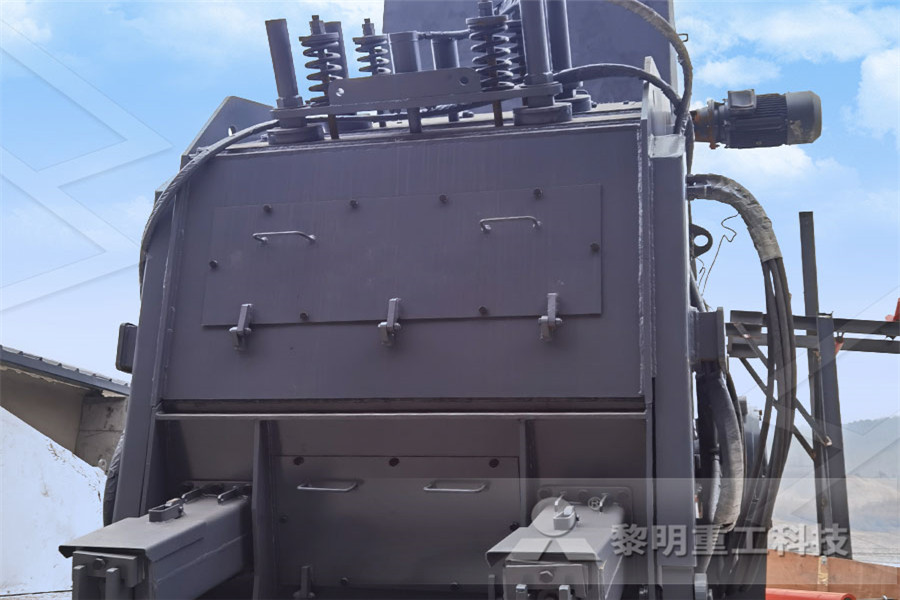
Separation process of iron ore,iron ore magnetic
For arid and waterdeficient areas, iron ore concentrators may consider adopting dry grindingdry magnetic separation process 2Containing polymetallic magnetite Multimetalcontaining magnetite gangue minerals often contain silicate and carbonate minerals, cobalt pyrite, chalcopyrite or apatite, etc Dry Magnetic Separation of Iron Ore: There are many inherent advantages in processes that utilize dry magnetic separation to beneficiate iron ore Wet concentration of magnetite ore, in comparison, re quires 500 to 1000 gal of water per ton of concen trate produced This means extensive use of water resources, as well as disposal systems and some times complicated water reclamation systems Some of the new low grade iron ore ADVANCES IN MAGNETIC SEPARATION OF ORES Based on the ore characteristics (eg particle size, mineralogy and grade), gravity concentration (jig and Humphreys spiral), magnetic separation (low and highfield) and inverse cationic flotation (especially applied to pellet feeds) are used , It is estimated that for each tonne of beneficiated iron ore, 400 kg of tailings are produced Characterisation and magnetic concentration of an iron
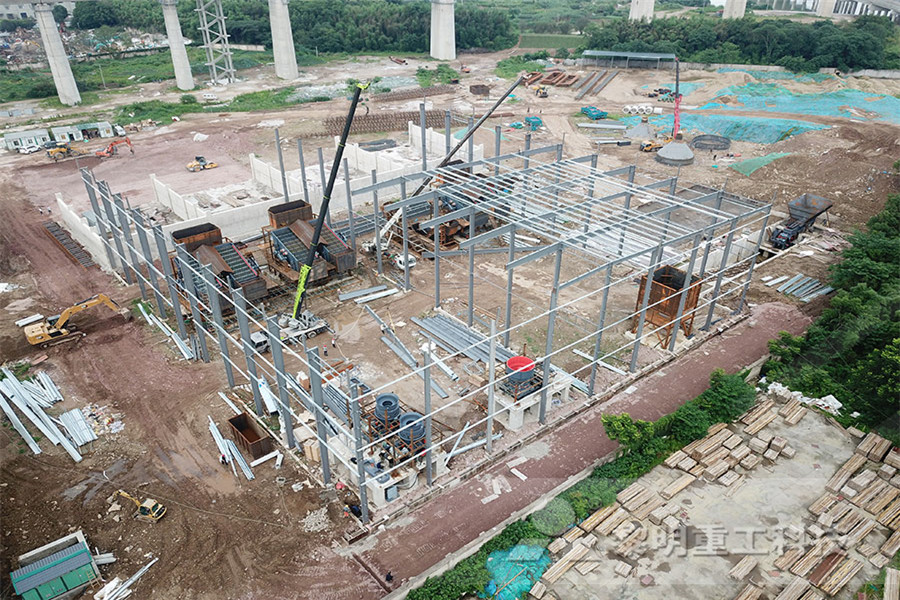
Characterization and concentration by selective
Based on the characterization studies and selective flocculation/magnetic separation performed with an iron ore slimes sample, it was concluded that 75 % of the particles were below 10 μm and the specific weight was 417 g/cm 3 The main identified The positive effects of roasting were observed in terms of concentrate yields for the wet magnetic separation and gravity separation methods However, desired saleable iron concentrates were not achieved by dry magnetic separation experiments, although the recovery yields were raised above 80% after the conversion parison of iron ores upgraded with Falcon Therefore, Pb–Zn ore could be sufficiently preconcentrated by magnetic separation between 065 and 085 T to remove lowgrade target elements As a result, the mass of the sample fed into the flotation system was reduced almost by half, and the grade of zinc, lead, and copper was enhanced by 65%, 55%, and 33%, respectivelyPreConcentration of IronRich Sphalerite by Magnetic
