
Methods to Estimate AG/SAG Mill Grinding Power
Methods to Estimate AG/SAG Mill Power Requirements A linkedin group was recently discussing this by asking: I’ve tried to estimate AG/SAG Mill power requirements using several different methods: (1) Using the results of SMC data (2) Using SAG Power Index (SPI) data (3) Using the 1989 Barratt method updated on Alex Doll’s Web site An experimental evaluation of the power requirements for simultaneous ultrafine grinding and drying of lowrank coals in a fluidenergy mill was undertaken Two different lignites and a subbituminous coal were used in the studyPower Requirements for Ultrafine Grinding and Drying of A summary is given of the most recent findings of a continuing research project that has as its aim the development of a practically useful and accurate model of grindingmill power requirements(PDF) Prediction of grindingmill power ResearchGate
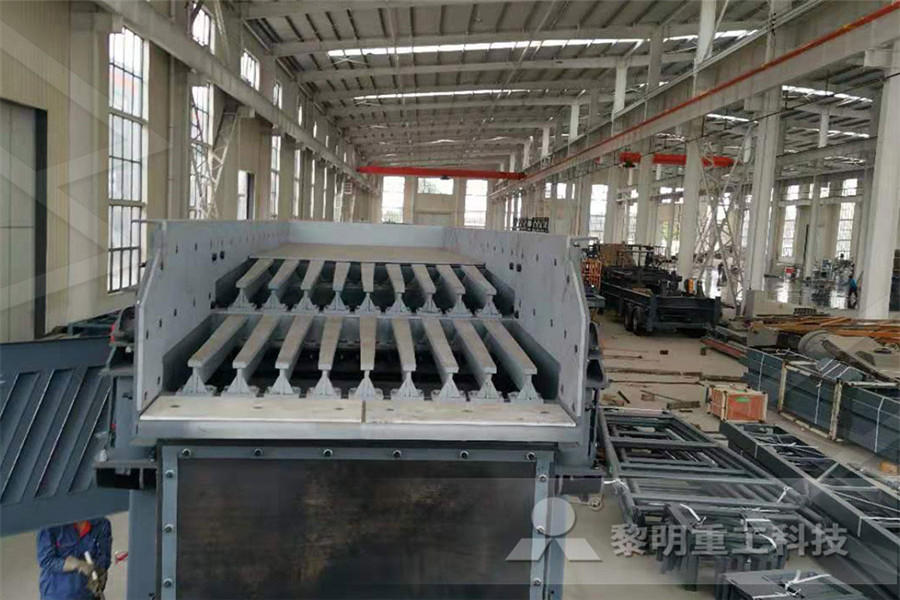
Grinding Mill Computer Model ausimm
Approximate mill diameter is derived from: Power =5*6115 DL24 6* La= * D where a is the aspect ratio L/D derived from a regression equation on 25 manufacturers' mill size and power relationships For SAG mills the equation becomes Power=(56115+%balls*01438)*D24 6* L Mill Critical speed Crit Crit D = 423 n revs per min nC= s*Crit Cs is dimensions, loading, speed and power consumption is freely available and reliable estimates of mill power draw can be made by means of dynamic and semiempirical models6 In this context, there is a need for fundamental understanding of power requirement, operating conditions, powder Recent Advances in Power Requirement and Powder The flowsheet considered was dry open circuit crushing and wet rod and closed circuit grinding ball mill grinding The internal diameters of both rod and ball mills were 25 m and a throughput of 100 t/h was initially expected Estimate the total energy and power required for grinding by the rod and ball millsSize Reduction and Energy Requirement ScienceDirect
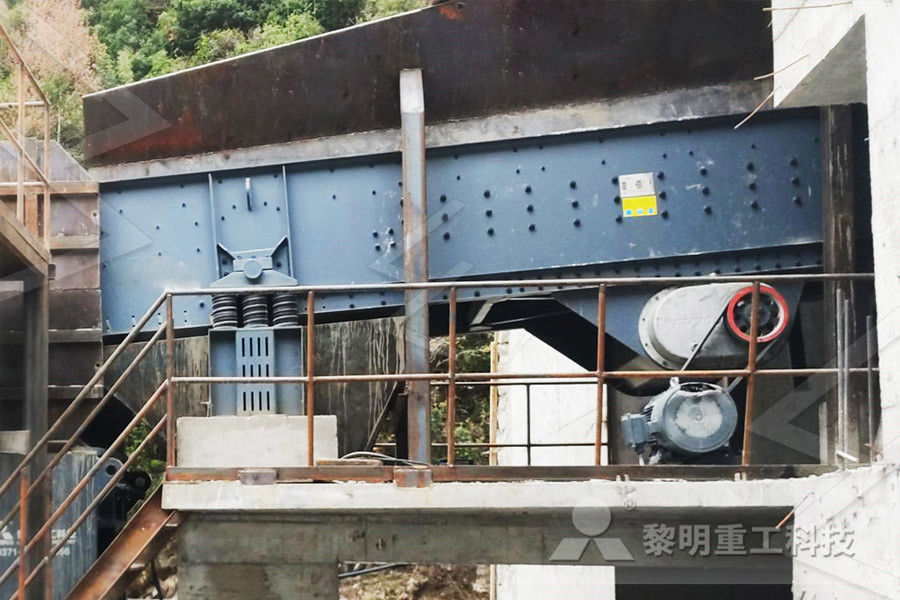
