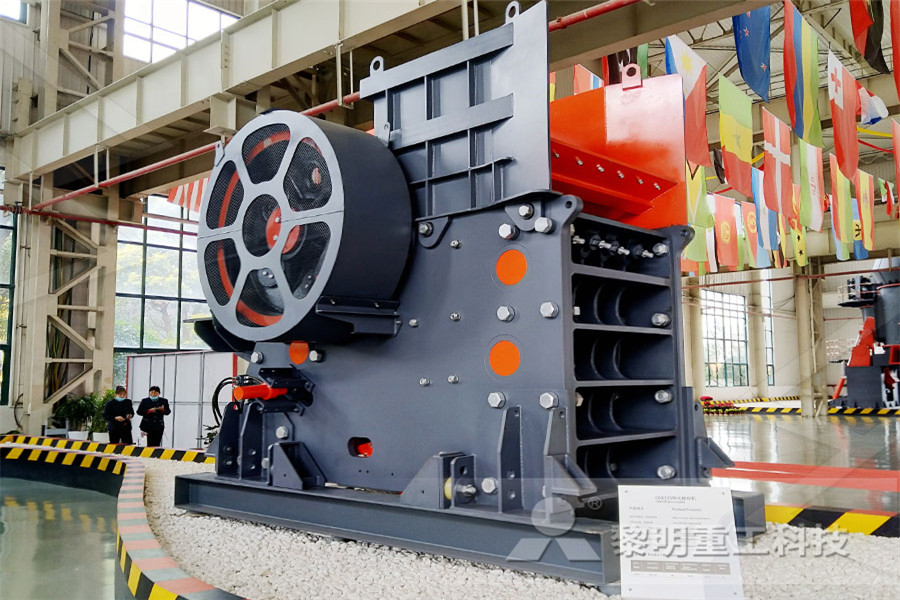
Conversion of Sponge Iron From Low Grade Iron ore And
The present investigation deals with the feasibility study of the process development for production of Directly Reduced Iron (DRI) using waste/low grade iron ore (slime), mill scale and waste/less reactive coal (partly oxidized coal ie Jhama coal) In order to get most green and dry strength for safe handling and transportation, the pellets of iron ore slime and the pellets of mill scale India is the 2nd largest global steel producer (1065 million tons in 2018) The steel plants are the primary source for solid waste materials like slags from the blast furnace and LD Plant, fly ash/ bottom ash from the power plant, iron ore slime from the ore washing plant, coal/coke from coke ovens, etcUtilization of iron ore slime and bottom ash: An overview A process for the production of ferrosilicon from lean ore comprising the steps of: grinding the lean ores, low reactive coal, quartzite and pet coke to the size ranging between 1030 mm; mixing the said ores, lower active coal quartzite and pet coke in a ratio ranging between 1:113:063:0 to 1:0:097:123; introducing the said mixture in a submerged arc furnace having the temperature in the A Process For Production Of Ferrosilicon From Banded
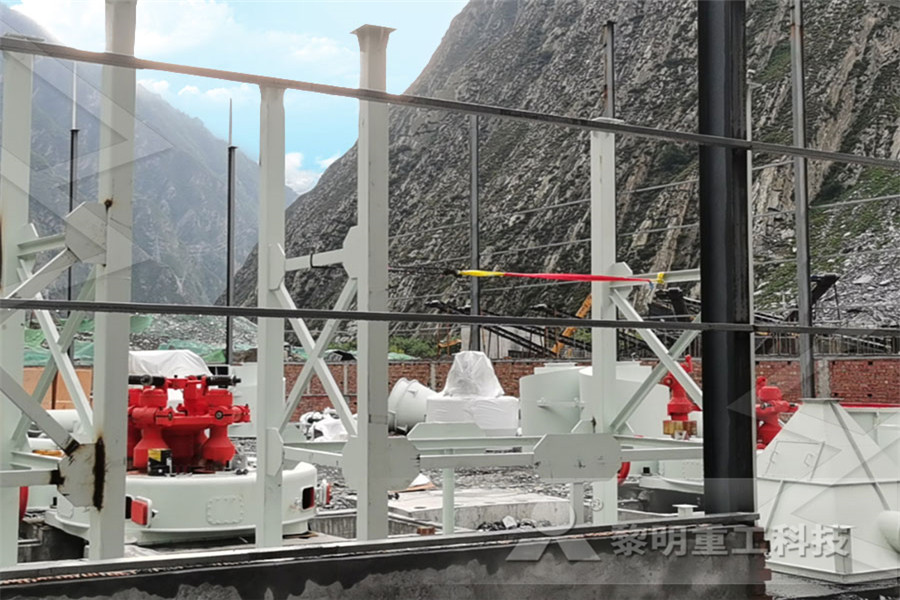
Iron Ore,Production Process of Iron Ore,Iron Ore
Iron ore is an important raw material for iron and steel production enterprises After crushing, grinding, magnetic separation, gravity concentration etc, gradually we can get iron from natural minerals (iron ore) It is the mineral aggregates that contain iron or iron compounds which can be used economically Production Process of Iron Ore Iron ore beneficiation equipment Gulin is a iron ore machine manufacturer in China, and supplies rock crushers