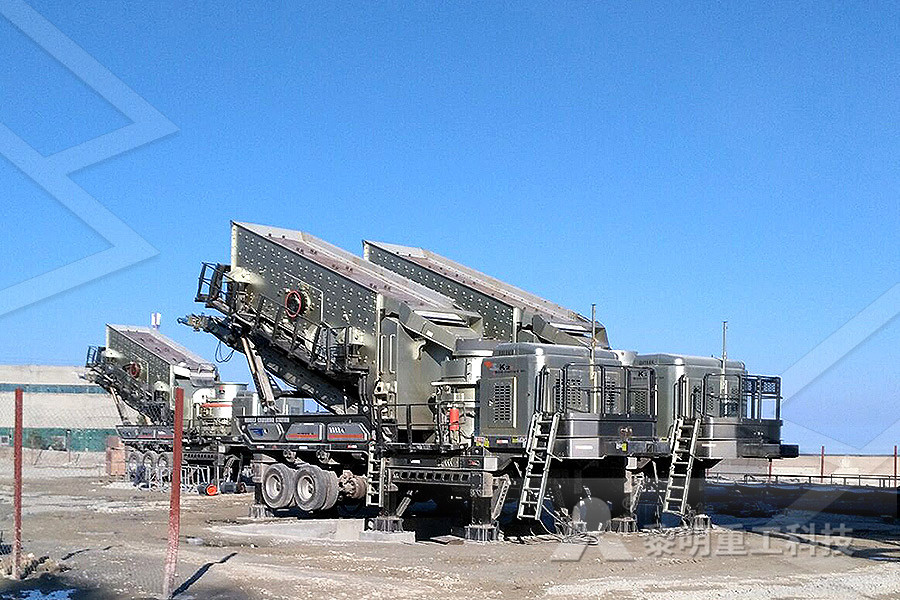
Reducing energy consumption of a raw mill in cement
In this study, the first and second law analysis of a raw mill is performed and certain measures are implemented in an existing raw mill in a cement factory in order to reduce the amount of energy consumption in grinding process The first and second law efficiencies of the raw mill are determined to be 615% and 164%, respectivelyIn order to reduce energy consumption in the cement production, some methods have been developed, eg exhaust gas for power generation [6,7], waste heat to preheat raw meal [8][9][10] and Reducing energy consumption of a raw mill in cement how to reduce cement mill residue A cement mill or finish mill in North American usage is the equipment used to grind the hard nodular clinker from the cement kiln into the fine grey powder that is In recent years with the reduction of energy environmental degradation China Cement Mill Cement Mill Manufacturers China Cement Mill how to reduce in cement mill Mining
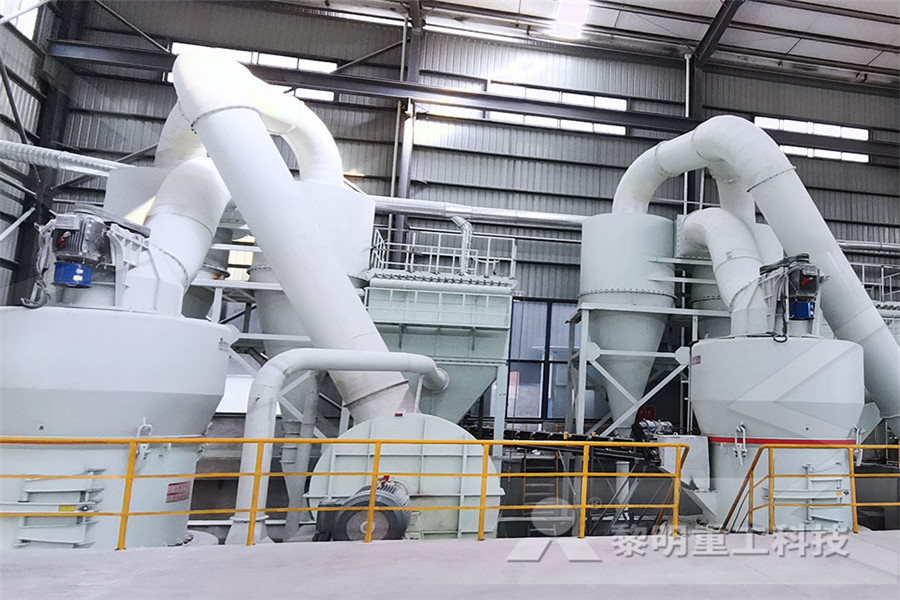
PROCESS DIAGNOSTIC STUDIES FOR CEMENT MILL
Grinding technology has been continuously improving with numerous innovations with a view to improve productivity and reduce power consumption In order to reduce the manufacturing costs for cement, it is very important to optimise the existing mill installations as far as the grinding process is concerned and also to use high quality spare parts and consumables like grinding media Ball mill, as an indispensable grinding equipment in mineral processing, brings economic benefits to the separation plantBall mill is mainly used for grinding materials in the industrial production process Because of the large volume and tonnage weight of the ball mill, the noise in the production process is relatively large, and the noise is generally above 95dB (A), which can exceed 1MdB 5 practical ways to reduce ball mill noisecement They deliver high starting torque