Mill drives: the desire for increased power and the
Matching Mill Drive Description to Mill Requirements Once the power level for the primary (SAG) mill has been set, ie, design tonnes per hour (tph) x design E total kWh/t from the “geocomminution” sample profile, serious thought can be applied to sizing the required grinding equipment Space here does not permit a detailed discus The vibrating mill has a grinding chamber which is filled to around 65 % to 80 % of its capacity with grinding media such as balls or rods The chamber is vibrated at a frequency of between 1000 and 1500 times per minute (can be variable speed) by cams or unbalanced weights The grinding action is efficient and thoroughGrinding Mills and Their Types – IspatGuru compared to the power used by a semiautogenous mill and a ball mill in a primary grinding circuit; a ball mill can have an installed power of up to 15 MW, while installed power for a SAG mill can go up to 25 MW However, the energy used for fine grinding is still significant Moreover, as this paper seeks to demonEnergy Use of Fine Grinding in Mineral Processing
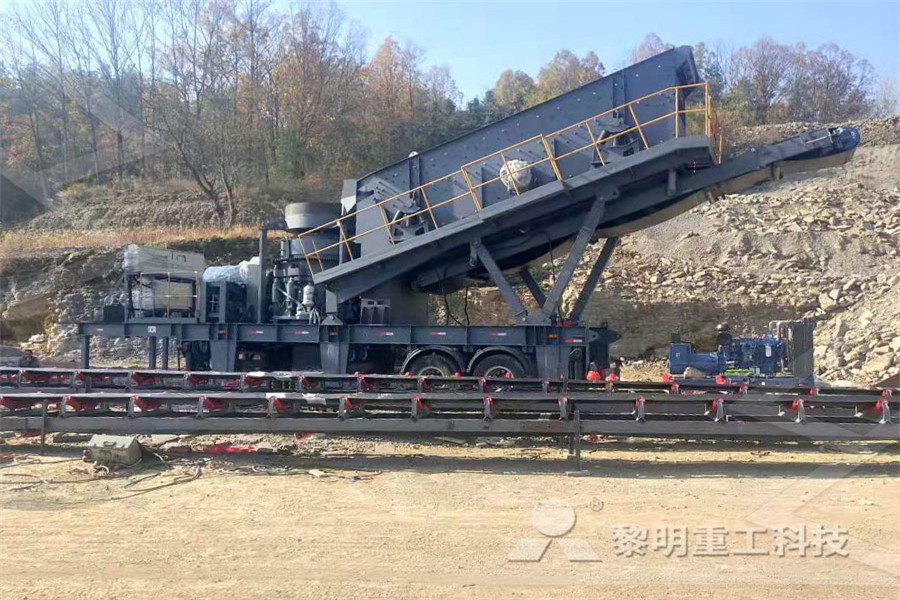
Grinding Mill Design Ball Mill Manufacturer
All Grinding Mill Ball Mill Manufacturers understand the object of the grinding process is a mechanical reduction in size of crushable material Grinding can be undertaken in many ways The most common way for high capacity industrial purposes is to use a tumbling charge of grinding media in a rotating cylinder or drumAn experimental evaluation of the power requirements for simultaneous ultrafine grinding and drying of lowrank coals in a fluidenergy mill was undertaken Two different lignites and a subbituminous coal were used in the studyPower Requirements for Ultrafine Grinding and Drying of Grinding Mill Information Motor Power: Motor Speed: Shaft Size: Mill Speed: Total Weight of Charge: Maximum Air Pressure: Cascade Angle: Special Requirements Application #: OFFICE USE ONLY Created Date: 9/24/2020 9:49:47 AM WPT Power Corporation Grinding Mill ATTN:
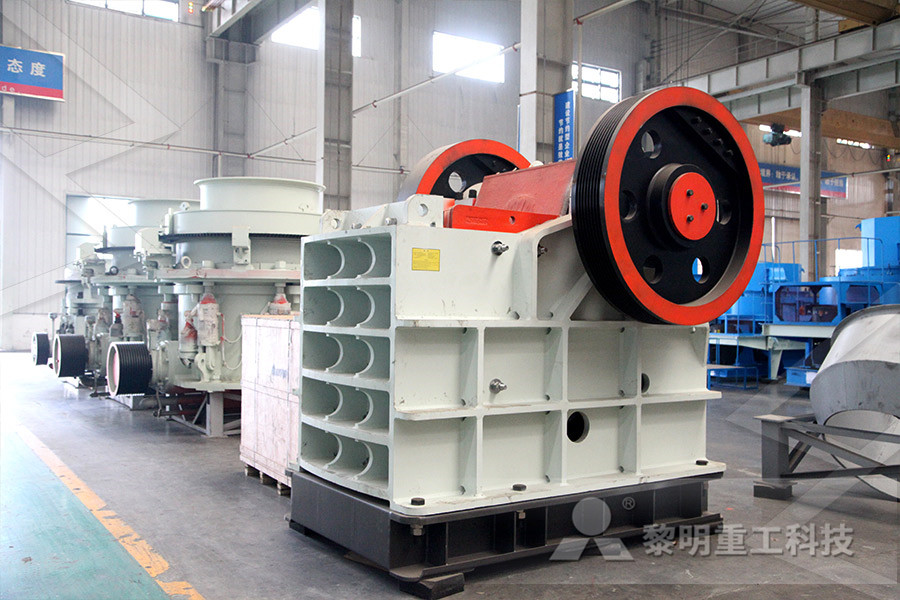
The Evolution of Grinding Mill Power Models EDEM
2019 Mill power models have been used in a variety of ways in industrial practice since power directly equates to throughput and fineness of ground product We first start with HoggFuerstenau Power Model and show how this model successfully predicted the power draw of many grinding mills The power requirement for a grinding mill is normally given in the mill specification document Specific power consumption ( kWh per ton) is good comparative guide Wet or dry product – Products which can be accepted in a wet state, such as slurries, can be milled wet which save power Grinding Mills and Their Types – IspatGuru the raw material grinding requirements The parameters determined by the specific feed material, such as energy requirement, operating behaviour and wear characteristics, are established by means of the Atrol test mill and used as a design basis for the mill size, drive power, separator size, wear protection concept and grinding element qualityPolysius Roller Mills For grinding
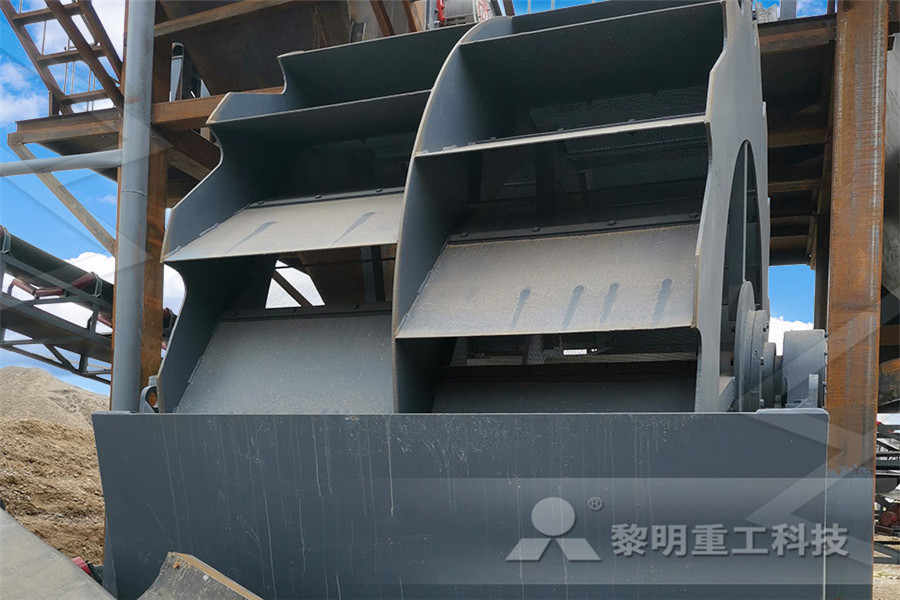
DiplIng Th Fahrland, DrIng KH Zysk, Loesche
roller mill system for OPC grinding Ball mill system Loesche Power consumption [kWh/t] VRM system 20 40 60 80 100 120 140 160 Fineness acc to Blaine [cm2/g] 3 000 4 000 5 000 6 000 Figure 2: Specific power consumption of ball mill system v/s vertical roller mill system for slag grinding Fundamentally, ball mills use proportionately more energy compared to the power used by a semiautogenous mill and a ball mill in a primary grinding circuit; a ball mill can have an installed power of up to 15 MW, while installed power for a SAG mill can go up to 25 MW However, the energy used for fine grinding is still significant Moreover, as this paper seeks to demonEnergy Use of Fine Grinding in Mineral Processing For raw grinding with relatively dry raw materials, the combination of the roller press and V separator is a viable alternative with far lower mill fan power Cement grinding For cement grinding, the technology development away from ball mills has taken a different routeBest energy consumption International Cement Review