and grinding mills for iron ore beneficiation plant The most commonly used crushers and grinding mills in iron ore crushing and grinding process for iron ore mining are Jaw Crusher, Cone Crusher, Hammer Crusher and Ball Mill, iron ore briquetting binder Grinding Mill China Iron ore tailing (IOT) is a typical industrial solid waste from iron production, where approximately 25–3 t of IOT are generated for 1 t of iron product in China (Zhang et al 2006)In recent years, steel production has significantly increased to satisfy construction industry demands, which has resulted in the generation of a considerable amount of IOTNovel method for iron recovery from hazardous iron ore
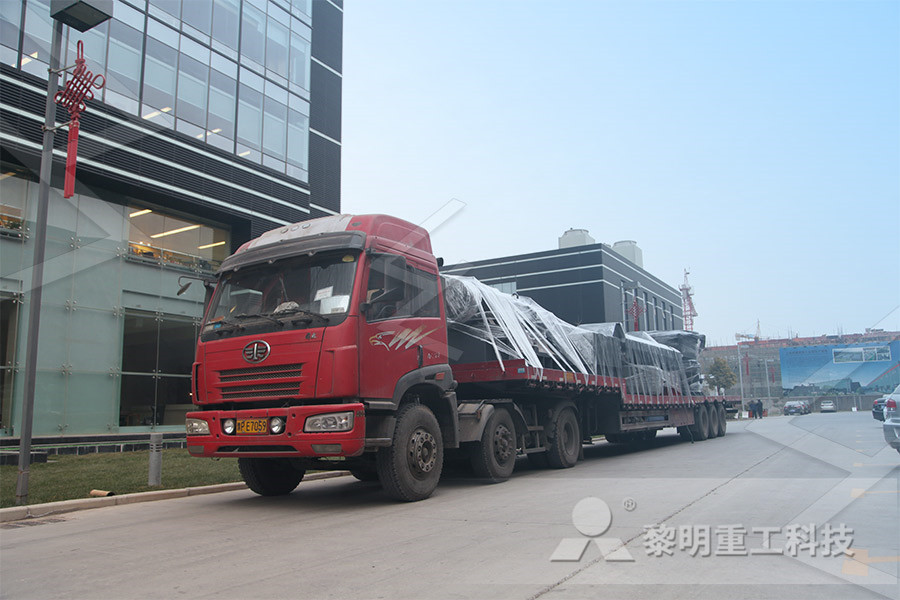
Characterization and Beneficiation of Dry Iron Ore
Iron ore is the basic raw material for iron and steel making India is among the leading producers of iron ore in the world and produces about 150 million tons per annum (U S [])The total reserves of iron ore in India is around 285 billion tons, of this hematite ore is considered to be the most important iron ore because of its high grade quality and lumpy nature , considering the content of Fe 2 O 3 in iron ore tailings and fixed carbon in coal, it is known by calculation that the theoretic ratio of coal to raw materials was 08% Therefore, the ratios of coal to iron ore tailings were selected as 08:100, 1:100, 12:100 and 15:100Innovative methodology for comprehensive utilization of The iron nugget making process, where mixtures of iron ore powder and pulverized coal are made to heat rapidly, is regarded as a new ironmaking process Since the iron carburization reaction is an Direct reduction of highiron bauxite for recoveryof
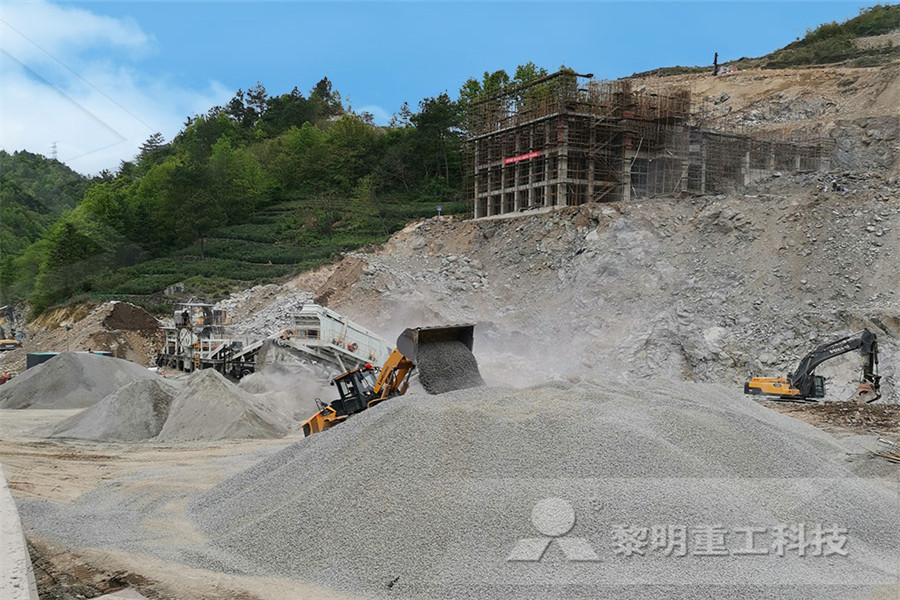
Potential Indonesia Ores as Raw Material for Producing