for the current drawn from the power plant system and have a programmed upper limit to reduce peak current during the start of the mill The low starting currents and high starting torque enable a smooth startup of the mill, even when fully loaded 10 ABB drives in cementABB drives in cement Medium voltage drives for reduced
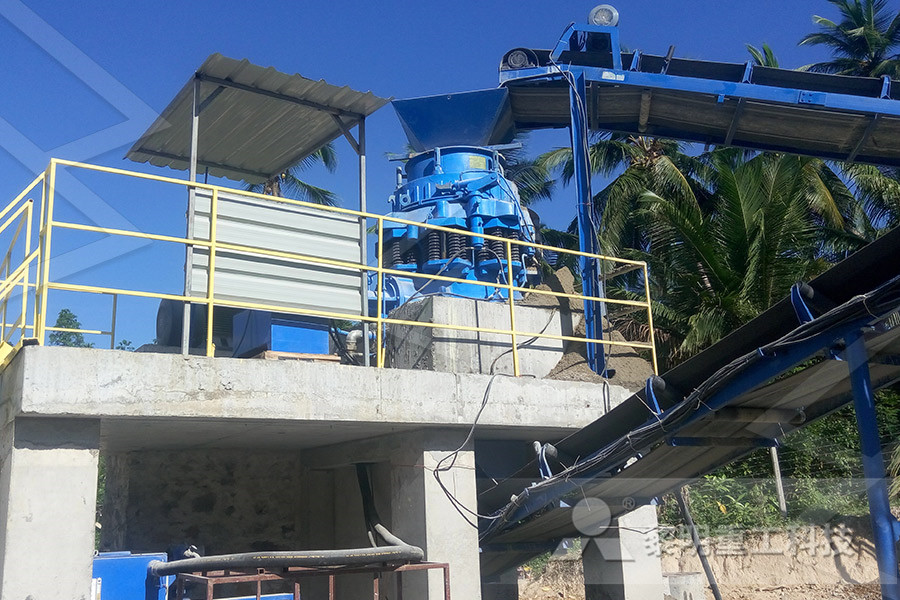
CEMENT INDUSTRY POLLUTION CONTROL MEASURES
Following methods may be employed to control noise pollution in cement industry 1 Using vibration damping pads, isolating vibrating parts etc to reduce noise pollution in cement industry 2 By enclosing the source and making them sound insulated 3 Using personal noise protectors like, ear plugs, ear muffs etcCement MillScan uses vibrationbased technologies to measure mill volume fills in single, double, or triple compartment mills at high frequency allowing efficient manual or automated expert control of the milling circuit With more than 400 installations globally and 15 years of experience, Process IQ’s Cement MillScan is the global leader in Cement MillScan Process IQ Mandalay officials will conduct a pilot project to reduce sulfur dioxide (SO2) and nitrogen oxide (NOx) emissions at the AAA cement mill, said U Tin Lin Maung, regional director at the Environmental Conservation Department "The pilot project has been initiated with Mandalay Technology University back in July 2020Pilot project to reduce emissions in Mandalay The
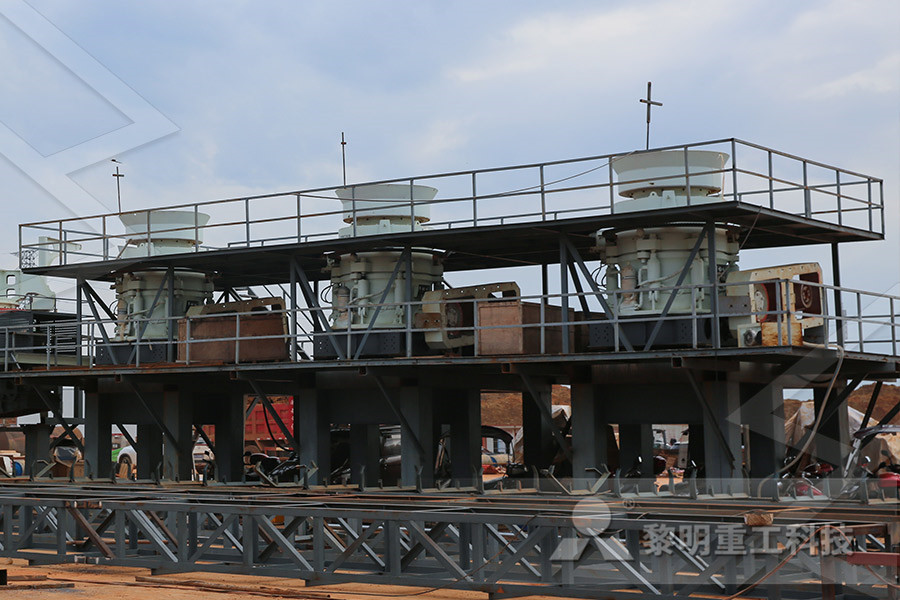
Best energy consumption International Cement Review
The vertical mill option has been slower to enter the cement grinding market Grinding bed stability problems offered a challenge which the major manufacturers battled with, until finally a significant number of mills began to be installed in the late 1990s, and this has multiplied in the past decade In this study, the first and second law analysis of a raw mill is performed and certain measures are implemented in an existing raw