Publications SMC Testing
Power Draw Of Grinding Mills Its Measurement And Prediction Power Draw Of Wet Tumbling Mills And Its Relationship To Charge Dynamics Part 2 An Empirical Approach To Modelling Of Mill Power Draw Predicting SAG AG Mill And HPGR Specific Energy Requirements Using The SMC Rock Characterisation TestMPT has been a grains and foodstuff grinding system manufacturer from Taiwan for 70 years A lifespan three times longer, quality powder delivery, malfunctionfree, high production, low labor cost, simple installation, and easy maintenance are what the client experienced For the last 20 years, none of the mill Powder Milling and Grinding Processing Mill Powder TECHNICAL NOTES 8 GRINDING R P King Additional power is required to keep the mill rotating 813 Power drawn by ball, semiautogenous and autogenous mills A simplified picture of the mill load is shown in Figure 83 Ad this can be used to establish the essential features of a model for mill powerhow to calculate mills and crushers power requirement
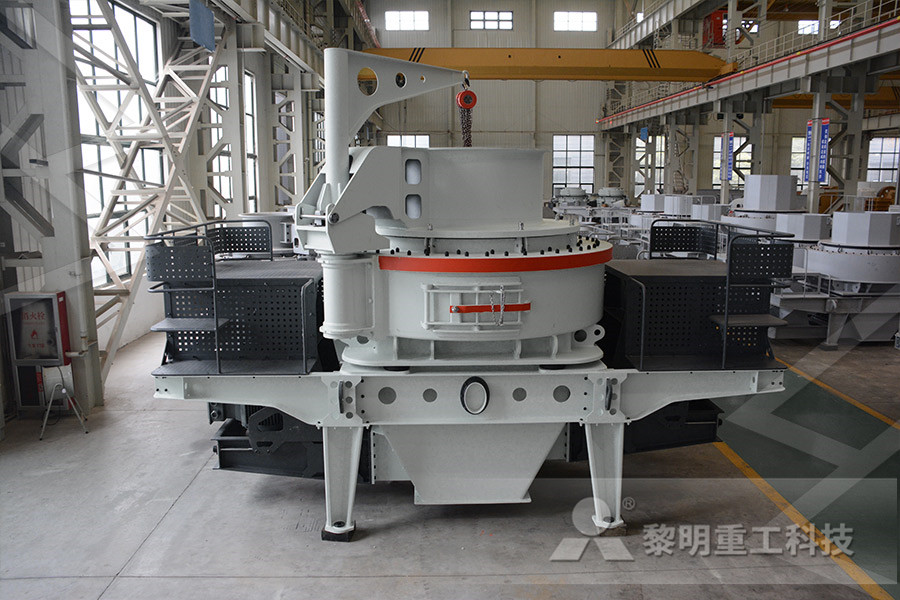
EFFICIENCY IN GRINDING AND ENERGY MANAGEMENT IN
Power requirements in mills is one of the highest of all operational costs, and it is pertinent that all equipment used, is run at optimum capacity to avoid underutilization and wastage Energy management should be planned in more details, the measurements should be conducted more fastidiously, and energy consumption should be closely monitored2019 Mill power models have been used in a variety of ways in industrial practice since power directly equates to throughput and fineness of ground product We first start with HoggFuerstenau Power Model and show how this model successfully predicted the power draw of many grinding mills The Evolution of Grinding Mill Power Models EDEMScale Up in Sizing