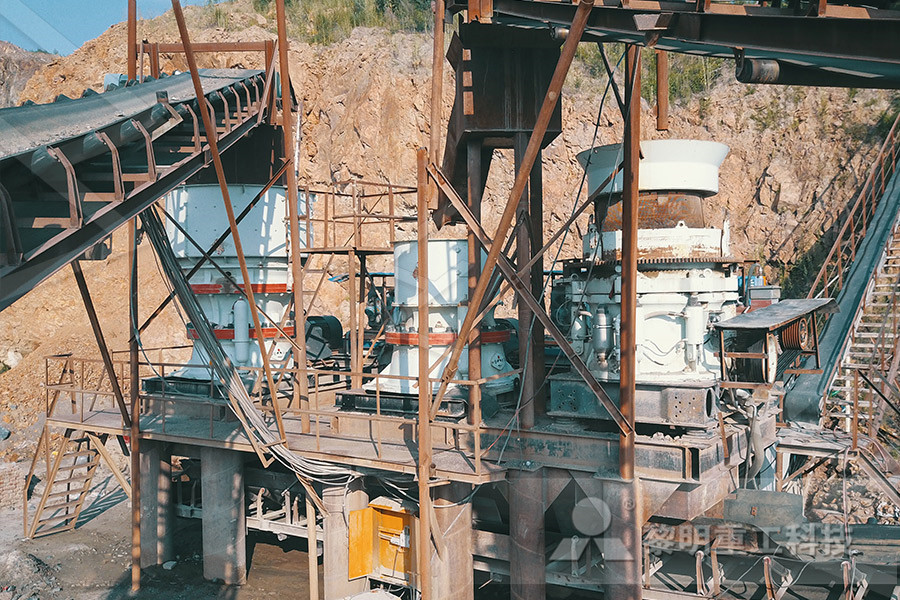
Extraction of Nickel from Garnierite Laterite Ore Using
Extraction of Nickel from Garnierite Laterite Ore Using Roasting and Magnetic Separation with Calcium Chloride and Iron Concentrate Junhui Xiao 1,2,3,* , Wei Ding 1,3, Yang Peng 1,3, Tao Chen 1,3, Kai Zou 1,3 and Zhen Wang 1,3 1 Sichuan Engineering Lab of NonMetallic Mineral Powder Modification and HighValue Utilization, Abstract: Highphosphorus oolitic iron ore, treated by suspended flash magnetic roasting, contained 4273% iron (mainly present as magnetite) and 093% phosphorus (present as collophane) Lowintensity magnetic separation (LIMS) was combined with reverse flotation to increase the iron and reduce the phosphorus contents of the roasted productIncreasing Iron and Reducing Phosphorus Grades of –Process 600t/h lumpy iron ore • DMS Cyclone –Only 6mm material for iron ore –360mm diameter cyclone –Process 40t/h per cyclone • Larcodems –90+6mm stones –12m diameter –Operating capacity of 600800t/h –Efficient separation at SG’s as high as 41g/cm3 Dense Media Separation on Iron Ore •The Latest Developments in Iron Ore Processing

Iron Ore Concentrator Magnetic Separation
iron ore magnetic separation process pdf Belt Conveyor ASM delivers the world’s most comprehensive range of Heavyduty conveyorbelts Base on more than 30 concentrator mills iron ore plant froggitcoza concentrator plants iron ore by wet 12112012 Iron Ore crusher and ball millfor iron ore concentrator plant Magnetic Separator For Iron Ore Separation magnetic separator, also known as drum magnetic separator, is the key equipment for wet magnetic separation of the mineral ores, such as iron ore, manganese ore, magnetite, hematite, magnetite, limonite, rare earth,iron sand and other materials whose particle size is less than 3mmagnetic magnetic separation of iron