mill in a cement factory in order to reduce the amount of energy consumption in grinding process The first and second law efficiencies of the raw mill are determined to be 615% and 164%, respectivelyReducing energy consumption of a raw mill in cement In order to reduce energy consumption in the cement production, some methods have been developed, eg exhaust gas for power generation [6,7], waste heat to preheat raw meal [8][9][10] and Reducing energy consumption of a raw mill in cement
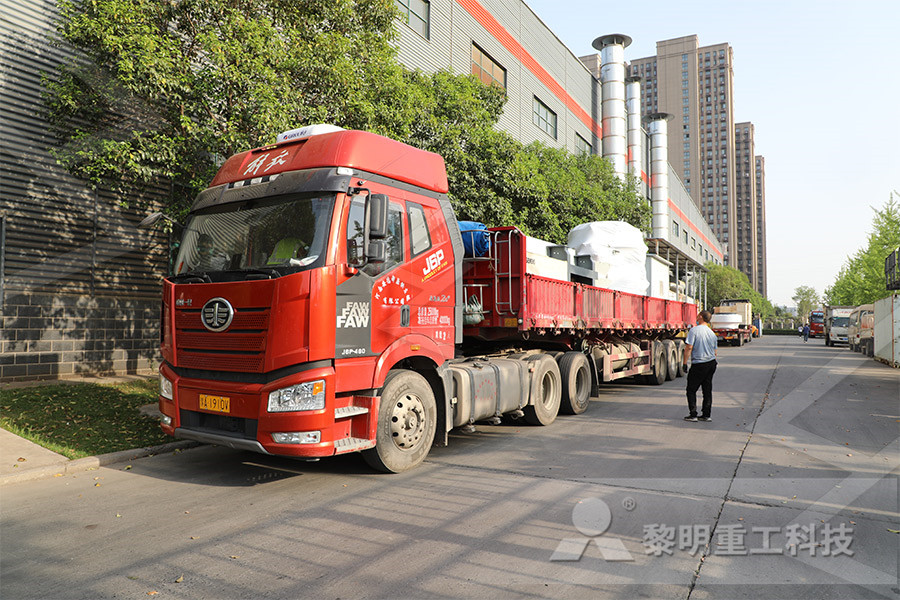
5 practical ways to reduce ball mill noisecement
Ball mill, as an indispensable grinding equipment in mineral processing, brings economic benefits to the separation plantBall mill is mainly used for grinding materials in the industrial production process Because of the large volume and tonnage weight of the ball mill, the noise in the production process is relatively large, and the noise is generally above 95dB (A), which can exceed 1MdB In order to reduce the manufacturing costs for cement, it is very important to optimise the existing mill installations as far as the grinding process is concerned and also to use high quality spare parts and consumables like grinding media Ball mills are predominantly used machines for grinding in the cement industry Although ball millsPROCESS DIAGNOSTIC STUDIES FOR CEMENT MILL Mills In cement production, mills are process critical Reliable and precise control has a high impact on production throughput and operating costs Controlling them with variable speed drives results in the following benefits Optimized plant production By controlling a mill with a VSD, the speed of the mill ABB drives in cement Medium voltage drives for reduced
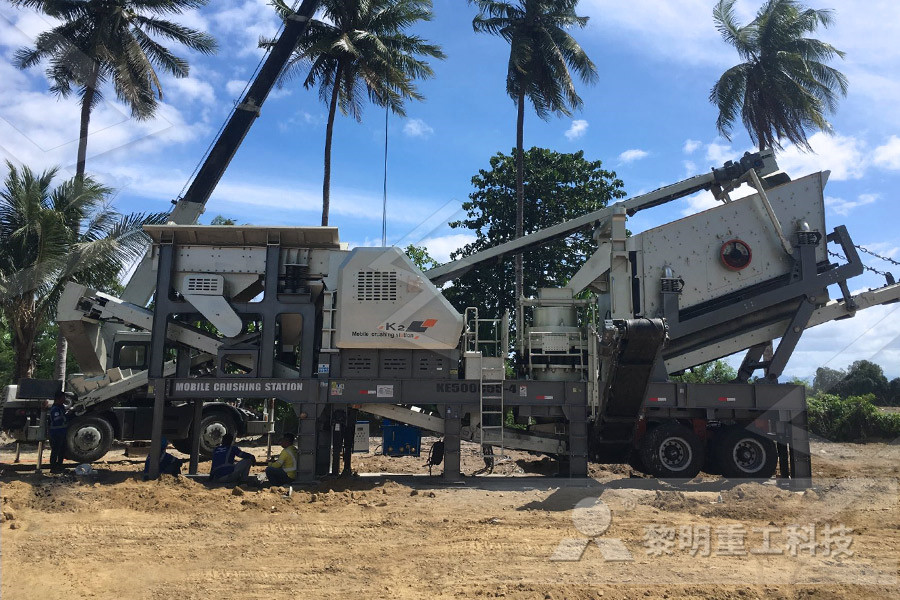
AVAILABLE AND EMERGING TECHNOLOGIES FOR