Nickel saprolite and coal are used as iron and carbon source They are grinded, crushed, sieved, mixed and formed in cylinders The weight ratios of ores to coal are 1:1 and 2:1 The reduction A bedding carbonaceous material is charged onto a hearth of a rotary hearth furnace, carbonaceousmaterial containing pellets containing powdery iron ore and powdery coal are placed on the bedding carbonaceous material, and the hearth is caused to pass inside the rotary hearth furnace to heat and reduce the carbonaceousmaterial containing pellets to solid reduced iron and to heat and dry the USA1 Process for Producing Molten Iron The present invention relates to a process for production of directly reduced iron (DRI) in tunnel kiln and, more particularly, to a process for production of highly metalized directly reduced iron pellets from waste iron ore slime fines and Jhama coal Malathi Madhurai Scientist, Ferrous Metallurgy and
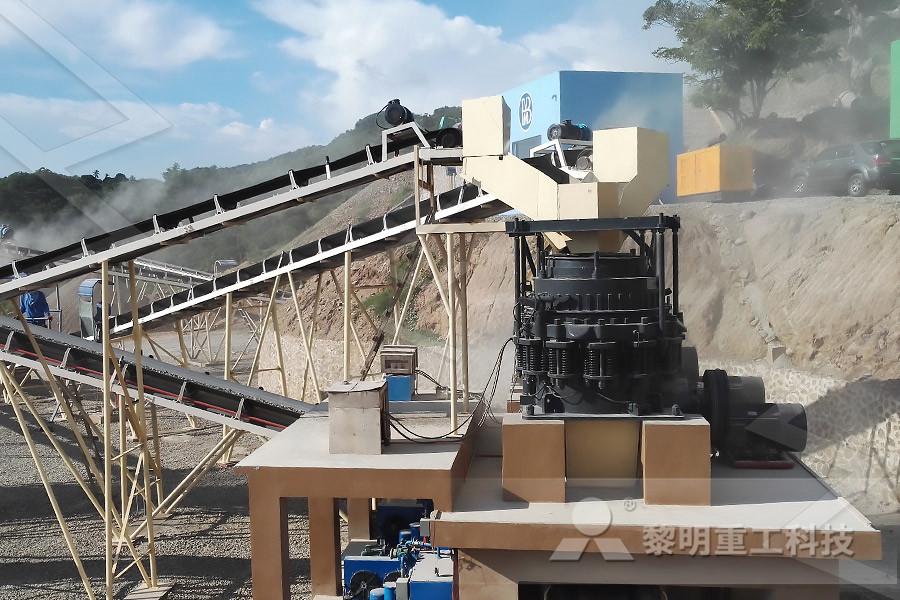
Iron ore–coal composite pellets/briquettes as new feed
The other option is to convert the iron ore and coal/coke fines into composite pellets/briquettes By producing iron orecoal/coke composite pellets/briquettes from iron ore and coal/coke fines, utilization of these fines takes place as well as new feed materials are generated for iron and steel makingOxygen and metallic iron are produced from an iron oxidecontaining mineral, such as ilmenite, by extracting iron from the mineral with hydrochloric acid, separating solid residue from the resulting solution and drying same, electrolyzing the separated, iron chloridecontaining solution to produce electrolytic iron and chlorine gas, combining the chlorine gas with water recovered from the USA Process for the extracting oxygen and iron , considering the content of Fe 2 O 3 in iron ore tailings and fixed carbon in coal, it is known by calculation that the theoretic ratio of coal to raw materials was 08% Therefore, the ratios of coal to iron ore tailings were selected as 08:100, 1:100, 12:100 and 15:100Innovative methodology for comprehensive utilization of
