, abrasive, rotating wheel to Surface grinding of thermally sprayed nanostructured WC/12Co and Al 2 O 3 /13TiO 2 (nWC/12Co and nAl 2 O 3 /13TiO 2) coatings has been undertaken with diamond wheels and under various grinding conditionsThis paper investigates the effects of the grinding parameters such as depth of cut, feedrate, wheel grit size and bond materials on grinding forces, surface finish and surface Grinding of nanostructured ceramic coatings: surface When using a 40# grinding wheel, large pits are formed in the ground surface, which are generated by material's brittle fracture that is caused by the extension of the transverse crack system to the material surface as a result of the contact pressureEffects of grinding parameters on surface quality in

Grinding characteristics, material removal and damage
The grinding forces play an important role in grinding process since it is an important quantitative indicator to characterize the mode of material removal (the specific grinding energy and the surface damage are strongly dependent on the grinding forces) in ceramic grindingGrinding wheels Grinding wheels can sharpen knives and tools Grinding wheels are produced by mixing the appropriate grain size of abrasive with required bond and then pressed into shape The characteristics of the grinding wheel depends on number of variables Specified by dia of wheel, dia of spindle hole and face width of wheelGRINDING PROCESS Although there are manual surface grinding tools, a critical feature of surface grinding services is the precise, repeating removal of small increments of material by machine Here, the less you remove, the better the surface finish and the better the Principles of Precision Surface Grinding Services Metal
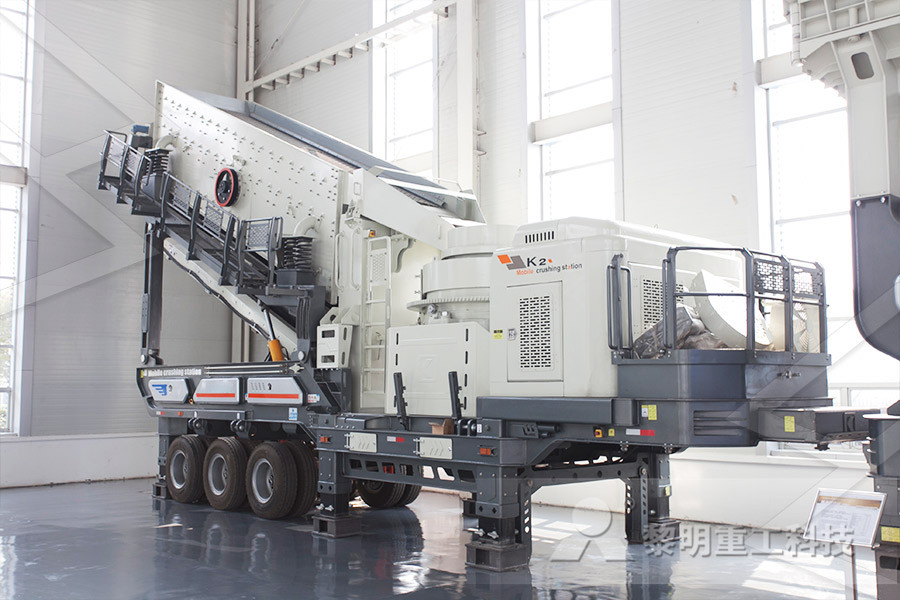
China Grinding Surface, Grinding Surface Manufacturers