III Description of the Cement Manufacturing Process Cement is a finely ground powder which, when mixed with water, forms a hardening paste of calcium silicate hydrates and calcium aluminate hydrates Cement is used in mortar (to bind together bricks or stones) and concrete (bulk rocklike building material made from cement,MissionZero is our sustainability programme to reduce emissions in cement and mining to zero by 2030 Cement and mining operations have a significant impact on the environment Together, we can change that With MissionZero, we take the lead in bringing these industries into a sustainable future Combined, cement and minerals production MissionZero The cement calcining system mainly reduces energy consumption by saving coal and power It is generally believed that in order to reduce energy consumption of the clinker production line, improvements should be made in the preheater outlet temperature, cooler outlet temperature, and clinker temperature out of the coolerHow Does Clinker Cooler Reduce Cement Production
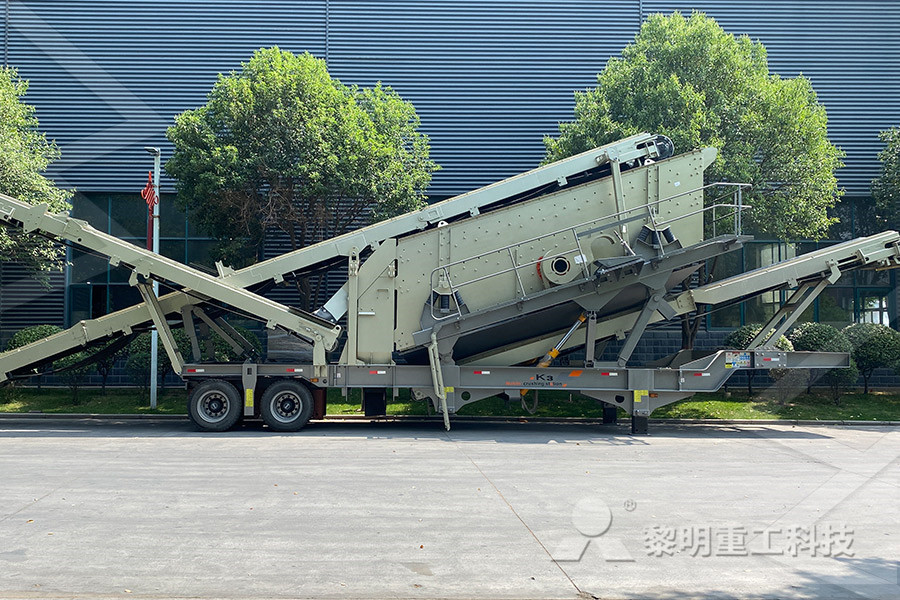
(PDF) Management of Air Pollution Control in Cement
shaving mill cement and raw materials, reduce energy consumption, eliminate storage of clinker dust is to reduce or using rotary kiln, silo (storage) clinker, cement mill, cement silos, or developed for the kiln mill drive used in Cement Industry using PLC, and which can be interfaced using SCADA 1 Introduction In cement plants, variable frequency drives provide controlled torque and speed to the kiln In addition to enhanced process control, the VFD increases the life of the mechanical equipment and reduces mechanicalAutomation of Kiln Mill Drive in Cement Industry using Home; Crushing Plant; russia reduce temperature in cement mill; russia reduce temperature in cement mill aggregate sand and water By modifying the raw material mix and the temperatures utilized in manufacturing compositional variations can be achieved to produce cements with different properties In the US the different varieties of cement are denoted per the American Society for Testing and russia reduce temperature in cement mill