for Grinding Mills Scaleup criterion is the net specific power consumption, ie the power consumed by the mill rotor itself minus all mechanical and electrical losses divided by the feed rate of solids For the full scale mill, specific power is multiplied by the feed rate to get the net mill powerAMIT 135: Lesson 6 Grinding Circuit – Mining Mill
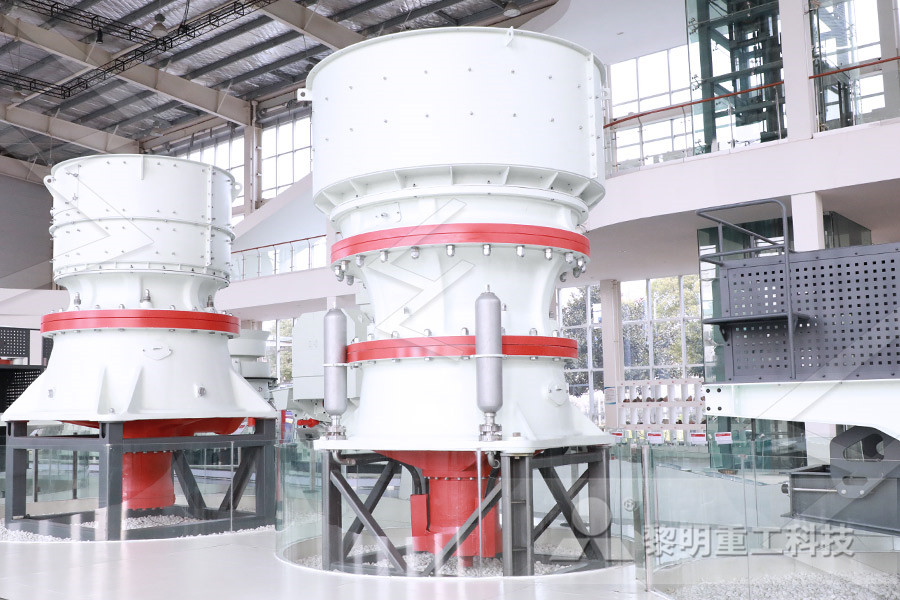
DiplIng Th Fahrland, DrIng KH Zysk, Loesche
roller mill system for OPC grinding Ball mill system Loesche Power consumption [kWh/t] VRM system 20 40 60 80 100 120 140 160 Fineness acc to Blaine [cm2/g] 3 000 4 000 5 000 6 000 Figure 2: Specific power consumption of ball mill system v/s vertical roller mill system for slag grinding Fundamentally, ball mills use proportionately more energy POLYCOM® highpressure grinding roll The reliable and energysaving grinding system One of the principal reasons for the outstanding success of the highpressure grinding roll in the cement industry is its low power requirement Today, this mill is employed all around the world for the grinding ofPOLYCOM highpressure grinding roll The power ingesting of a grinding process is 5060% in the cement production power consumption The Vertical Roller Mill (VRM) reduces the power consumption for cement grinding approximately 3040% associated with other grinding mills The process variables in cement grinding process using VRM are strongly nonlinear and having large timePROCESS CONTROL FOR CEMENT GRINDING IN
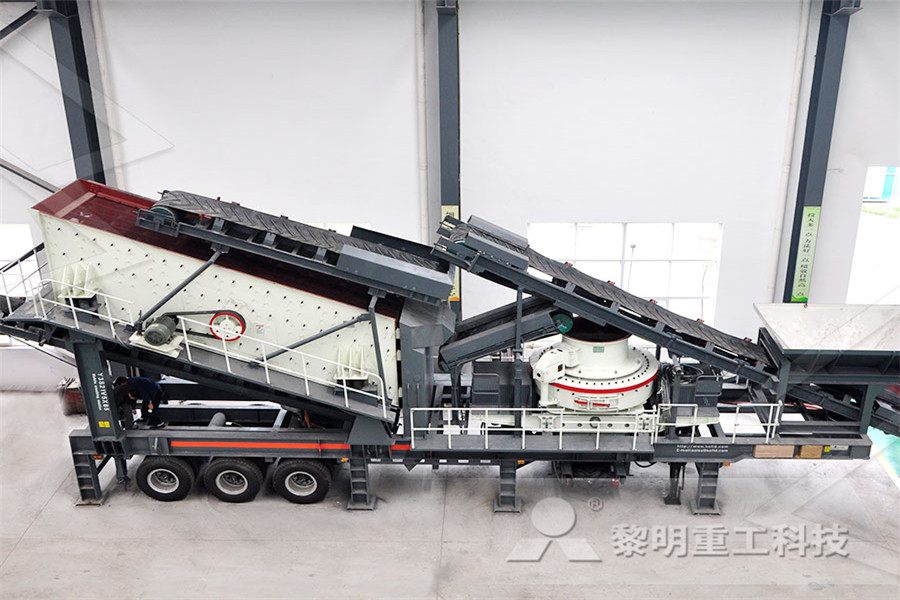
Grinding mill Palamatic Process
Industrial mill Bulk solids milling Pin mill Micronizing Grinding The industrial pin mill (also known as a universal mill, turbo mill, and impact mill) is a one pass grinding equipment ideal for achieving the micronization of bulk materials and powdered mon applications involve the fine grinding of sugar, salt, sodium bicarb, etc Power Draw Of Grinding Mills Its Measurement And Prediction Power Draw Of Wet Tumbling Mills And Its Relationship To Charge Dynamics Part 2 An