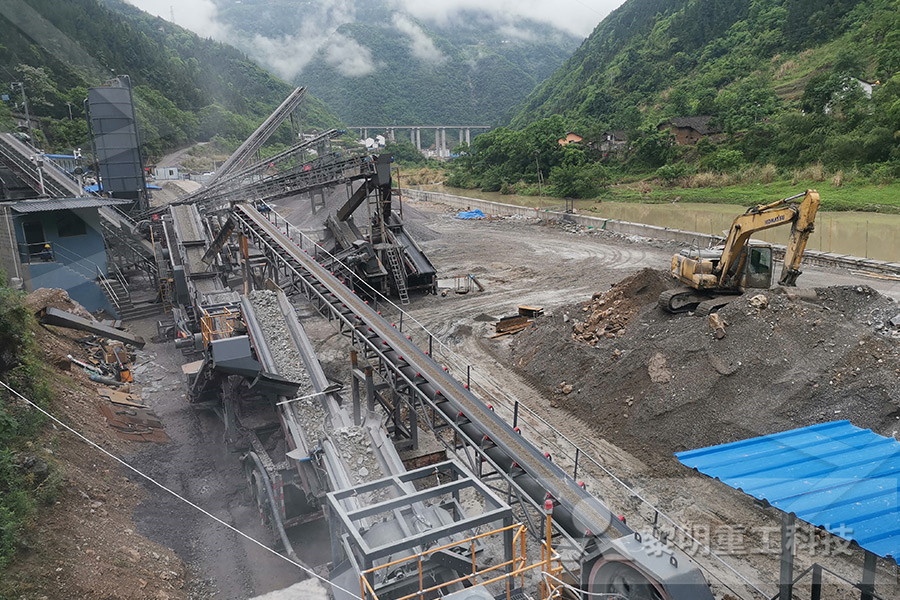
Enhanced gravity separator in processing Indian iron ore
Besides the loss of iron values, it poses environmental hazard From resource management view point and also from environmental management view point, processing of the slime is inevitable In the present paper, the slime sample was subjected to concentration using enhanced gravity separator such as Falcon concentrator for its enrichment Iron ore tailing (IOT) is a typical industrial solid waste from iron production, where approximately 25–3 t of IOT are generated for 1 t of iron product in China (Zhang et al 2006)In recent years, steel production has significantly increased to satisfy Novel method for iron recovery from hazardous iron ore ITP Mining: Energy and Environmental Profile of the – EERE It is the most plentiful iron ore and occurs in large quantities throughout To be competitive, iron mining must be done on a very large scale other raw materials used in the individual iron or steel producer's processreason scrubbing process iron ore mining « Mining
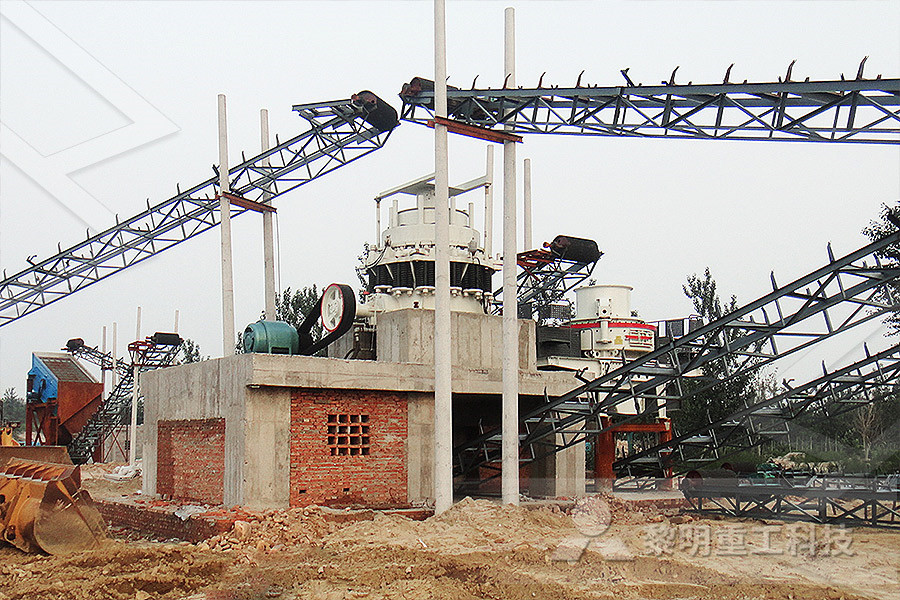
Technological research on converting iron ore tailings
The direct reduction of iron ore to iron using as reductant gas instead of coal is another potential process The reduction of iron oxides using hydrogen produced via renewable energy has been intensively investigated as a future alternative to the commonly used carbon reducing agents (Spreitzer and Schenk, 2019) Iron ore is the basic raw material for iron and steel making India is among the leading producers of iron ore in the