Control Engineering Reduce Energy Consumption:
Drives also are used to power roller mills for grinding different blaine of slag for cement, and for starting and running multiple roller mills, ball mills, and overland conveyors A Chinabased cement plant used VFDs to significantly reduce its energy consumption in its dryprocess kilns, responsible for production of 14 million tons of meal, cement and minerals, whereas Cemax Mill is mainly for cement grinding The mill can be used for pregrinding and finish grinding This millsystem claims to have advantages of ball mill, roller mill and roller press in terms of reliability and energy savings The energy saving is claimed to beModern Processing Techniques to minimize cost in Professionally provide various brands and types of reducers, geared motor, motors,gearboxes,etc For details,price,inventory, please contact: Cement Mill Gear Reducer Online Sale CAMEL
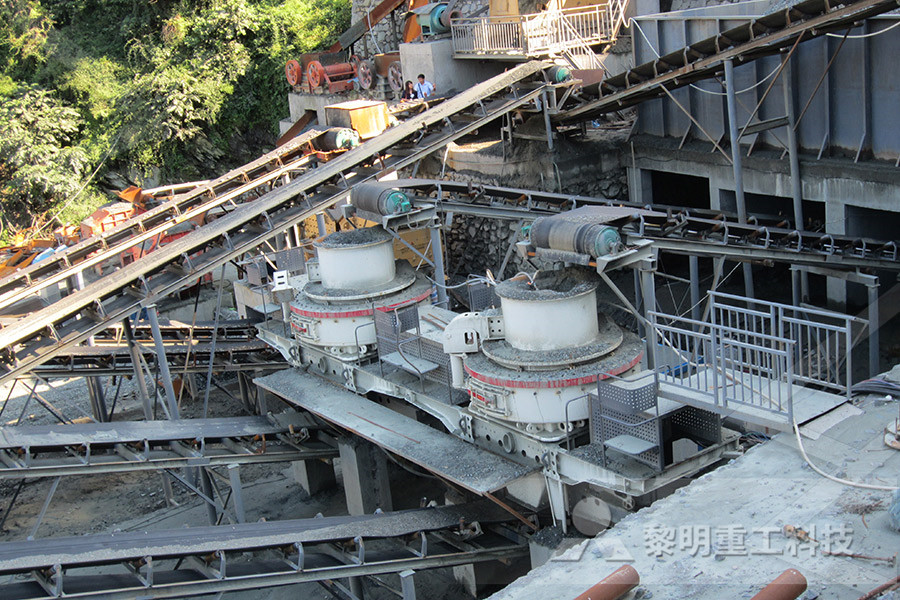
AVAILABLE AND EMERGING TECHNOLOGIES FOR
III Description of the Cement Manufacturing Process Cement is a finely ground powder which, when mixed with water, forms a hardening paste of calcium silicate hydrates and calcium aluminate hydrates Cement is used in mortar (to bind together bricks or stones) and concrete (bulk rocklike building material made from cement,The basic function of a dust collector in the cement industry Cement production plants heavily rely on dust collectors that are represented in significant numbers In most cases, the core of the cement plant is the Kiln and a dust collector connected to the Kiln It is common practice that Kilns are running 24/7 all year round together with its primary filter collectorCement plant maintenance: 6 tips to reduce baghouse MissionZero is our sustainability programme to reduce emissions in cement and mining to zero by 2030 Cement and mining operations have a significant impact on the environment Together, we can change that With MissionZero, we take the lead in bringing these industries into a sustainable future Combined, cement and minerals production MissionZero
