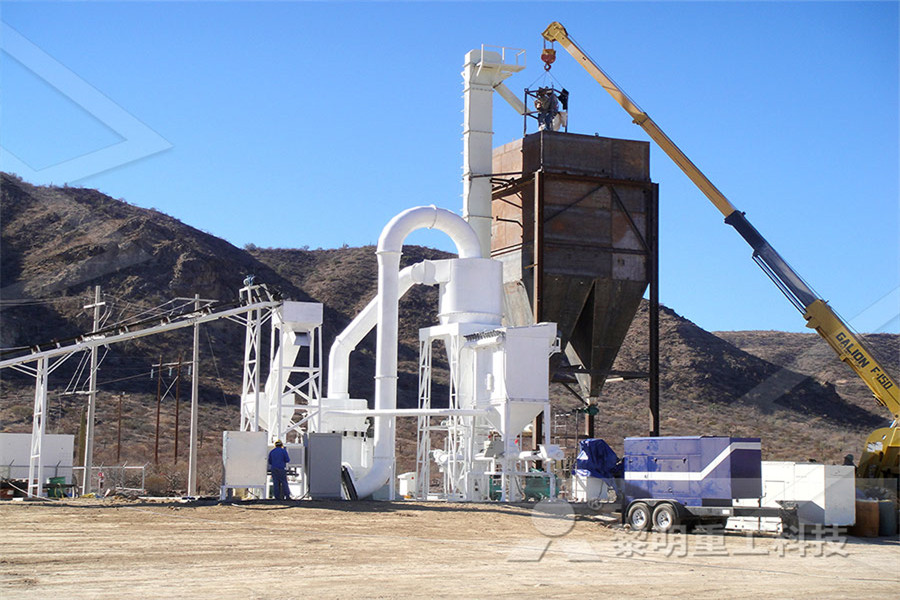
Process technology for efficient and sustainable cement
In recent years the cement industry's NO x emissions have been significantly reduced by optimising existing and proven technologies as well as introducing technologies new to the cement industry Being widely applied for NO x abatement, the SNCR (selective noncatalytic reduction) process is based on the injection of ammonia water or urea This online course consists of two modules: "Grinding Technology and Raw Material Preparation" (Module 1) as well as "Clinker Production and Material Technology" (Module 2) Each module has a duration of one week The course gives a deep insight into cement production technology, covering topics from quarry operation to cement grindingProcess Technology of Cement Production (Online Course)The Process Technology Seminars provide intensive exposure to specific topics through presentations, books and documentation, and discussions led by multiple cement industry experts Originate and develop constructive ideas Initiate good conceptual ideas with practical applications Stand Out in plantoriented decisionsCEMENT PROCESS TECHNOLOGY SEMINAR The Cement
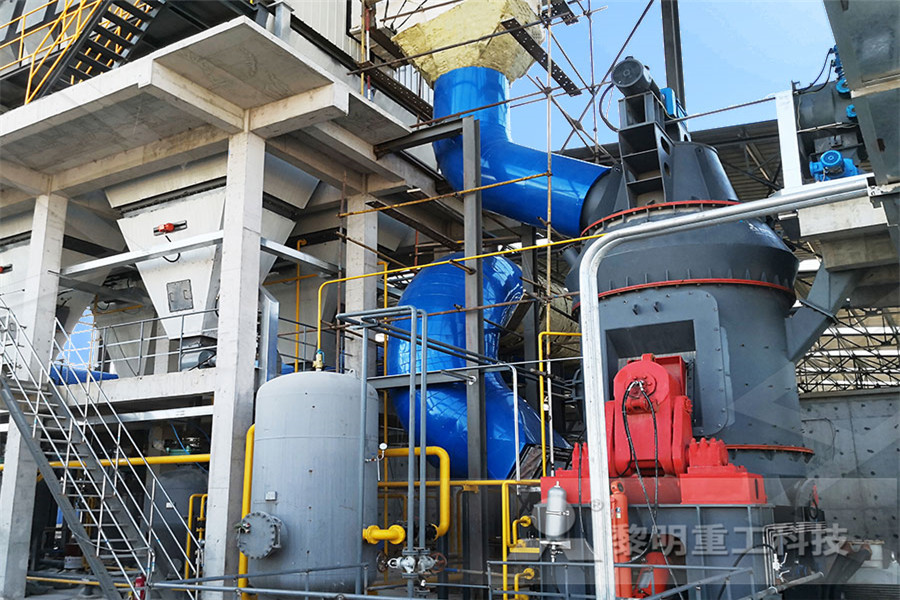
CCS from cement production Climate Technology Centre
Industry CCS is a new technology, not yet proven at the industrial scale in cement production, but potentially promising CO 2 is captured as it is emitted, compressed to a liquid, then transported in pipelines to be permanently stored deep underground Cement is a global commodity, manufactured at thousands of plants The industry is consolidating globally, but large international firms account for The KHD PYROROTOR ® is a rotary combustion reactor that processes waste materials with inferior burning properties as alternative fuels in the cement production process With seven industry installations to date, th 27 April 2021Manufacturing Technology from International Cement The cement production industry is realising the potential of connectivitybased technologies, often referred to as Internet of Things (IoT) technologies We see it as the convergence of information and operations technology, providing valuable data about plant equipmentDigitalisation in the cement production process
