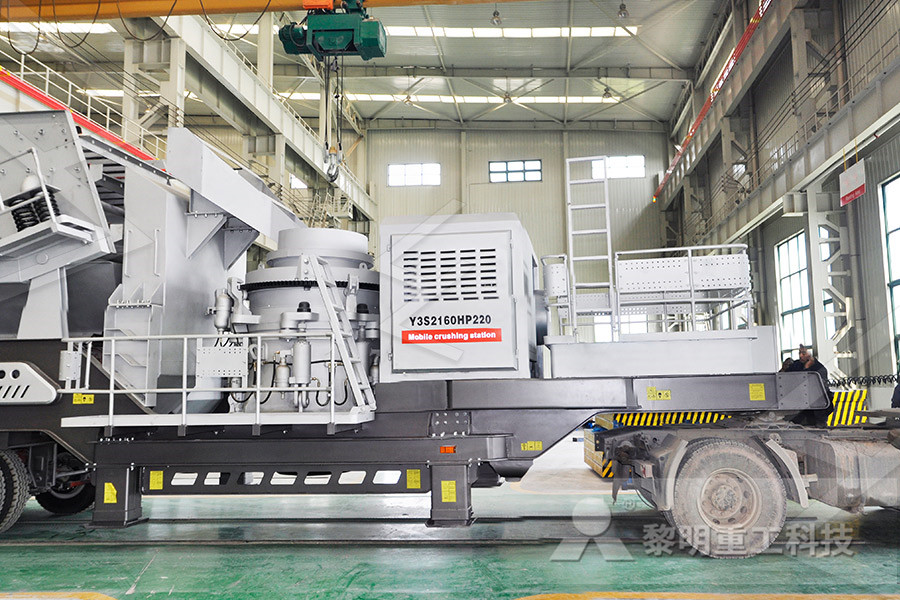
EFFECT OF BALL SIZE DISTRIBUTION ON MILLING
42 Effect of ball diameter on the selection function 55 43 Reduced selection function graph 56 44 Reduced cumulative breakage function 58 51 EQM and OEM ball mass size distributions used 64 52 EQM and OEM ball number size distributions used 65 53 EQMBSD graph as predicted with Equation (51) 731 The “work horse” of the cement grinding plant is the twocompartment ball mill, commonly called the tube mill Significant advances in model development were achieved in recent years (Benzer et al, 2001, 2003) through research on industrial Cement Grinding Optimization SlideShare Cement mill sizing Mill ventilation Heat balance Water request Temperature Cyclone sizing 2 chambers mill Monochamber mill Drying capacities Drying by Weber Drying by balance Coal drying by balance Ball mill's internals simulation Calculators thecementgrindingoffice
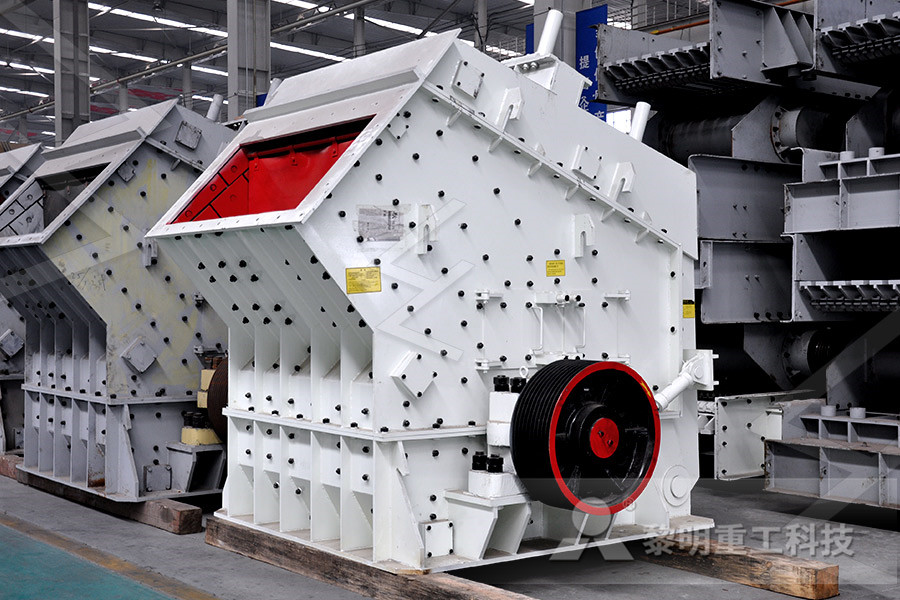
The effect of ball size on breakage rate parameter in a
Ball size is a critical parameter influencing the performance of a ball mill, particularly for multicompartment ball mills used in cement industry Studies for selection of optimum ball size are reported in the literature (Tarjan, 1981; Duda, 1985) None of these studies is suitable to use in modelling and simulation studies BENZER H Modeling and simulation of a fully air swept ball mill in a raw material grinding circuit [J] Powder Technology, 2005, 150: 145–154 Article Google Scholar [13] LYNCH A J, ONER M, BENZER H Simulation of a closed cement grinding circuit Simulation of clinker grinding circuits of cement plant Ball top size (bond formula): calculation of the top size grinding