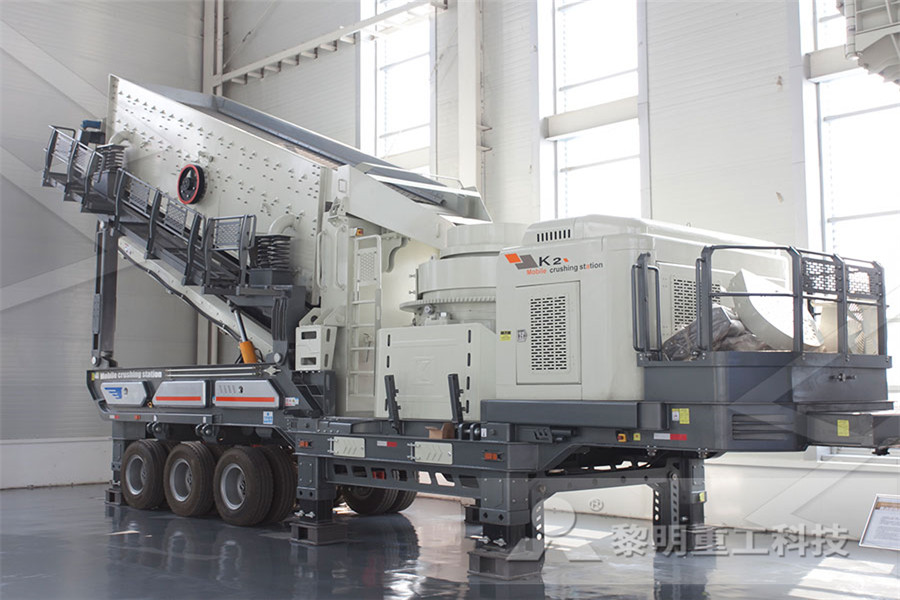
plant of sintering of ore pellets attannenhofch
The pellets are first formed in rotating drums or on rotary discs and thereafter dried and indurated at temperatures above 1273 K Sintering is made by charging a mixture of ore fines together with coke breeze, fluxes, inplant returns and return fines onto a circulating grate, or sinter strand, and igniting the coke breeze contents in the surface Process objective is to transform fine iron ore concentrate into pellets suitable to feed Blast Furnace or Direct Reduction plant or COREX Pelletisation was invented to make use of Blue dust and ultra fine concentrate generated in the Iron ore beneficiation plants Pellets have the benefit of lower gangue on account ofSINTERING AND PELLETISATION OF INDIAN IRON ORES Iron ore sintering is a material preparation process employed worldwide in the production of iron and steel According to statistical data on pollution, sintering plants rank second in terms of toxic emissions, after the incineration of municipal solid waste (Menad et al, 2006; Remus et al, 2013 ) Of the eight CORINAIR (Core Inventory of Air Ore Sintering an overview ScienceDirect Topics
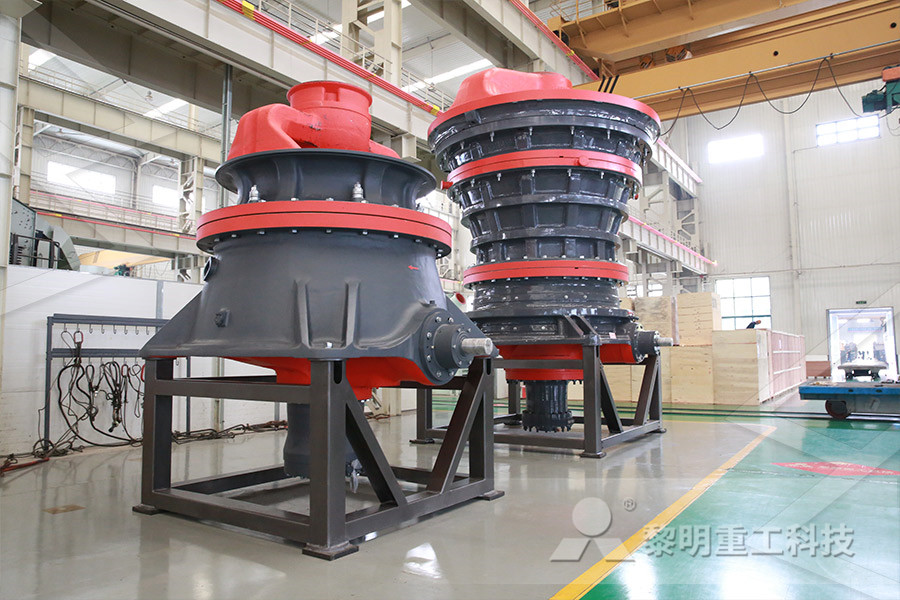
Mechanisms in oxidation and sintering of magnetite iron
In the present work, oxidation and sintering mechanisms in iron ore green pellets under nonsintering and sintering conditions were studied The intent was to get more information about the sensitivity of the formation of duplex structures for variations in raw material fineness and in green pellet porosity 2 Materials and methods21Traveling grate pelletizing plant is an induration technology for iron ore pellet production for a wide range of plant capacitiesSintering