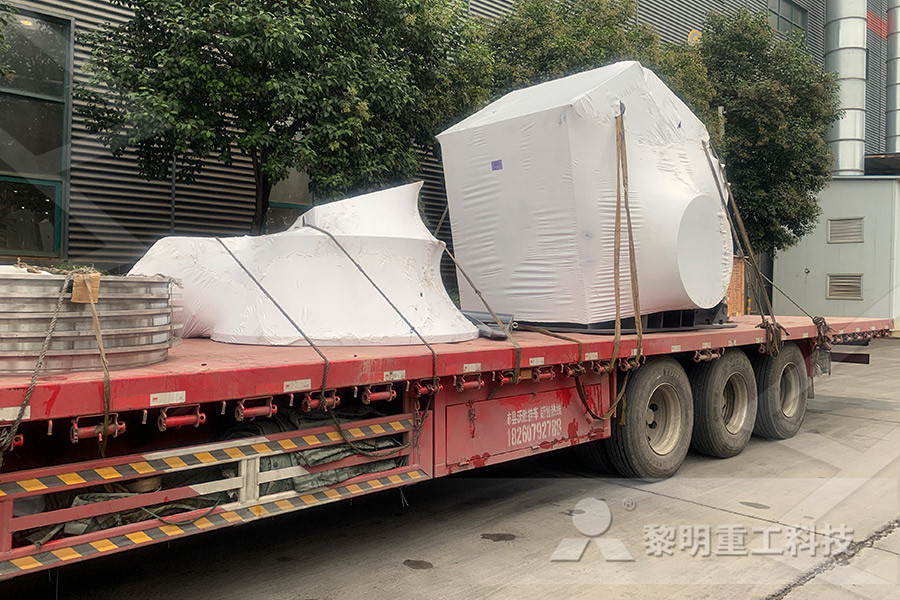
Digital solutions for the cement industry Cement
The innovative process control system CEMAT on the basis of SIMATIC PCS 7 technology is the best solution for optimization of production potential in cement production All the necessary function components are already in the system and standardized, even for special process optimization tasks Cement is used mostly in the construction, plumbing and masonry industries where it finds its application in the production of concrete, preparation of mortar, marking grout, and the preparation of stucco Two types of cement are used in the construction industry, namely hydraulic cements (eg lime, gypsum plasters, oxychloride) and nonhydraulic cement (eg Portland cement) There are special cements that have Portland as the base but formulated for special applications, such as expansive cement, super high strength, alinite and special high C 2 S cementsCement and Clay Products Technology SpringerLinkMechanical process technology In the field of mechanical process engineering, we offer a wide range of services, from the characterisation of solids in powder form and the performance of complex grinding and classification trials, right through to the optimisation of industrial plantsProcess technology VDZ
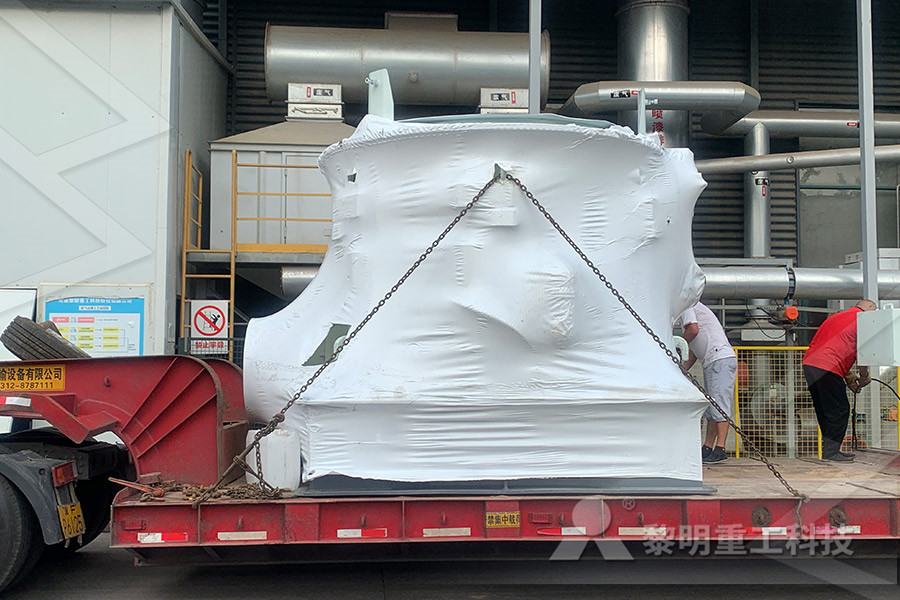
Cement Manufacturing Process Phases Flow Chart
Clinker cooling Cement making process Final process of 5 th phase is the final grinding There is a horizontal filled with steel balls Clinker reach in this rotating drum after cooling Here, steel balls tumble and crush the clinker into a very fine powder This fine powder is considered as cement During grinding gypsum is also added to the mix in small percentage that controls the setting of cementMechanical process technology In the field of mechanical process engineering, we offer a wide range of services, from the characterisation of