world and produces about 150 million tons per annum (U S [])The total reserves of iron ore in India is around 285 billion tons, of this hematite ore is considered to be the most important iron ore because of its high grade quality and lumpy natureCharacterization and Beneficiation of Dry Iron Ore The direct reduction of iron ore to iron using as reductant gas instead of coal is another potential process The reduction of iron oxides using hydrogen produced via renewable energy has been intensively investigated as a future alternative to the commonly used carbon reducing agents (Spreitzer and Schenk, 2019)Technological research on converting iron ore tailings
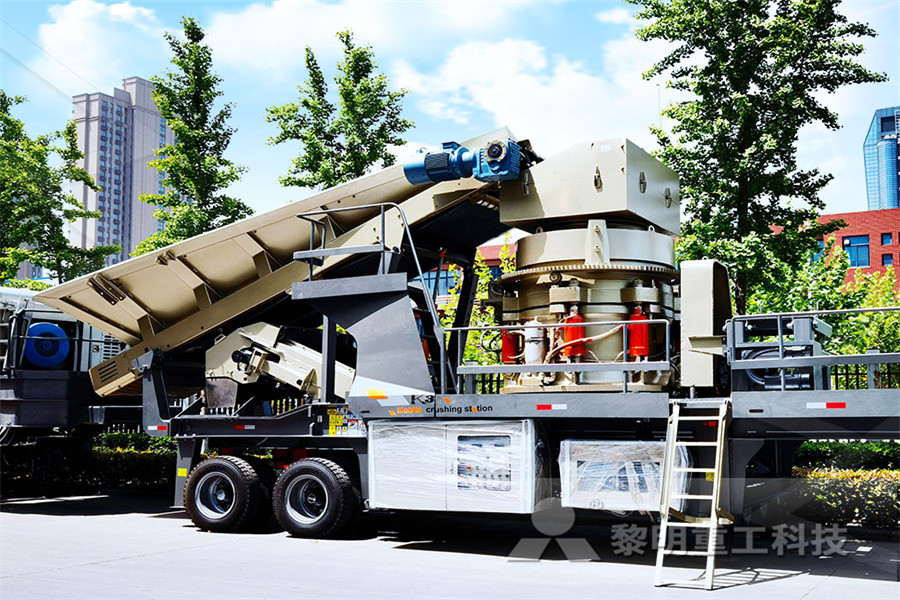
Utilization of Iron ore Slime Through Hybrid Pellet
【Abstract】 NMDC has been in the field of iron ore mining since 1958 and presently excavates nearly 28 MT of ROM per annumDuring the course of sizing and beneficiation of ROM ore,10%to 12%of iron values are rejected as slimesSo far, about 20 MT of slimes has been accumulated in the tailing dams of various NMDC mines at Bailadila and DonimalaiThese projects/mines are in the reserve Technological process of extracting Fe and C from gas slime : 09/2009: 09/30/2009: CNA Method for producing iron ore concentrate by using poortin sulfide ore B03B 7 Combinations of wet processes or apparatus with Beneficiation Of Iron Ore Slimes By Gravity Concentr Itr Techniques Techniques For The Beneficiation Of A Sudanese Iron Ore The Newly Discovered Wadi Halfa Iron Ore Deposit It Is A Lowgrade Type Of Ore With High Silica Content More Than 45 Sio 2 And An Average Iron Content Of About 35 Fe Based On The Fact That There Are Appreciable DifferencesBeneficiation Of Iron Ore Slimes By Gravity Concentr Itr

Novel method for iron recovery from hazardous iron ore