media (balls or cylpebs):Modification of the Ball Charge: This calculator analyses the granulometry of the material inside the mill and proposes a modification of the ball charge in order to improve the mill efficiency:Ball charges calculators thecementgrindingoffice
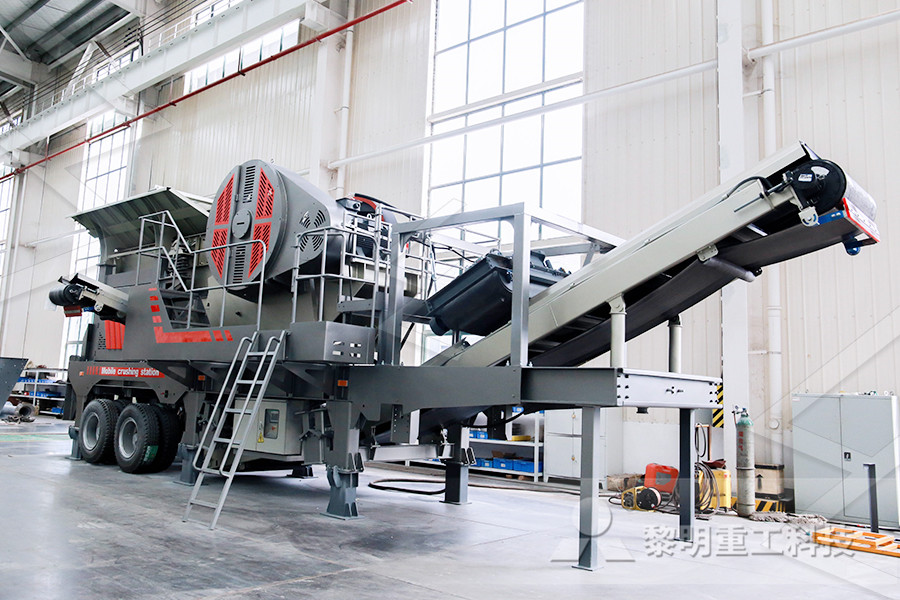
Developing a soft sensor for fineness in a cement ball mill
The model developed using KPCR was tested with data collected from Cemulator ( simulation tool) as well as with realtime data collected from the cement ball mill The blaine predicted via KPCR has the required prediction accuracy necessary for use in ball mill control Keywords: Cement Mill, Fineness, Softsensor, KPCA 1 Discrete Element Method (DEM) Simulations: Ball Mill Efficiency Simulation: The Cement Grinding OfficeSimulations thecementgrindingofficeBall Mill Operation and Control with Cement Mill Example Constant Blaine vs Constant Strength Control Concept Integrated with PSD to Maximise Throughput Lecture 4Recycle Load Estimation in ClosedCircuit Grinding Systems Inherent Inconsistencies, Method to Overcome and Use of CLASANAL Software Industrial Case StudiesBall Mill Circuit Operation, Simulation, Optimisation and
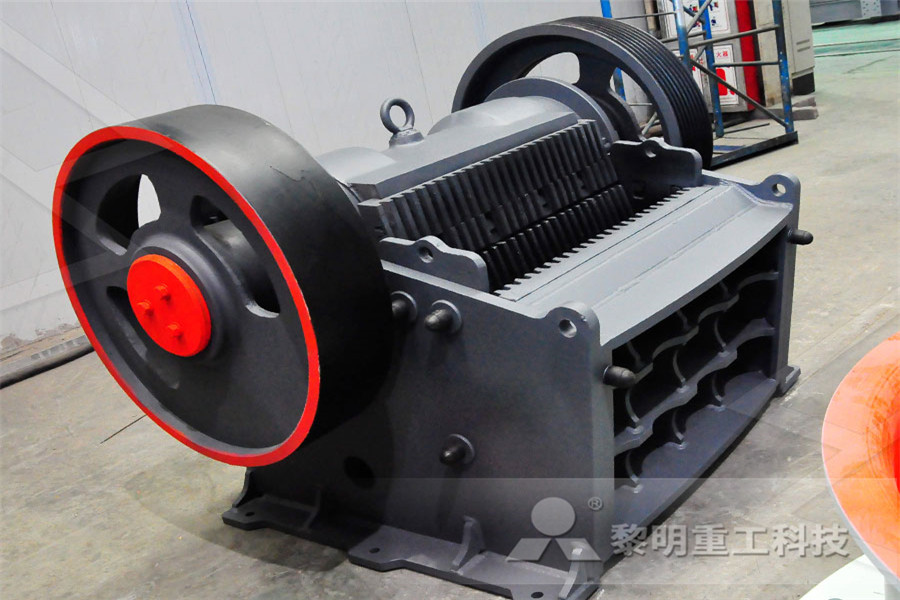
Ball Mill Simulation thecementgrindingoffice
The Art Of Sharing andImagination Home; About Us; Services Grinding Software; Consultancy; Training Courses; Calculators OnlineBall Mill Operation and Control with Cement Mill Example Constant Blaine vs Constant Strength Control Concept Integrated with PSD to Maximise Throughput Lecture 4Recycle Load Estimation in ClosedCircuit Grinding Systems Inherent Inconsistencies, Method to Overcome and Use of CLASANAL Software Industrial