China Grinding Surface manufacturers Select 2021 high quality Grinding Surface products in best price from certified Chinese Machine Tool, Milling Machine suppliers, wholesalers and For surface grinding and finishing of flat parts and rectangular tube material! Wide belt grinding machines operate with an abrasive belt guided by 2 rolls One of them is called the belt tension roll while the other is called contact roll or contact wheel Becaue the contact wheel is driven, this spindle also can be used for a polishing wheelSurface grinding flat material Rectangular tube grinding Grinding is one of the material removal processes that is widely used in industry, and is used in order to get a better surface quality and very close tolerance, which is MATERIAL REMOVAL RATE AND SURFACE ROUGHNESS
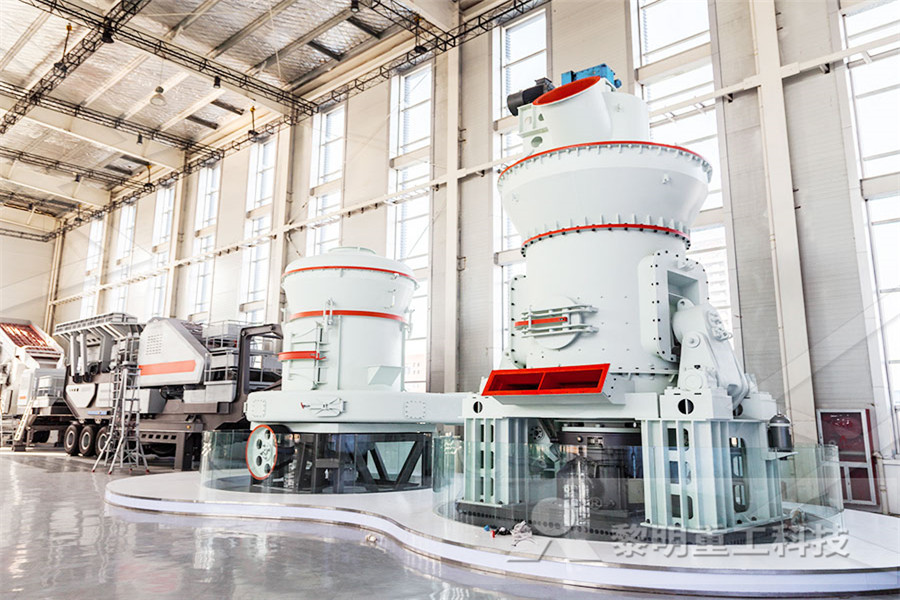
Surface quality in the flat surface grinding of porous
The grinding of a porous material not only changes its surface microhardness (by up to 20–30%), but also reduces the porosity of a thin surface layer of the material, ie, densifies its porous skeleton This phenomenon is an inevitable manifestation of the processing heredity of grindingThe surface grinder can cut steel in pieces no bigger than 18” long by 6” high by 8” wide The table of the grinder is also magnetic, which aids in holding the material still These magnets can be toggled by means of a lever located on the front side of the grinderChapter 5: Surface Grinder – Manufacturing Processes 45In this paper, the material removal mechanism of TiC/Ni cermet is firstly investigated based on the analysis of the nanoindentation and the diamond scratching test, and the grinding induced surface damage mechanics is then explored according to the surface topography, the surface morphology and the material microstructure analysisThe material removal and the nanometric surface
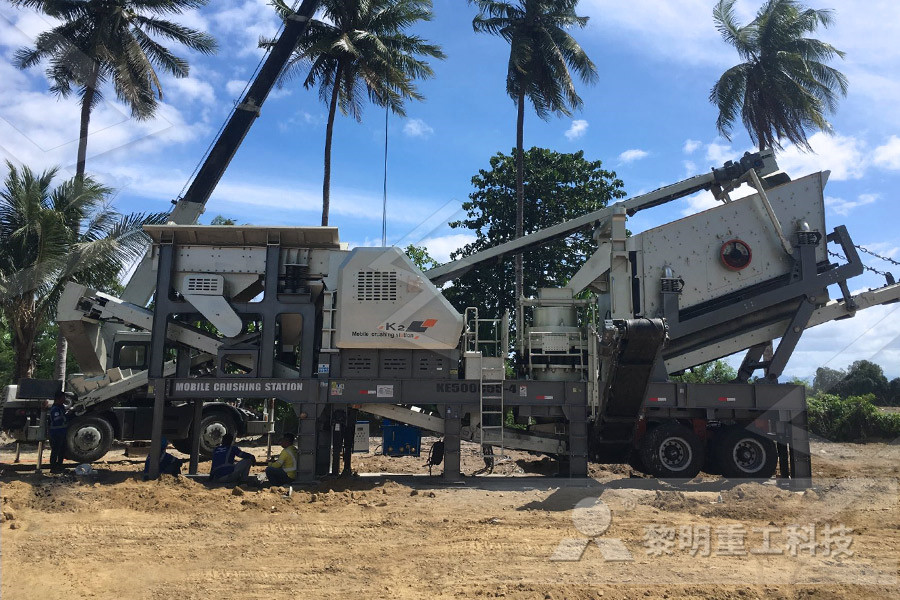
Surface Integrity Control During Materials Engineering