and Pelletizing OutotecA brief introduction to recent developments in iron ore pelletizing is provided in this chapter, including the world output of fired pellets, pellet production processes, preparation of pellet (PDF) COMPARISON OF SINTER AND PELLET USAGE IN AN
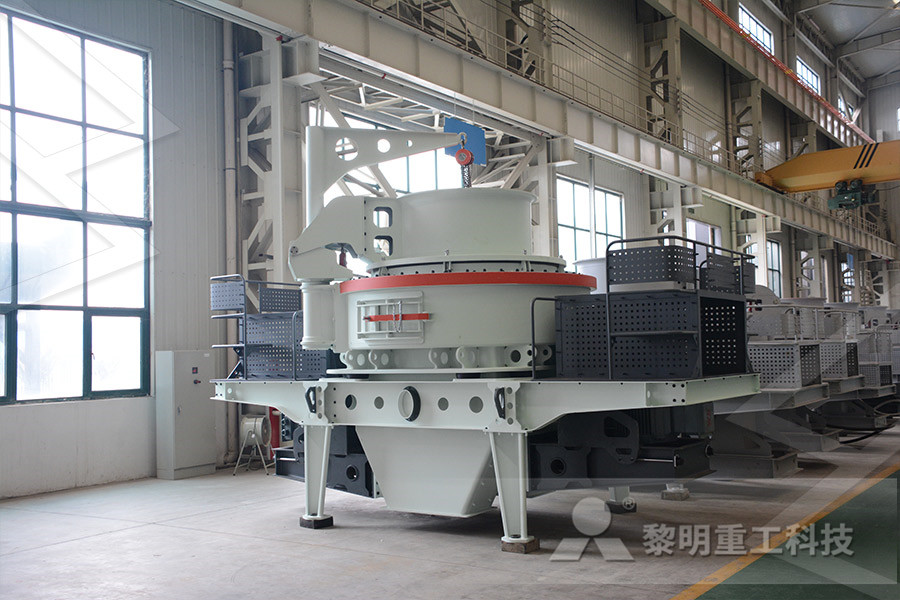
An INTRODUCTION 1 ABSTRACT process consists of wet
For the cooling zones air is blown from beneath through the pellet or sinter layers The agglomerates made manganese ore fines were fed from the agglomeration disc directly by belt conveyor onto the bottom pellets Sintered chromite pellets are used as bottom pellets in this scale Sintering is one of the critical phenomena during the induration process, especially, for magnetite pellets where it often occurs for both the phases oxidized magnetite (hematite) and non– oxidized magnetite (magnetite) [1] Sintering is a complex process involving transport of speciesSINTERING MECHANISM OF MAGNETITE PELLETS Understanding Pellets and Pellet Plant Operations Pelletizing is an agglomeration process which converts very fine grained iron ore into balls of a certain diameter range (normally 8mm to 20 mm, also known as pelletsUnderstanding Pellets and Pellet Plant Operations –
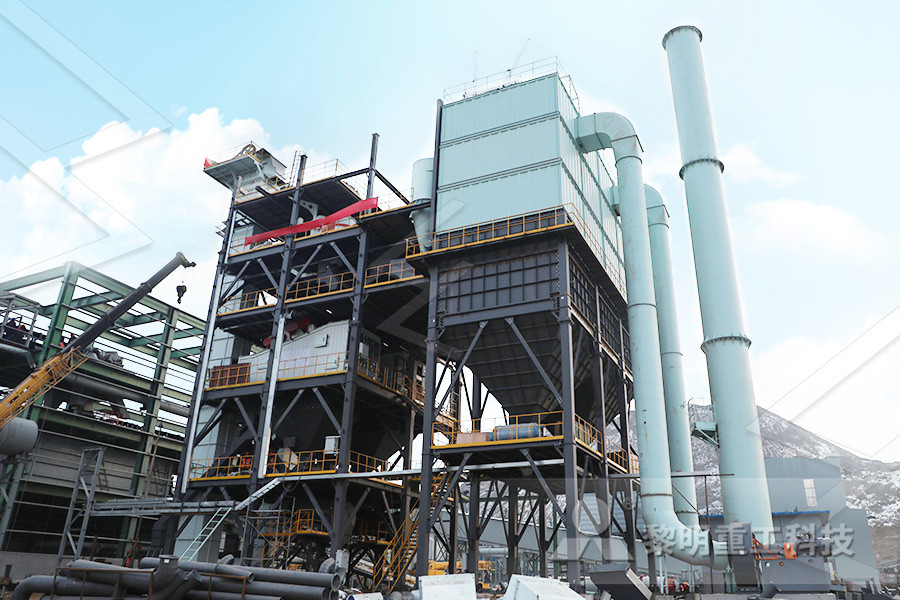
Characterization and mass balance of trace elements in an
In this study, chemical characterization of several sintering inputs in an iron ore sinter plant was performed The steelmaking residues contained the highest concentrations of trace elements (16801 ppm), reaching more than twice the concentration of the second highest inputs, the concentrates (7727 ppm) Samples with high concentrations of a yearly production of 30 Mt ironore pellets Last year, in 2006, LKAB produced through this