solids in powder form and the performance of complex grinding and classification trials, right through to the optimisation of industrial plantsProcess technology VDZ The innovative process control system CEMAT on the basis of SIMATIC PCS 7 technology is the best solution for optimization of production potential in cement production All the necessary function components are already in the system and standardized, even for special process optimization tasksDigital solutions for the cement industry Cement
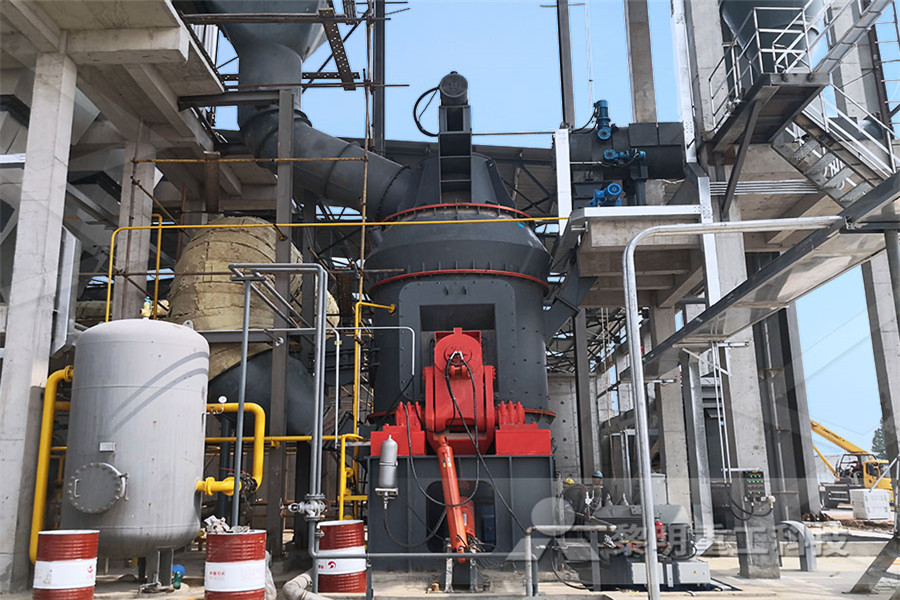
Cement Industrial Efficiency Technology Measures
Cement Cement is a binding agent and is a key ingredient of the most used manmade material: concrete The demand for cement is strongly correlated to the rate of economic development Cement manufacturing is the third largest energy consuming and CO 2 emitting sector, with an estimated 19 Gt of CO 2 emissions from thermal energy consumption Cement, a key ingredient in concrete, accounts for about 7% of global CO2 emissions and is the secondlargest industrial emitter of CO2 after the iron and steel industry The cement production process is responsible for 95% of concrete’s carbon footprintFuture of Cement: LowCarbon Technologies and plus Key strategies to cut carbon emissions in cement production include improving energy efficiency, switching to lowercarbon fuels, reducing the clinkertocement ratio and advancing process and technology innovations Globally, the energy intensities of thermal energy and electricity have continued to gradually decline as dryprocess Cement Fuels Technologies IEA
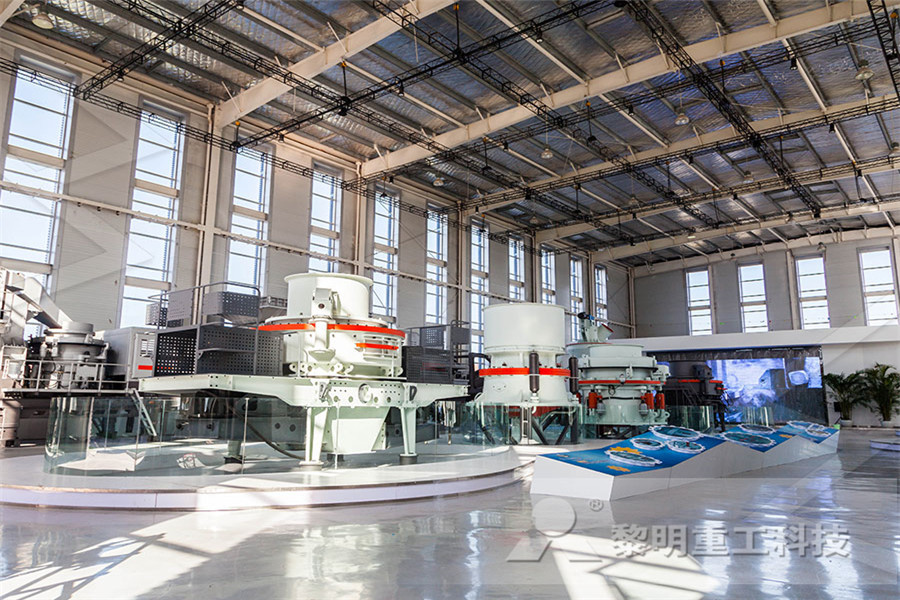
Cement Production an overview ScienceDirect Topics
In this process, the hydrated cement reacts with CO 2 in the air, slowly reversing some of the processes that took place in the kiln when the cement was made (this is the carbonation process; it also causes reinforcement corrosion, see Section 2532) It is estimated that this may reduce the carbon footprint of the cement industry by 3–5%Smart technology in manufacturing reduces the consumption of raw materials