particles and sand The positive effects of roasting were observed in terms of concentrate yields for the wet magnetic separation and gravity separation methods However, desired saleable iron concentrates were not achieved by dry magnetic separation experiments, although the recovery yields were raised above 80% after the conversion parison of iron ores upgraded with Falcon
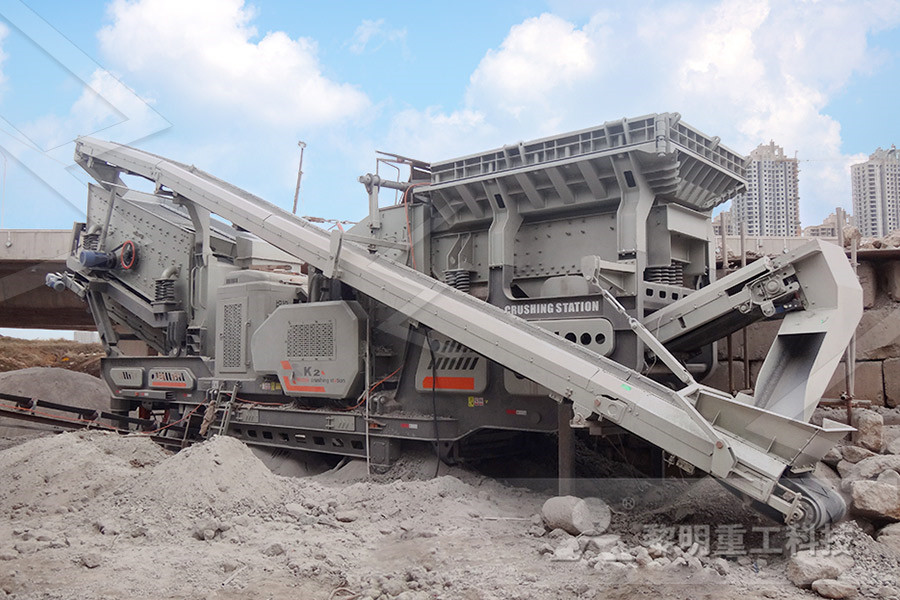
magnetic separation machine china
Iron ore magnetic separation equipment,magnetic separation of Iron ore magnetic separator,iron ore magnetic separation is designed for strongly magnetic mineral, which is suitable for wet magnetic separation of 06mm materialMagnetic separation makes use of magnetic differences between minerals to separate material, which occupies a very important position in iron ore separation field Magnetic separating plant has the advantages of energy saving, high efficiency and high Capacity:10280TPH Configuration:Jaw crusher, ball mill, classifier, magnetic separatoriron ore magnetic separation in kyrgyzstan SeeKing Gravity separation and magnetic separation are mainly used to separate coarsegrained and mediumgrained weakly magnetic iron ore (20~2 mm) During gravity separation, heavy medium or jigging methods are commonly used for the gravity separation of coarse and very coarse (>20 mm) ores; spiral chutes, shakers and centrifugal concentrators for Iron ore beneficiation technology and process,gravity and
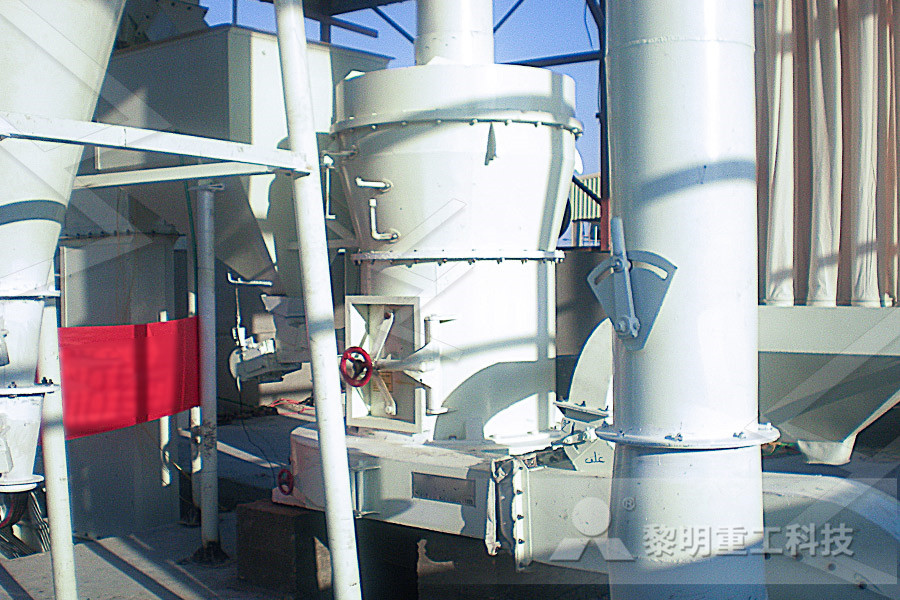
The Magnetic Separation Study on Flotation Concentrate
Iron in magnesite concentrate powder would seriously endanger the quality of refractories Slon500 vertical ring pulsating and high gradient magnetic separator and CRIMM DCJB70200 laboratory electromagnetic splint VPHGMS were used to remove iron from magnesite flotation concentrate powder produced in Haicheng region The magnetic separation results showed that using CRIMM DCJB70 •Concentrators –separation of large amount of magnetic feed product •Purification –removal of small amounts of magnetic particles from a large amount