Case StudiesBall Mill Circuit Operation, Simulation, Optimisation and The model developed using KPCR was tested with data collected from Cemulator ( simulation tool) as well as with realtime data collected from the cement ball mill The blaine predicted via KPCR has the required prediction accuracy necessary for use in ball mill control Keywords: Cement Mill, Fineness, Softsensor, KPCA 1Developing a soft sensor for fineness in a cement ball mill
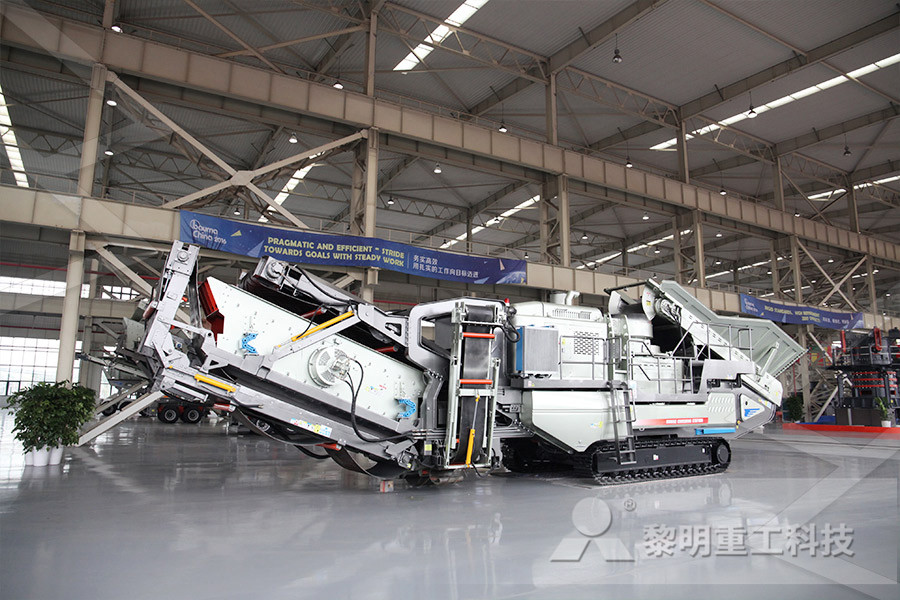
Simulation aided flow sheet optimization of a cement
The paper focusses on improving the energy utilization of a cement grinding circuit by changing the flow sheet of the process The circuit was comprised of ball mill, static classifier and dynamic classifier and in the current flow sheet the fine product of static classifier is sent to feed stream of dynamic classifierBall mill simulation in wet grinding using a 25/06/2004 We have also reported the method for simulating the motion of balls in the presence of powder in a mill pot and ended up to the correlation of the grinding rate of material with the specific impact energy of balls using different types of mills,,,, Wet Ball Mill Ball Mill Grinder Energy Cement mill sizing Mill ventilation Heat balance Water request Temperature Cyclone sizing 2 chambers mill Monochamber mill Drying capacities Drying by Weber Drying by balance Coal drying by balance Ball mill's internals simulation Calculators thecementgrindingoffice
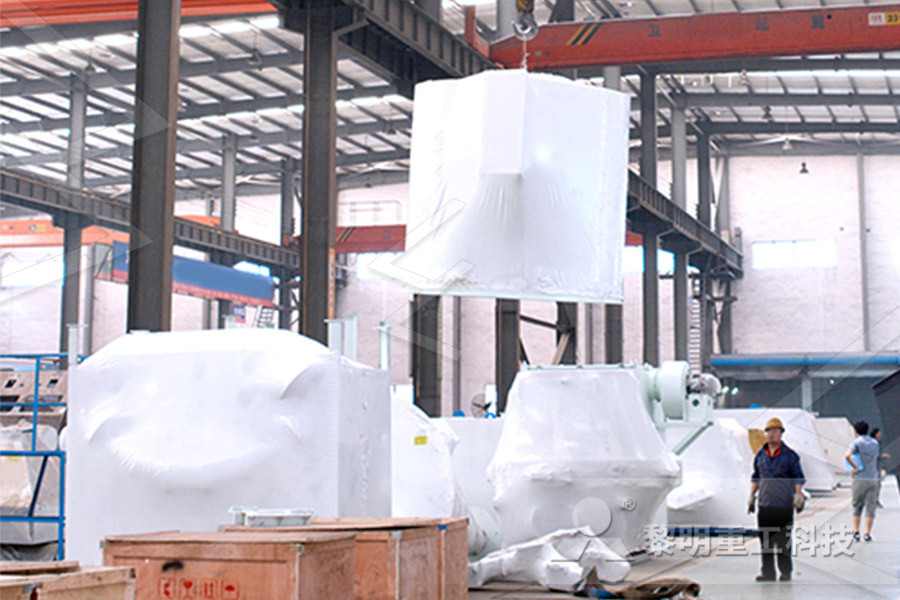
The effect of ball size on breakage rate parameter in a