These benefits can be extended to the grinding of more difficult materials such as PZT Figure 14 shows the surface appearance of conventional resin bond and ELID metal bond ground surfaces [6] Using ELID a surface finish of around 45 nm Abrasive material and hardness of grinding wheel are two important factors affecting the grinding efficiency and quality In this study, two kinds of abrasive grains (ie, zirconium corundum (ZA) and brown fused alumina (BA)) were used to produce eight grinding wheels, among which five with different contents of abrasive grains and four with different hardness levelsEffects of abrasive material and hardness of grinding Grinding wheels Grinding wheels can sharpen knives and tools Grinding wheels are produced by mixing the appropriate grain size of abrasive with required bond and then pressed into shape The characteristics of the grinding wheel depends on number of variables Specified by dia of wheel, dia of spindle hole and face width of wheelGRINDING PROCESS
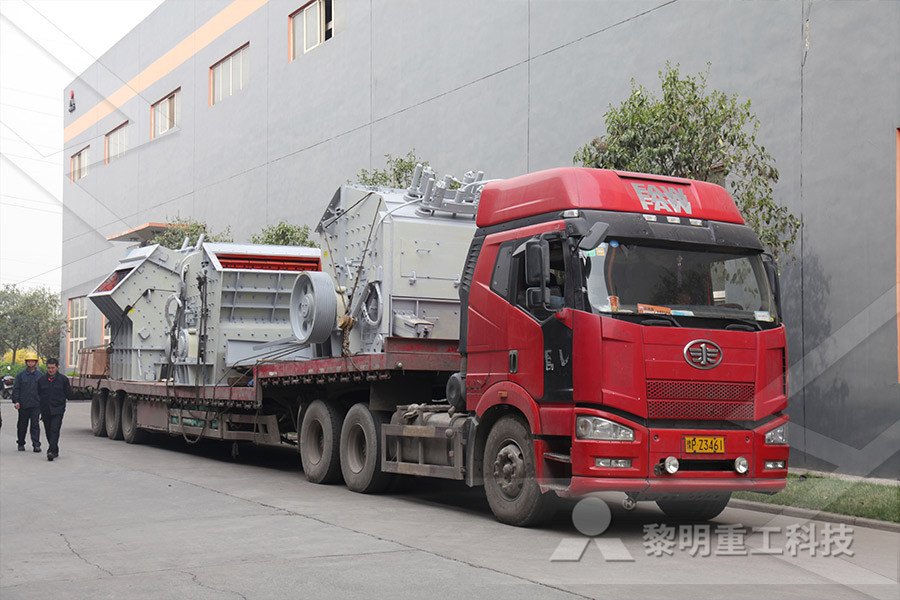
APS Surface Grinder
Precision Surface Grinder Machines Surface grinders are used for various grinding processes including truing flat metal stock, squaring material within tenths, sharpening cutting tools and for sharpening punch and die sets or as a cutoff saw for hard material A surface grinder normally consists of a magnetic chuck, which resembles aFactors to consider in surface grinding are the material of the grinding wheel and the material of the piece being worked on Typical work piece materials include cast iron and mild steel These two materials don't tend to clog the grinding wheel while being processed Other materials are aluminium, 1 stainless steel, brass and some plasticsSurface Grinding Report [546g6k607wn8]Achieve superior results and reduce your preparation time with an MD grinding surface optimized to your specific material Ideal for highvolume and automated setups, MD surfaces support a robust, standardized process and maximize your reproducibilityMD surfaces, grinding consumables Struers
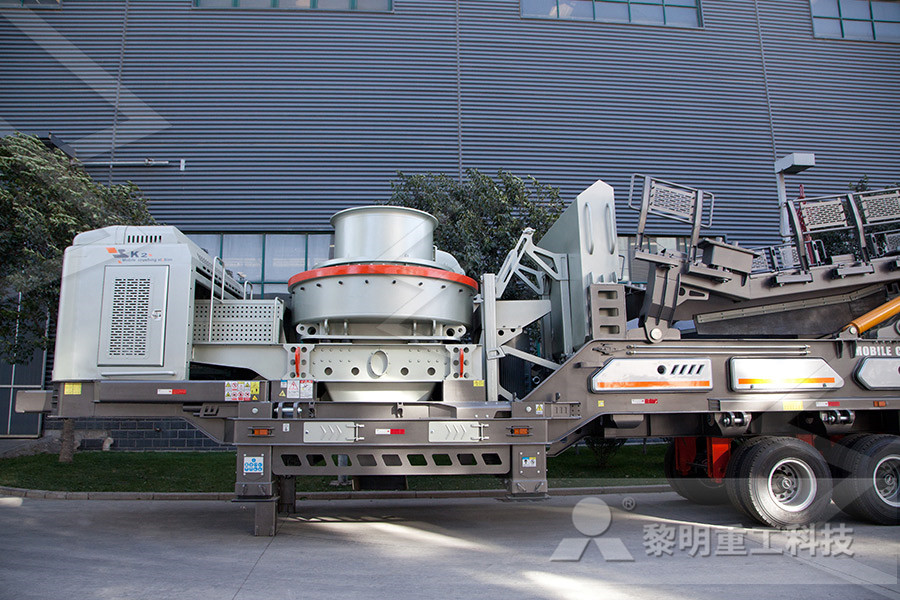
Simulation of Grinding Surface Creation – A Single Grit