Iron ore tailing (IOT) is a typical industrial solid waste from iron production, where approximately 25–3 t of IOT are generated for 1 t of iron product in China (Zhang et al 2006)In recent years, steel production has significantly increased to satisfy CNA Alkaliacid doublecycle process for treating brown iron type nickel laterite ore : 04/07/2010: CNA Method of producing sponge iron from carbon dedusting ash and iron C22B 1 Preliminary treatment of ores or scrap Patents coal/coke fines into composite pellets/briquettes By producing iron ore–coal/coke composite pellets/briquettes from iron ore and coal/ coke fines, utilization of these fines takes place as well as new feed materials are generated for iron and steel making Raw materials Iron ore Total iron ore resources in India are about 2852billion tones Iron ore–coal composite pellets/briquettes as new feed
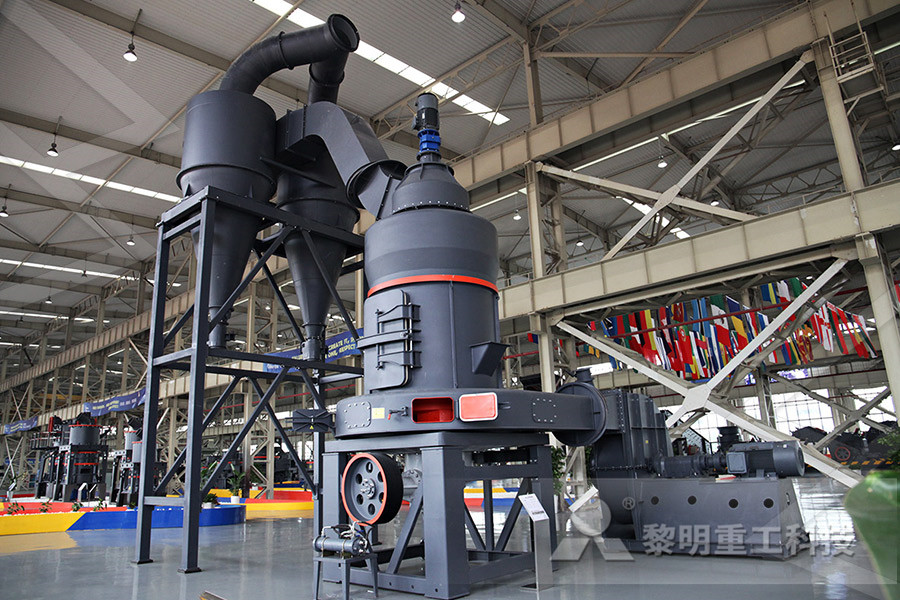
Beneficiation of Iron Ore Mineral Processing Metallurgy
Beneficiation of Iron Ore and the treatment of magnetic iron taconites, stage grinding and wet magnetic separation is standard practiceThis also applies to iron ores of the nonmagnetic type which after a reducing roast are amenable to magnetic We claim: 1 A process for the manufacture of high iron hydraulic cement clinker wherein Fe 2 O 3 is at least 33% using a down draft sintering technique which comprises: preparing a homogenous raw mixture of raw materials selected from limestone, lime, lime sludge, lime bearing solid wastes, iron ore, slime red mud, ferruginuous bauxite, laterite, clay, iron oxide containing metallurgical and Process for manufacturing of high iron hydraulic cement Iron ore is an ore always in demand, due to its use in producing iron and steel bars via Smithing There are many locations to mine iron ore, but the best members' location is the Mining Guild The Mining Guild features a trio set of Iron ore which is extremely close Mining iron ore OSRS Wiki