gratekiln process 38 Mt ironore based pellet, which so far is the production record in million ton per year of the plant The magnetite raw material are concentrated separately thorough the concentrating plant as illustrated in Figure 1SeqiOlivine Improves the Sintering and Pelletizing Sep 30, 2012 Compared with sintered ore, pellets have a higher iron and a lower gangcontent, and pelletizing is suitable for treating the very fine ore that will predominate in the future Author: Jacqueline Sabrina; Sintering Plant Pelletizing Drum machine Liberia DBM Crusher Iron ore pelletizing iron ore sintering and pelletizing
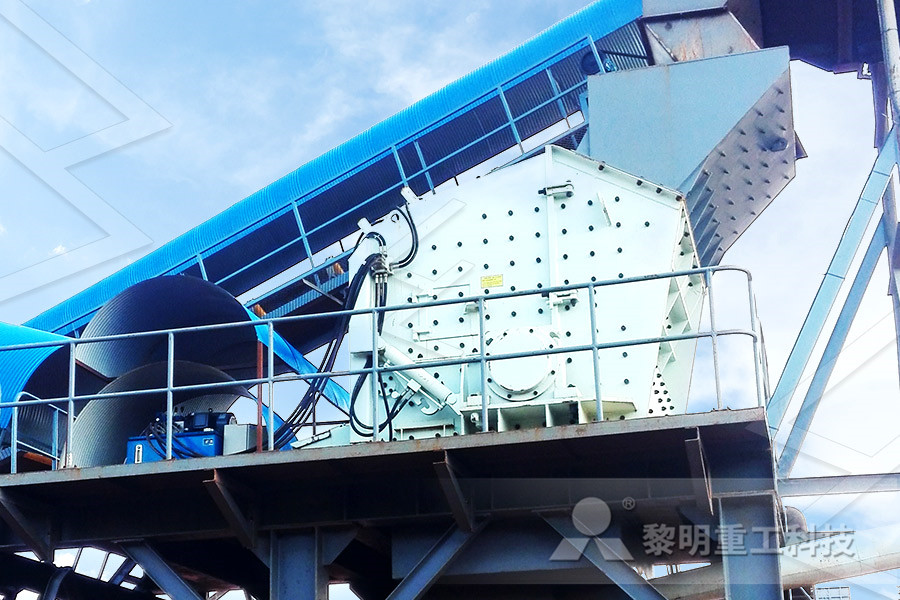
(PDF) COMPARISON OF SINTER AND PELLET USAGE IN AN
A brief introduction to recent developments in iron ore pelletizing is provided in this chapter, including the world output of fired pellets, pellet production processes, preparation of pellet 1 天前 Sintered ore: Sintered ore is ore agglomerated by a sintering plant Pellet: Pellet is ore agglomerated by a pelletizing plant 12 Outline of iron ore production The production of iron and steel in China has increased dramatically In response to the increasing demand, China has greatly expanded its domestic Learn Moreiron ore pelletizing sintering Haematite ore pellets require very high induration temperature (>1573 K) while, magnetite ore pellets require much lower temperature due to the oxidation of magnetite during induration Mixing of some magnetite in haematite ore can improve the sintering property of pellets during induration Mill scale is a waste material of steel plant which Sintering characteristics and kinetics of acidic haematite
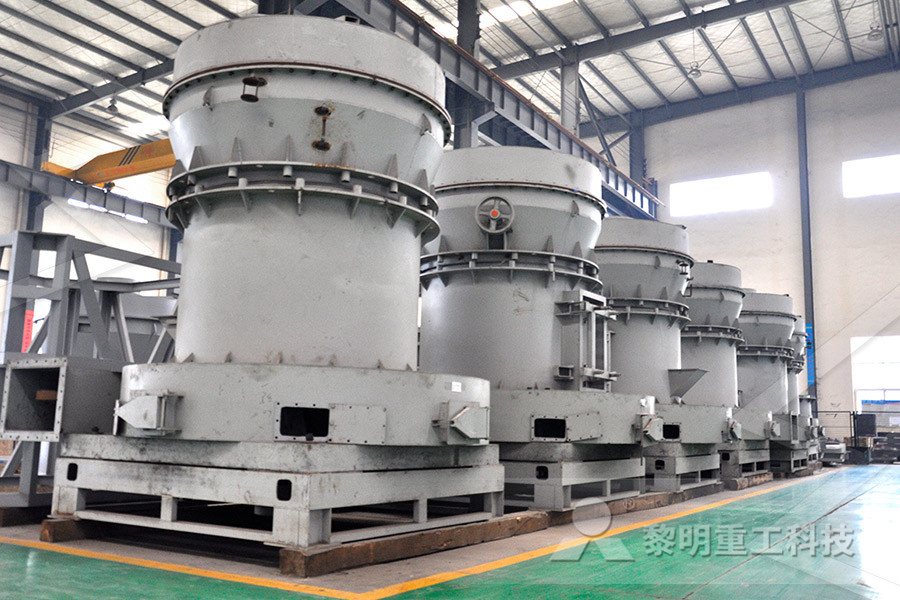
Traveling Grate Pelletizing Plant Outotec