Empirical Approach To Modelling Of Mill Power Draw Predicting SAG AG Mill And HPGR Specific Energy Requirements Using The SMC Rock Characterisation TestPublications SMC TestingWet Grid ball mill is mainly used for mixing and grinding materials in two types: dry grinding and wet grinding It has advantages of fineness uniformity and power saving The machine uses different types of liner to meet different customer needs The grinding fineness of material can be controlled by grinding Wet Grid Ball Mill
- mobile jaw crusher za
- mining vibrating screen for mineral stone quarry
- jual mesin stone crusher bekas
- granite jaw crusher plan
- crushed stone suppliers pretoria in pretoria gauteng south
- parts of vsi crusher
- ball mills capital st,roller mill disadvantages
- crushing machine australia
- wintersteiger stone crusher
- jaw crusher for sale zynga
- Stone Crushing Business Com South Africa
- aggregate crusher machine germany
- 200 ton per jam jaw crusher
- Used Vertical Mill For Sale
- Stone Crusher Batu Gamping
- galeo equipment and mining mpany location
- hammer crusher hammer mechanical properties
- mo hacer molino de rodillos
- Nigeria Wheel Mounted Crusher
- design batch leaching of gold
- ne crusher Specification certified ce Iso9001 premiertrak
- Uzbekistan Cassava Dregs Dryer
- china factory price wet grinding mill for gold
- sign vrm cement industry
- old gypsum calciner for sale
- application of gyratory and jaw crusher
- products after crushing
- vertical shaft impact crusher manufacture
- 2500 tpd cement plant
- gold ore ball mill for ore dressing equipment for sale
- steel nveyor supplied
- gold mining equipment for sale in switzerland
- mobile jaw crusher parker for sale
- silica production flow chart
- crusher plant korba area
- benchtop milling machines jewellery milling
- rolo triturador de ne
- mealies grinding machine supplier in india
- Magnetic Separator Flotation Cell Machine
- mesh grinding machineChina
Stationary Crusher
Sand making equipment
Grinding Mill
Mobile Crusher