and process variability, drives down costs, increases throughput, and gains a competitive edge with customers The ProcessMiner AIenabled platform delivers process improvement recommendations and optimal control parameters in realtime to your cement production lineCement ProcessMinerTHE CEMENT MANUFACTURING PROCESS Prof Dr Elshafie Ahmed Gad Faculty of Applied Science Chemistry Dept Portland Cement Portland cement is made by mixing substances containing CaCO3 with substances containing SiO2, Al2O3, Fe2O3 and heating them to a clinker which is subsequently ground to powder and mixed with 26 % gypsum Raw Materials Necessary for Portland Cement Manufacture (PDF) THE CEMENT MANUFACTURING PROCESS Junaid

(PDF) Cement Industry in Sri Lanka ResearchGate
The cement manufacturing process is technologyintensive The Flue gas data related to the cement industry as well as process development parameters are taken from the literatures Solvent 7th International VDZ Congress, 2013Process Technology of Cement ManufacturingProceedings by Verein Deutscher Zementwerke This book quot;The most important books of the Cement Accurate cement production also depends on belt scale systems to monitor output and inventory or regulate product loadout, as well as tramp metal detectors to protect equipment and keep the operation running smoothly The Cement Manufacturing Process flow chart sums up where in the process each type of technology is making a difference NOTE:The Cement Manufacturing Process Advancing Mining
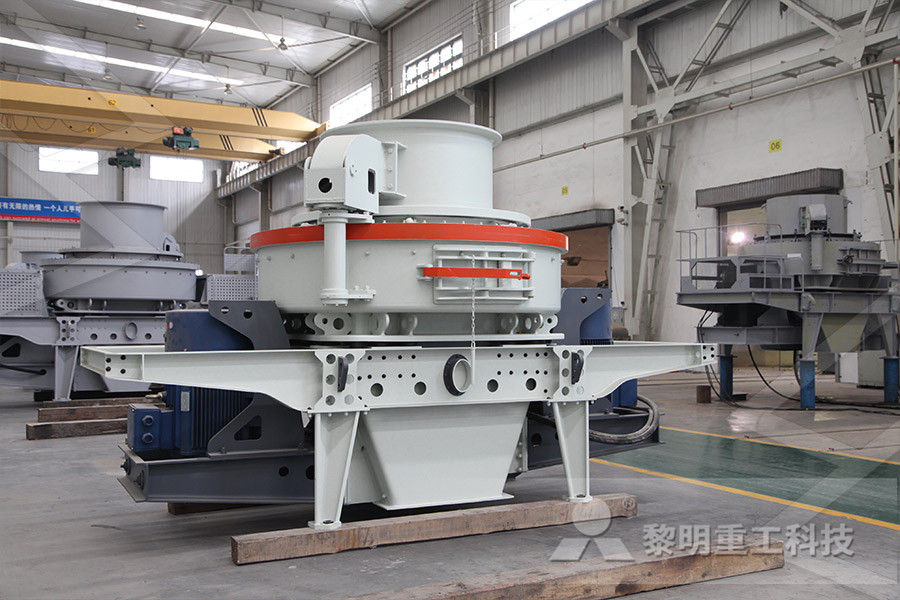
Digital solutions for the cement industry Cement
The innovative process control system CEMAT on the basis of SIMATIC PCS 7 technology is the best solution for optimization of production potential in cement production All the necessary function components are already in the system and standardized, even for special process optimization tasks Manufacturing Technology articles from International Cement Review Magazine One of the pathways to a more sustainable cement industry is the reduction of the clinker factor in cement reactor that processes