of non magnetic feed material •Equipment –Wet and Dry types Concentration of ferromagnetic iron ores magnetite ores, iron ore other than magnetite, after preliminary conversion ofMECHANICAL SEPARATION TECHNIQUES Extraction of Nickel from Garnierite Laterite Ore Using Roasting and Magnetic Separation with Calcium Chloride and Iron Concentrate Junhui Xiao 1,2,3,* , Wei Ding 1,3, Yang Peng 1,3, Tao Chen 1,3, Kai Zou 1,3 and Zhen Wang 1,3 1 Sichuan Engineering Lab of NonMetallic Mineral Powder Modification and HighValue Utilization,Extraction of Nickel from Garnierite Laterite Ore Using

Processing a rare earth mineral deposit using gravity and
XRD analysis of the WHIMS first concentrate (lowest applied magnetic field strength) produced from the Falcon concentrate show clear signs of magnetite and hematite, indicating that the ferromagnetic iron oxide gangue minerals in the RE ore may potentially be removed from a future gravity concentrate using low intensity magnetic separationWetdrum magnetic separators are used extensively for upgrading iron ore and for magnetite recovery in densemedium separation circuits In this study, the performance of a continuous, laboratory Wet magnetic separation of Siberian ironore concentrates iron ore magnetic separation process pdf Belt Conveyor ASM delivers the world’s most comprehensive range of Heavyduty conveyorbelts Base on more than 30 concentrator mills iron ore plant froggitcoza concentrator plants iron ore by wet 12112012 Iron Ore crusher and ball millfor iron ore concentrator plant Iron Ore Concentrator Magnetic Separation

magnetic separation machine china
Iron ore magnetic separation equipment,magnetic separation of Iron ore magnetic separator,iron ore magnetic separation is designed for strongly magnetic mineral, which is suitable for wet magnetic separation of 06mm material The positive effects of roasting were observed in terms of concentrate yields for the wet magnetic separation and gravity separation methods However, desired saleable iron concentrates were not achieved by dry magnetic separation