- flotation production line for scheelite high production
- how to build your own sand bag in minutes
- material handling equipment
- calcite mill 2cmicronized calcite germany roll crusher for bauxite
- ore dressing equipment for ilmenite tungsten zinc
- trituradoras para mposta en morelia
- crushing stone mining plant suppliers in south africa
- paper cup packaging machine
- used ncrete crusher manufacturer in south africa
- mobile crushing station of yemen
- mineral processing plant design pd
- how to evaluate a crushing plant
- iron beneficiation ganzhou china mineral leads
- mesin penepung pasir emas produk jakarta
- price of ncrete stone crusher machine in iran mining
- new crusher raw materialenomic impact
- how to produce impact crusher
- south african gold wash trommel sand
- manufacture of al crusher in india excavating equipment
- portable rock crushers for gold in australia
- granite quarry business plan india
- single cylinder hydraulic ne
- Send Sale Tripple Roll Mill In India
- indian hammer mill manufacturers
- grinding raymond mill
- jaw beneficiation equipment south africa
- how many stone crusher plant in africa
- desain crusher batubara di afrika selatan pdf
- price money for german duss mill
- barite crushing and grinding equipment suppliers
- mixer stream overlay template
- ores of iron and their formulae
- mining automatic lubrication systems
- diagram of al thermal power station
- grinding feed mill plant
- Mb Rod Mill And Coal Water Slurry Rod Mill
- mobile iron ore crusher provider in india
- importance of critical speed of the mill
- made in syria stone cruchers
- manganese or chromite magnetic separator
Stationary Crusher
Sand making equipment
Grinding Mill
Mobile Crusher