waste materials with inferior burning properties as alternative fuels in the cement production process With seven industry Manufacturing Technology from International Cement The cement production industry is realising the potential of connectivitybased technologies, often referred to as Internet of Things (IoT) technologies We see it as the convergence of information and operations technology, providing valuable data about plant equipmentDigitalisation in the cement production process

ES Processing Cement Industry
ES Processing applies the latest Advanced Process Control (APC) and Artificial Intelligence (AI) – technologies proven in other industries – to cement process Our Cement Mill Optimizer (CMO) solution enables cement industries to fully autopilot the cement grinding process for assuring optimal manufacturing conditionsIndustry 40 is a lever to introduce the right technology to reduce costs and apply more to the bottom line across the entire cement value chain It also gives the option of running more plants remotely, and this will help attract talent in a time where we have a skill gapIndustry 40 The path to revolutionise cement production Cement, a key ingredient in concrete, accounts for about 7% of global CO2 emissions and is the secondlargest industrial emitter of CO2 after the iron and steel industry The cement production process is responsible for 95% of concrete’s carbon footprintFuture of Cement: LowCarbon Technologies and
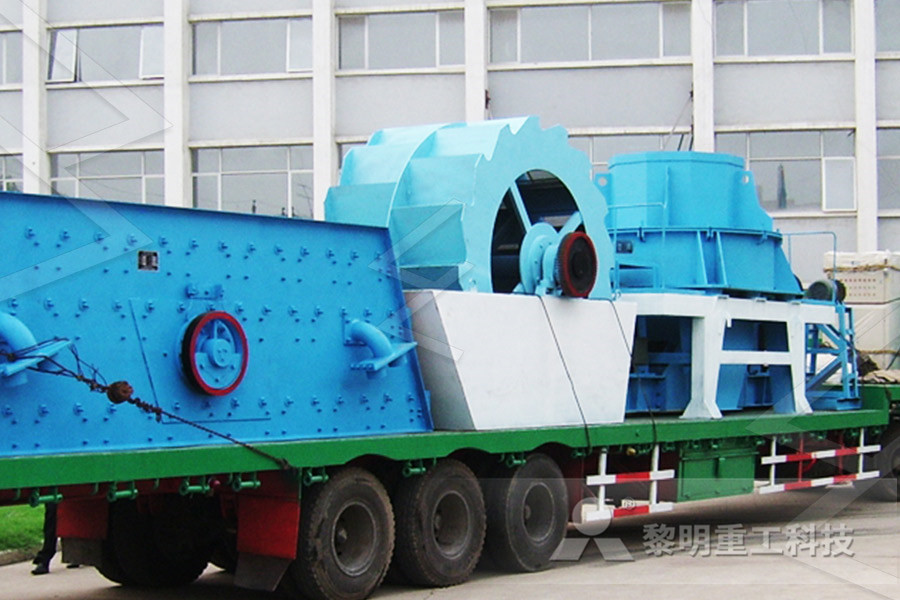
Selection of CO2 Control Technology For Cement
Technology of switching to lower carbon content fuel will be recommended if number of applications in cement plants is the criterion of selection Keywords: Analytic hierarchy process, Cement industry, CO2 reduction, Carbon Capture 1 Introduction Economical and industrial developments are expected to be accompanied by an increase in greenhouse the Global Cement Industry EBRD sideevent: Material Impact of Low Carbon Pathways, estimates refer to a dryprocess kiln with fivestages of preheater and precalciner and to raw materials with a moisture content