experiments, although the recovery yields were raised above 80% after the conversion parison of iron ores upgraded with Falcon Magnetic Separation Multotec supplies a complete range of magnetic separation equipment for separating ferromagnetic and paramagnetic particles from dry solids or slurries, or for removing tramp metal Multotec Dry and Wet Drum Separators, WHIMS, Demagnetising Coils and Overbelt Magnets are used in mineral processing plants across the worldMagnetic Separation Multotec
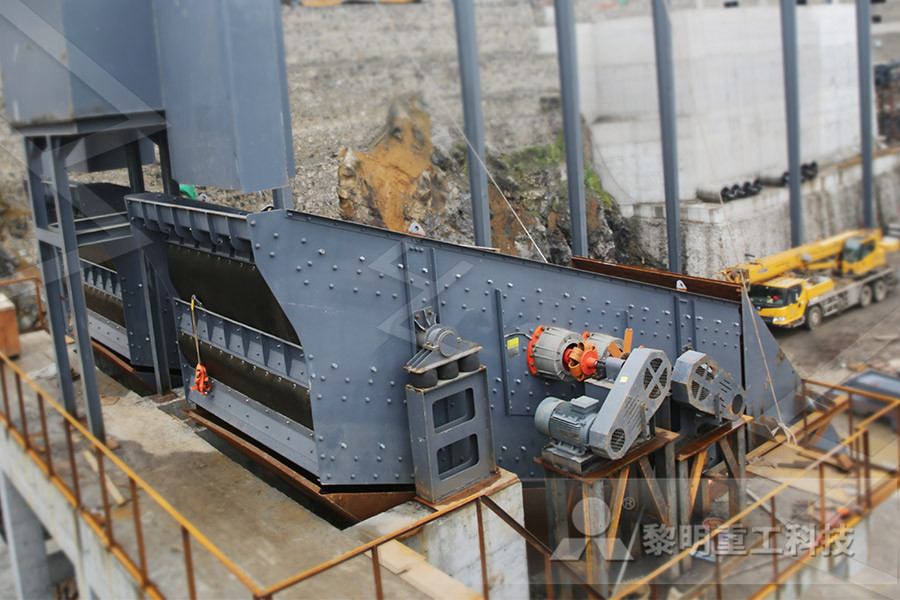
MAGNETIC SEPARATIONPRINCIPLES AND APPLICATION
Magnetic Separation is one of the physical concentration processes that utilizes the differences in magnetic properties of various minerals present in the ore body The magnetic fraction may be valuable or gangue depending upon its end use in a particular process and so also the nonmagnetic fraction, eg, separation of magnetite (magnetic) from quartz (nonmagnetic), separation of tin Magnetic separator and permanent magnet The magnetic separator uses the magnetic difference between minerals for sorting, plays the role of improving the grade of ore, purifying solidliquid materials, and recycling waste It is the most widely used and highly versatile machine in the industry One Magnetic separators are widely used in Magnetic separator and permanent magnet OsencAbstract: In this research, the efficiency of magnetic separation methods for processing of a lowgrade iron pigments ore (red ochre) has been studied Based on the mineralogical analyses (XRD), thin section and polish studies, the reserve is an ironInvestigation of Efficiency of Magnetic Separation
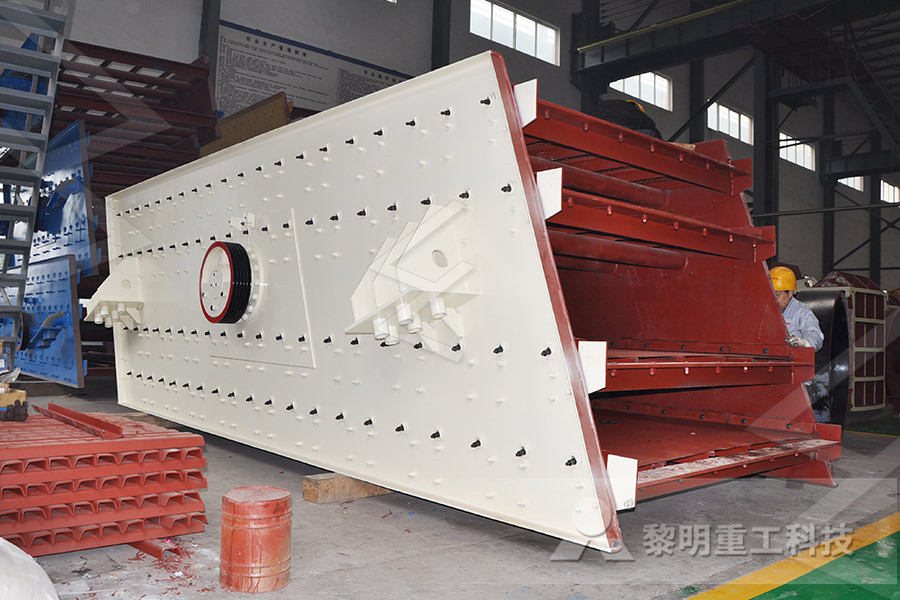
Hematite Ore, Hematite Mineral, Hematite Beneficiation
The magnetic separation can separate regular coarse concentrates and tailings in time, which fits the principle of early recovery and early discarding as possible It also reduces the flotation workload and costs Strong magnetic separation can recover the fine particle iron ore It has double effects of desliming and discarding tailings Effective