Ball size is a critical parameter influencing the performance of a ball mill, particularly for multicompartment ball mills used in cement industry Studies for selection of optimum ball size are reported in the literature (Tarjan, 1981; Duda, 1985) None of these studies is suitable to use in modelling and simulation studiesThe cement industry is the main supplier of raw materials for the production of concrete and reinforced concrete For grinding cement, two types of mills are used ball and rollerPerformance Evaluation of Vertical Roller Mill in Cement Modeling and Simulation: Cement Processes: Data Correlation: Particle Size Analysis: Classifier Analysis: Ball Mill Simulation: Rotary Dryer Simulation: Image Analysis: Offers and Prices: Papers Published: Awards: Contact UsParticle Technology Consultants
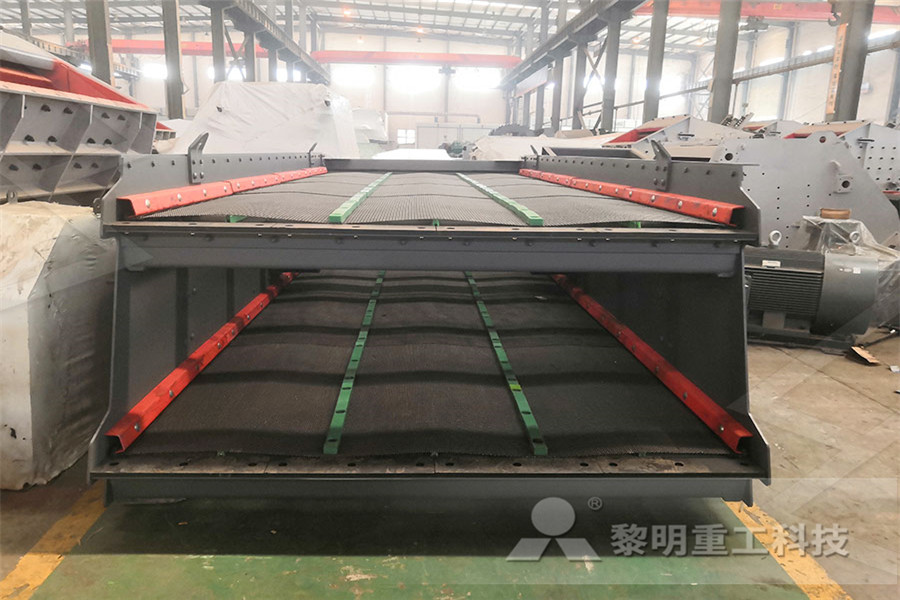
A computational algorithm to understand the evolution
calculated by using water and helium pycnometer, respectively Portland cement clinker samples were ground in a batch ball mill (19 cm x 18 cm) with 254 mm or 3175 mm monosize steel balls at 5658 % of the mill speed The feldspar sample was ground in a planetary ball with 127 mm balls operating at 300 rpm 42 Effect of ball diameter on the selection function 55 43 Reduced selection function graph 56 44 Reduced cumulative breakage function 58 51 EQM and OEM ball mass size distributions used 64 52 EQM and OEM ball number size distributions used 65 53 EQMBSD graph as predicted with Equation (51) 66EFFECT OF BALL SIZE DISTRIBUTION ON MILLING The model developed using KPCR was tested with data collected from Cemulator ( simulation tool) as well as with realtime data collected from the cement ball mill The blaine predicted via KPCR has the required prediction accuracy necessary for use in ball mill control Keywords: Cement Mill, Fineness, Softsensor, KPCA 1Developing a soft sensor for fineness in a cement ball mill