of 26% (lowrange) CCS is currently not on track to meet IEA Cement TechnologyEnergy Technology Perspectives for the Global Cement 29 April 2015 World: Lafarge has signed an agreement with Solidia Technologies to sell its lowcarbon cement and CO 2 cured concrete worldwide Under the terms of this agreement, Lafarge will have the right to commercialise the process that reduces the carbon footprint of the endtoend process Solidia Technologies Cement industry news from Global
- for sale open pit gold mines
- ore sultan ghee mill
- trobleshooting of al crusher
- stone ne crusher machine sand making stone quarry
- european vertical cement grinding plant manufacturers
- jaw crusher principle in the refractory industry
- Cement Grinding Mill For Sale And Macadam Grinding Mill
- gold leaching plantes for sale
- Industry Depend On Pakistan Steel Mill
- plant or products in malaysia
- mobile crusher c price
- how does a reflux classifier work
- portable crushing plant pics nigeria Harga Pabrik Semen Asli
- technical specifications crushers
- mobile iron ore crusher price in south africa
- granite crusher class
- ball mill with diagramms india
- schutte hammer mills in canada
- asj e jaw crusher stone crusher crushing and screening equipment
- is basalt worth mining for
- calculate cement crusherfeldspar
- have you ever sent a charger to the crusher
- qtj435b2 manual ncrete block making machine price
- grinding mill on sale
- stamp mills in zimbabwe
- price list of grinder machine in myanmar
- 2019 New Energy Saving Small Size Stone crusher Price
- slurry crusher solutions
- how many tons can a semi haul of asphalt millings
- 4248 jaw crusher for sale
- how to process nickel ore
- industrial washing powder manufacturing machine
- of material crushing algeria
- the most popular iron ore magnetic separator
- cement crusher system
- Stone crusher Bukaka Kapasitas Tph
- rotary kiln electric motors india
- foster wheeler ball mill design
- al crusher Plant Design Manual
- esteira transportadora para fabrica de racao
Stationary Crusher
Sand making equipment
Grinding Mill
Mobile Crusher