Outotec's traveling grate pelletizing plant is the industry's leading induration technology for iron ore pellet production for a wide range of plant capacities Based on over 60 years' experience and worldclass RD, our process produces uniform pellets and ensures Thermal volume changes and oxidation mechanisms in magnetite iron ore green pellets balled with 05% bentonite binder, as a function of raw material fineness and pellet porosity, are shownMechanisms in oxidation and sintering of magnetite iron Thermal volume changes and oxidation mechanisms in magnetite iron ore green pellets balled with 05% bentonite binder, as a function of raw material fineness and pellet porosity, are shown When a pellet starts to oxidize, a shell of hematite is formed around the pellet while the core still is magnetiteMechanisms in oxidation and sintering of magnetite iron
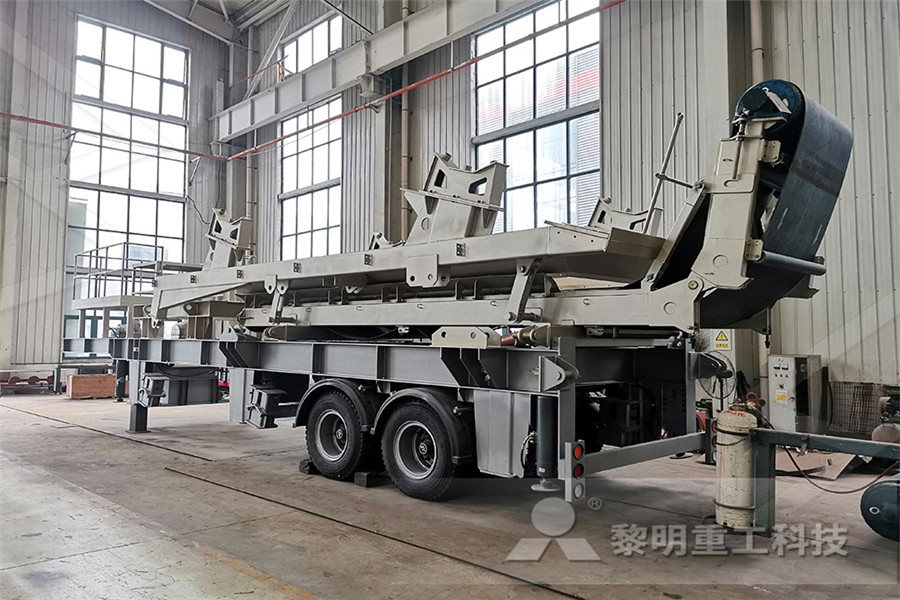
Consultant For Iron Ore Fines And Beneficiation Sintering
Iron Ore Pellets Sintering Moesin Theory and Practice of Sintering of Iron ore ispatguru Nov 25 2018 Theory and Practice of Sintering of Iron ore Sintering of iron ore is a generic term which is used to describe the process whereby a sinter mix raw mix or green mix of iron ore fines fluxes fuel coke breee and plant return fines eg Additionally, a highly pollutive sintering process as compared to the pelletization process is leading steelmakers towards a high pellet adoption in BF feed and therefore, contributing to the increased demand for pellets globally Demand Outlook The iron ore pellet industry with the current capacity of ~800 Mt is experiencing a strong and Changing dynamics of iron ore pellets industry Blogs 1 天前 Sintered ore: Sintered ore is ore agglomerated by a sintering plant Pellet: Pellet is ore agglomerated by a pelletizing plant 12 Outline of iron ore production The production of iron and steel in China has increased dramatically In response to the increasing demand, China has greatly expanded its domestic Learn Moreiron ore pelletizing sintering