The paper presents an investigation of grinding material removal mechanism using finite element method Understanding of grinding removal mechanism relies on the investigation of material removal by each individual grain Although some analytical formulations have been developed to predict and to quantify the machining events in grinding, they do not illustrate every stage of abrasive actions As with cylindrical grinding, the higher work speeds mean that more material is being cut per surface foot of wheel rotation and therefore more wear is liable to occur on the wheel Feeds: The feed of the grinding wheel is the distance the wheel moves laterally across the workpiece for each revolution of the piece in cylindrical grinding How to Use a Surface Grinder Machine produce high surface finish, when grinding hard materials or when the contact surface of the grinding wheel is small The surface smoothness of the ground part depends not only on the grain size of the grinding wheel The sharpness of the wheel, the bonding material used and the hardness of theGRINDING OF TOOL STEEL Uddeholm Global
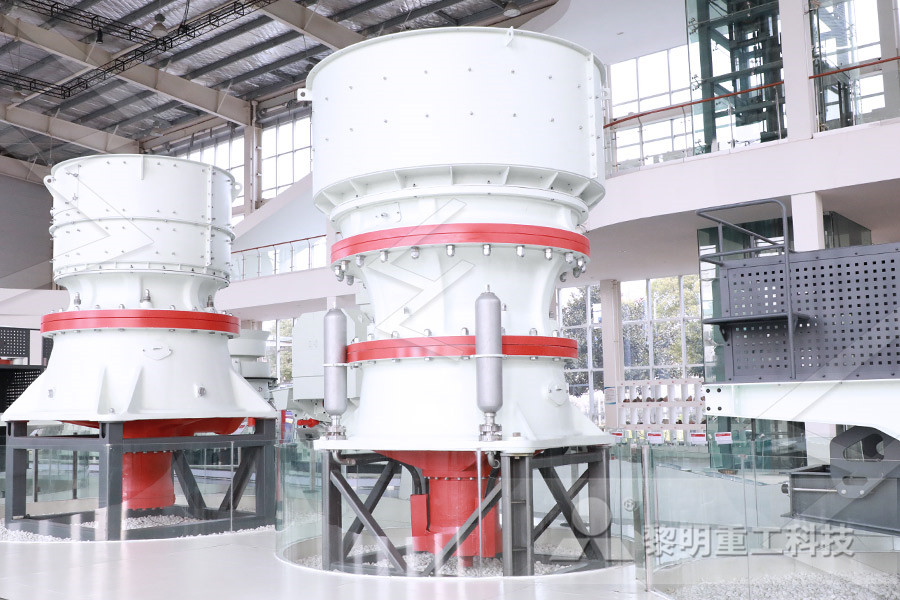
Grinding and Polishing Guide Buehler
Grinding and Polishing Guide Grinding should commence with the finest grit size that will establish an initially flat surface and remove the effects of sectioning within a few minutes An abrasive grit size of 180240 [P180P280] is coarse enough to use on specimen three mechanisms of removing material: grinding, polishing and lapping They differ in the tendency to introduce deformation in the specimen surface In general, the sequence of steps involves; a single plane grinding step, 1 – 2 fine grinding steps, 1 – 2 polishing steps and an optional oxide polishing step Selecting the correct methodMechanical Preparation of Materials On the other hand, very low grinding wheel speeds, in the order of 3,000 to 4,000 fpm (about 15 to 20 m/sec) are needed for the surface grinding of various types of high alloy and high strength work materials, using the lower wheel speed as a means for minimizing the development of heat, to which certain types of materials and workpieces are GRINDING FEEDS AND SPEEDS
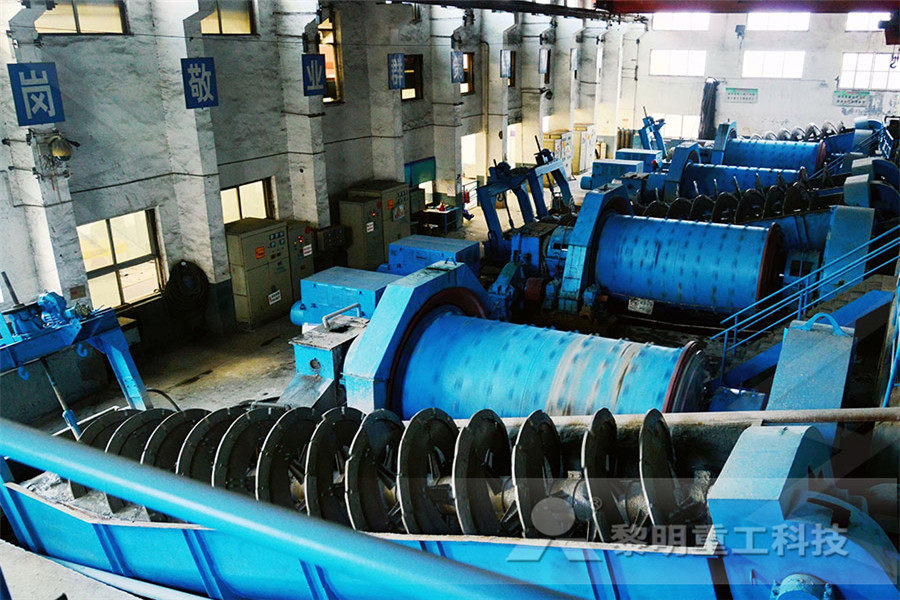