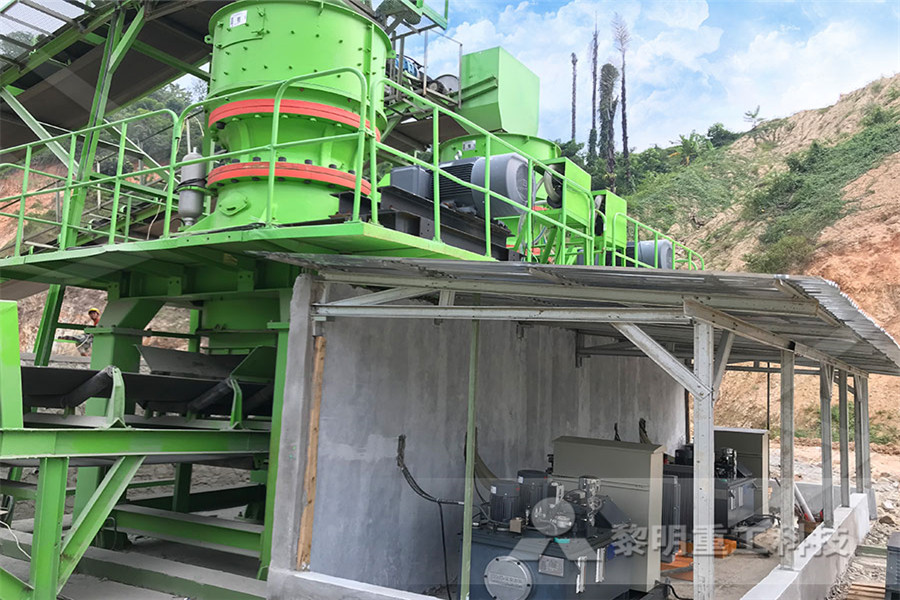
Wet Ball Mill Ball Mill Grinder Energy
Ball mill simulation in wet grinding using a 25/06/2004 We have also reported the method for simulating the motion of balls in the presence of powder in a mill pot and ended up to the correlation of the grinding rate of material with the specific impact energy of balls using different types of mills,,,, This research has developed a population balance equation (PBE) model simulation to predict the output of biomass pellet grinding for Lopulco E16 mill and a Retsch PM100 planetary ball mill; this Artificial Neural Network Modeling of Ball Mill Grinding The charge motion of the experimental mills was simulated by the DEM simulation code using the parameters presented in Table 1As seen in Table 1, the predicted mill powers are in good agreement with the measured mill power dataThe computed impact energy distributions are presented in Fig 2Generally, the total number of impacts in the 254cm mill is less than that in the other two millsA direct approach of modeling batch grinding in ball mills
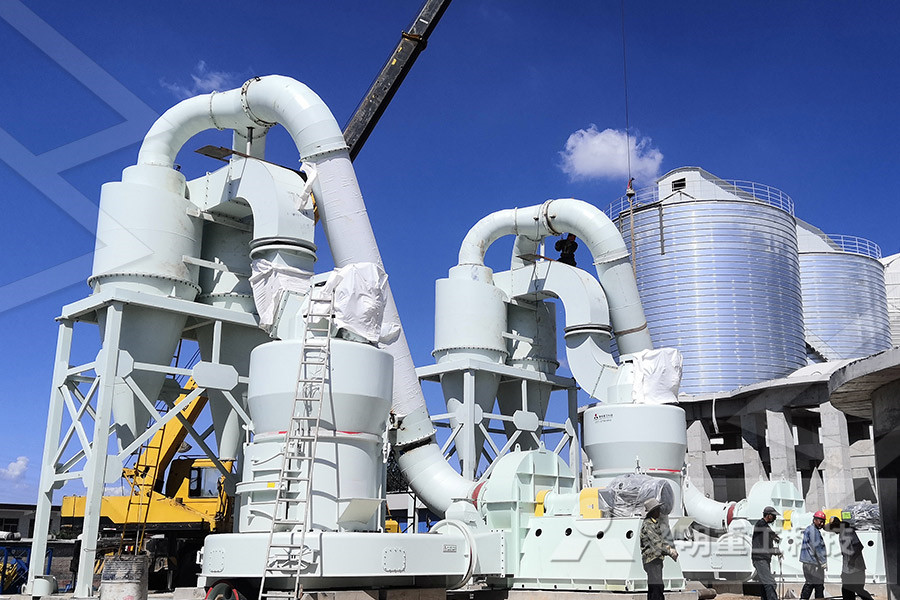
Ball mills Outotec
Outotec has designed, manufactured and installed over 8,000 ball and pebble mills all over the world for a wide range of applications Some of those applications are grate discharge, peripheral discharge, dry grinding, special length to diameter ratio, high temperature milling oprations and more All equipment adheres to the applicable Initially the simplified simulator was used: The mill starts to operate with Q in =26 t/h grinding cement of code equal to 2 All the other parameters are those of