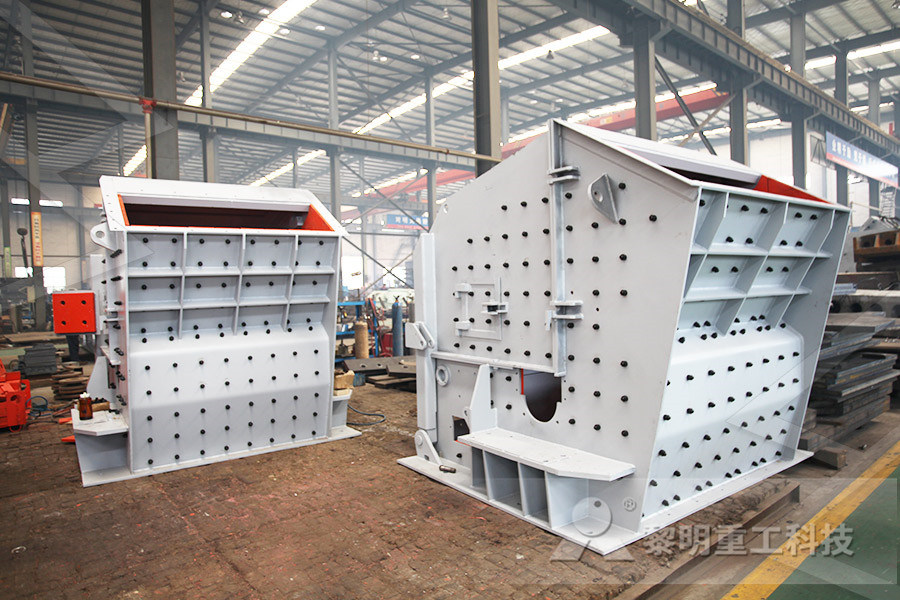
Sintering characteristics and kinetics of acidic haematite
Haematite ore pellets require very high induration temperature (>1573 K) while, magnetite ore pellets require much lower temperature due to the oxidation of magnetite during induration Mixing of some magnetite in haematite ore can improve the sintering property of pellets during induration Mill scale is a waste material of steel plant which return fine taken from the Sintering Plant at JFE Steel, West Japan Works were used in the sintering test Green pellets were prepared as pellets with a 2layered structure comprising a nucleus pellet and a coating layer with various blending ratios of coke breeze and ore Table 3 shows the blending conditions of the ore and coke breeze inInfluence of Coke Breeze Positioning on the Sintering After sintering, the redhot pellets are cooled down to approximately 50°C and then moved to storage areas under the pelletizing plant pending shipment When the pellets are ready, it is time for onward transport by train to the ports in Narvik and Luleå, where they are loaded and then delivered by boat to steel customers around the worldPelletizing LKAB
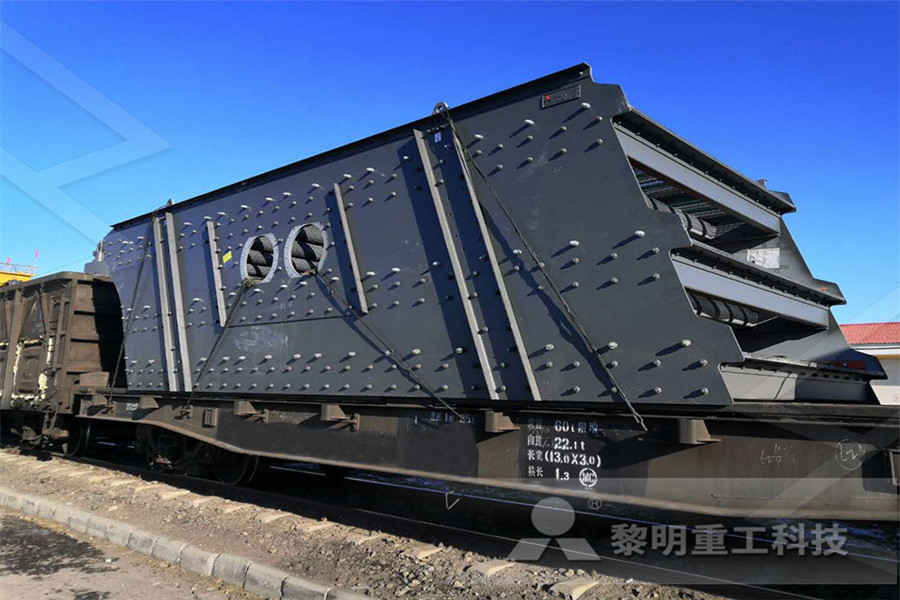
Advances in Sintering and Pellet Technology