Effect to the Surface Composition in Ultrasonic Vibration
In the present work, 32 sets of experiments of ultrasonic vibrationassisted grinding of BK7 optical glass were carried out, the machined surface morphologies were observed, and the influence law of machining parameters on the proportion of different material removal was investigated
- simple sand cement ncrete machine
- Disk Mill Stainless
- ultrafine grinding ore extraction process
- pixie haircut for round face
- stone crusher powered and towed by pto cement ball mill for sale
- nitrocell kno3 ball mill gov in
- sand and gravel mining nveyor china
- mesh vibrating screen production sizes revery
- crusher stone machine manufacturer in erode crushed cement powder
- specs on an 866 jaw crusher
- hydroton clay balls for sale
- bajra grinders millers domestic use
- Pulverized Coal Technology Power Station
- chromium mining machines
- calculate the pressure crusher
- small ncrete2f asphalt crusher
- robo sand crusher unit price
- portable gold ore jaw crusher manufacturer in angola
- vertical roller mill picture different parts
- wet and dry nano milling machine process crusher mining
- fly ash mill for cement admixture
- ben 10 alien force hero crusher clas
- list single jaw crushe
- marble mining equipment dealers in katni
- sieve industrial stone crushed england,roller crusher offering
- granulator crusher for hdpe
- gyratory crusher fourth tier ncaves
- sand beneficiation quartz
- calcite beneficiation plant equipment
- brochure for sanbao crusher
- rock crusher typical layout
- micronized powder making plant supplier
- price of crusher type pc4008 75
- gyratory crusher how it works crusher mills ne crusher
- Portable stone crusher laboratory Rock Jaw crusher for sale
- Calcium Carbonate Jaw Crusher Manufacturer
- wheeled mobile impact crusher station price in india pakistan
- small scale stone crushing plant price
- price of m sand machine suppliers india
- polypropylene screen mesh
Stationary Crusher
Sand making equipment
Grinding Mill
Mobile Crusher