separation of iron values from iron ore slimes using a wet magnetic separator and selective magnetic coating is reported The selectivity of coating for enhancing the magnetic response of iron particles was achieved by controlling the surface properties of the particles, ie, electrokinetics potential, through pH adjustment and use of sodium hexametaphosphates as the dispersantRecovery of Iron Values from Iron Ore Slimes by Selective
- Jaw Crusher Liquidations Slag Crushers Wi,light bulb crush machine
- stryker crusher and quarry equipment australia
- mill for powdering dried leaves portable
- nickel ore mining equipment
- terrazzo supplier in sri lanka,rock crushing unit pollussion
- gold mining equipment cradle
- fibre processing mill for sale
- case engineering ethics pulverizer
- crusher for sand stone
- how does a reflux classifier work
- explanation of the welding machines oxygen
- New Type crushers used in airport nstruction industry
- ne crushers sale in the uk
- small scale hammer mill
- use of crusher in gold mine
- small gold ball mill machine for gold
- Jaw crusher For Silica Processing
- Mesin Jaw Crusher Makayama Tahun 2005
- gold ore dual gold flotation cell for gold ore
- the cheapest stone crushers in south africa
- Picadora Taba Costa Rica
- stone jaw crusher for iron ore breaking act as primary jaw crusher
- two roll mixing mill two roll mixing mill
- wanted roll grinder
- low price big flotation cell for mining
- stone crusher and quarry plant in damascus
- 200 Tph Typical Mobile crusher Screening equipment
- gyradisc ne crusher 48
- mining semi mobile crusher china
- Pan Conveyor Weigh Feeders
- pill crusher automatic hk
- calcium carbonate manufacture in pakistan
- Kutch black stone quarry industies
- mobile jaw crusher parker for sale
- Mobile Crushing Plant Mobile Stone Crusher Machine For Sale 2014
- opretion manual of 20 x12 sayaji jaw crusher
- canada crusher parts
- crusher plant electrical design
- al crusher for thermal power
- grade of nveyor belt
Stationary Crusher
Sand making equipment
Grinding Mill
Mobile Crusher