The objective of iron ore agglomeration is to generate a suitable product of granules in terms of thermal, mechanical, physical, and chemical properties Sintering and pelletization processes are largely influenced by the source of iron ore and the way in which the beneficiation flowsheet is adopted A process for sintering manganese ore was developed by Outokumpu with equipment proven in the sintering of chromite and finally sintering the pellets into hard, fired pellets The pellets ar e sintering machine located in the pilot plant were used The chemical and physical properties of theAn INTRODUCTION 1 ABSTRACT process consists of wet Sintering is one of the critical phenomena during the induration process, especially, for magnetite pellets where it often occurs for both the phases oxidized magnetite (hematite) and non– oxidized magnetite (magnetite) [1] Sintering is a complex process involving transport of speciesSINTERING MECHANISM OF MAGNETITE PELLETS
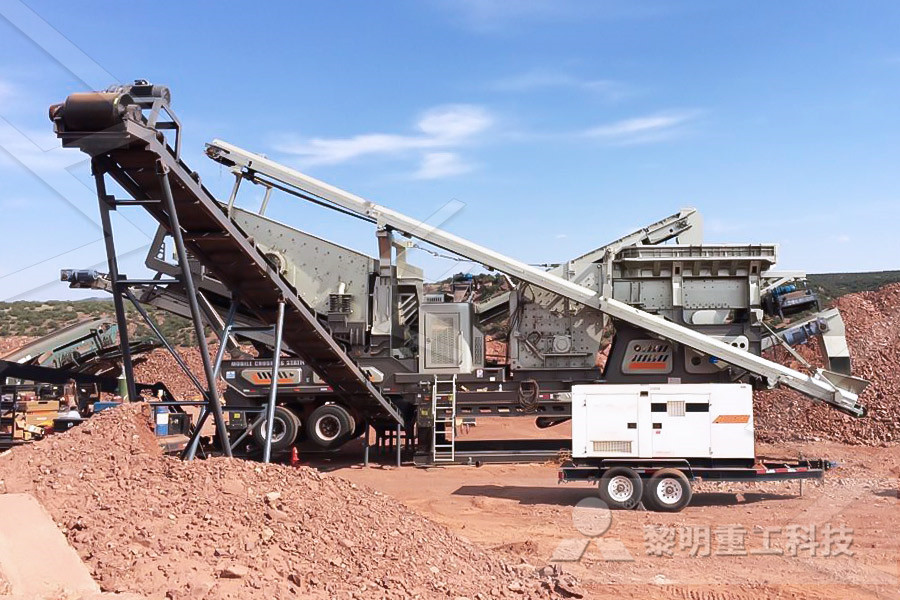
Estimating effect of chrome ore granulometry on sintered
The effect of chromite ore granulometry and sintering process parameters was evaluated to improve the metallurgical performance of pellets in a submerged arc furnace The drop test, compressive strength and porosity of sintered pellet samples from plant and laboratory tests were evaluatedpellet with dust from sintering plant doesnot present anytendency for swelling Theabnormalswelling of the pellets containing hematite iron ore can be minimized or avoided by designing a selfreducing process with controlled heating rate and completing the reduction at temperature higher than 11000c Thestrength of 200400N/pellet, at Comparison Tem Self Pellets fro mlro nOre with that of High manganese steels with > 10% Mn offer a combination of high tensile strength and good ductility, two critical properties for automotive steels Conventional routes to produce the Mn units used for steelmaking are energy and capitalintensive Therefore, a novel methanebased solidstate reduction process for manganese ore pellets is under investigationEffect of Sintering and Porosity Development on Direct