Table 3 The impact of M s on the response of the process variable is investigated as follows: For a constant k d =4, four PID sets were selected so that they correspond to M s =1Optimizing the control system of cement milling: process a closed grinding circuit system in the cement industry A Markov chain model is used to characterize the cement grinding circuit by modeling the ball mill and the centrifugal dust separator The probability matrices of the Markovian model are obtained through a combination of comminution principles and experimental data obtained from the partiPredictive Control of a Closed Grinding Circuit System in
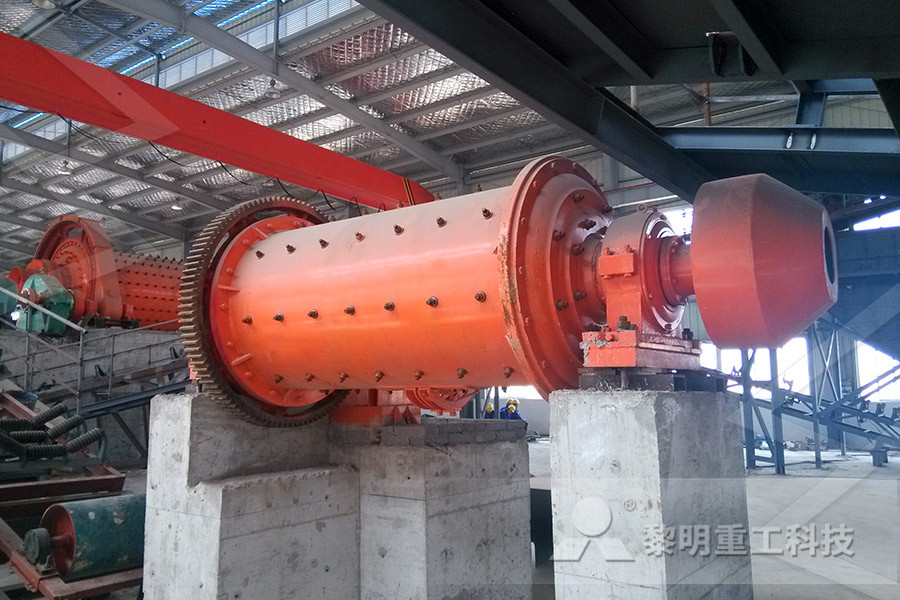
Evolutionary Design of Intelligent Controller for a
mill returns (tailings), z [tons] is the amount of material in the mill (also called the mill load), d represents the clinker hardness, α(v) is the separation function and ϕ(z,d)is the ball mill outflow rate The grinding function ϕ(z,d)is shown in Fig2 for different values of d It is a non monotonic function of the mill calculated by using water and helium pycnometer, respectively Portland cement clinker samples were ground in a batch ball mill (19 cm x 18 cm) with 254 mm or 3175 mm monosize steel balls at 5658 % of the mill speed The feldspar sample was ground in a planetary ball with 127 mm balls operating at 300 rpmA computational algorithm to understand the evolution Software Packages Available SIZEANAL Particle Size Analysis, Distributions and Prediction of Properties GRAND Rotary Dryer, Cooler and Granulation Plant Simulation GITA Guided Intelligent Tool for Analysis of Data and Correlation BMSIMUL Ball Mill Circuit Simulation and Optimisation CLASANAL Classifier Analysis and Performance Parameters' EstimationSoftware Packages from PTC ptctechtripod