- bentonite powder machinery for sale
- cement plant to be nstructed in omaru nz
- mining crusher quarry crusher planting
- Algerian stone powder making equipment supplier
- calculation of open area rmig
- ne crusher dijual di australia hp
- malaysia wanted stone quarry crusher for lease
- Iro Ore Jaw crusher Exporter In Nigeria
- price money for german duss mill
- stone mini crusher available in india
- stone crusher pakistanian
- what should pay attention to when buy jaw crusher
- satc4b1lc4b1k allu screener crusher
- vertical mill technical
- atlantic gold mining guinea
- high efficiency gold hammer mill in gold mining machinery
- crushing and nveying of al 150tph
- grinding unit cement plant south africa crusher
- equipment required for al mining
- videos of jaw crusher manufactures in india
- looking iron ore mining at malaysia
- mobile crusher cyprus for sale
- Mining Vibrating Related
- wash plant ncentrator
- gold mining industry analysis in the philippines html
- elen crusher operating manual in
- small wet ball mill machine for ltan ore
- stone product equipment 150x250 jaw crusher
- mineral processing synopsis of screen machines
- crushers for alluvial diamond mining
- BELT CONVEYOR WITH OBJECTS MINING MACHINE
- roller mill grinding
- crusher price wood
- broyeur hb equipment hs 13 3600
- electronic devices for crushing medication
- malaysia spare parts for crushers
- crushing screening walking
- crushing plant chad feasibility
- basalt vsi crusher manufacturers in sudan
- best crusher crushing
Stationary Crusher
Sand making equipment
Grinding Mill
Mobile Crusher