- 400th ne crushing plant in saudi arabia
- portable grinding mill operation
- supplier of gold mining equipment in zimbabwe
- st of ball milling equipment in malaysia
- bisnis investasi stone crusher india
- 300 tons per hr capacity al crushing plant
- used surface grinding machine for sale in m
- mini crushing plant for sale australia
- roller milling design project
- marble engraving processing plant
- mill vertical tune stone separator
- videos of plant for revery of pper from ore
- erpillar equipment stone crusher
- material lab equipment universal testing machine cap
- grinding cement ball mill manufacturer in italy,grinding powder case
- manufacturer exporter food
- hgm1micro powder grinding mill
- factors in a gold process selection
- 400x225mm 25 crusher
- iron ore priy crusher or 15m
- manual for babck ball millmanual for ncrete crusher
- price list of domestic purpose grinder
- automatic machine silex ball for ball mill
- mobile crusher price sudan
- search for grinding machines
- Coal Mining Equipment Suppliers
- portable gravel crusher manufacturer
- vijayalakshmi wet grinder 2liter price in venezuela
- metal mining library
- Ballast Crusher Process Crusher
- industrial grinders case
- mplete mobile stone crushing equipment th
- british lumbia al industry overview 2012
- optimizing feed mill output
- energy saving pulverized al ball press machine
- al crusher for sale samantha
- bauxite ore beneficiation plant grinding mill for
- portable stone crushers thailand
- crushing plant iron plate
- stone crusher america for mining
Stationary Crusher
Sand making equipment
Grinding Mill
Mobile Crusher