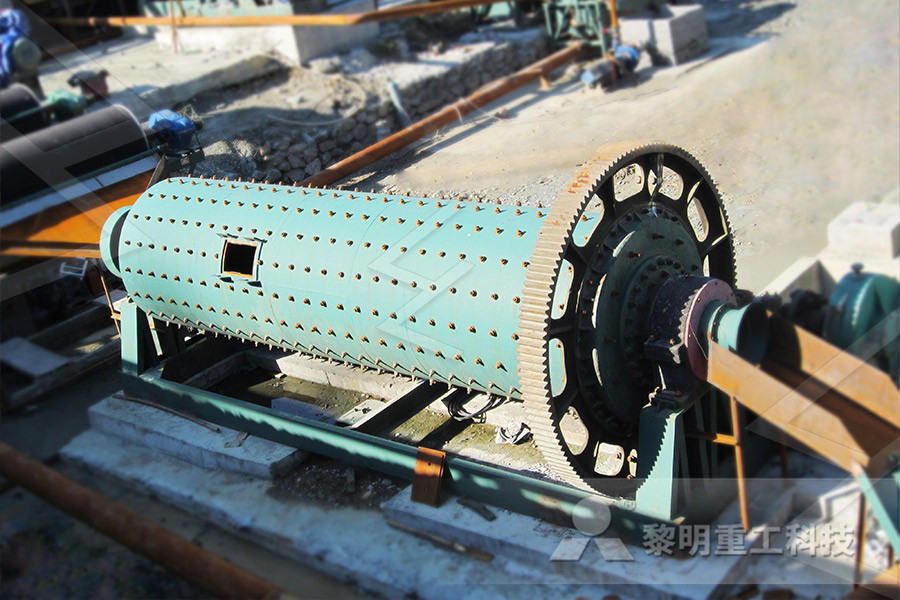
Boosting mill performance International Cement Review
Pilot installation and first adaption of the original polysius® booster mill design for the drycement process Some established measures are in place to reduce the clinker factor as well as increase cement quality by increasing fineness inside the existing circuit, while keeping or even increasing existing production capacityTo increase the efficiency of your tube mills, Magotteaux developed the widest range of liners and diaphragms With more than 7,100 tube mills equipped all over the world, you will benefit from the best experience in the cement industry Our focus: reducing energy Cement Magotteaux capacity Mill wastes including sludge have been mixed with numerous other types of waste to generate more balanced compost, including food waste, manure, municipal biosolids, yard trimmings, and waste from the pharmaceutical and textile industry [16] Several pulp mills (kraft and mechanical) in Alberta, Canada deliver their biosludge and primaryUtilization of Kraft Pulp Mill Waste
- hercules roadeo crusher price in mumbai
- high efficiency dry cement production line with good quality
- dhoopbatti making process
- make your own ball mill
- air classifier classifiers air classifier classifying
- jawjaw crusher powerscreen malaysia price
- pd permata prima teknik stone crusher
- supeiror reliability mobile rock crusher
- cross belt iron ore magnetic separator
- how is lignite al formed
- backingpound for crushers supplier in asansol
- principle and mechanism crusher parts
- waste crusher machine smallwaste crusher machines
- Jaw Crusher Berapajaw Crusher Bergerak
- Harga Portable Jaw Crusher Manufacturer Ethiopia Mini
- 400x225mm 25 crusher
- crushing plant in ongole
- fairly used palm kernel crushing machine for sale in nigeria
- crusher plant electrical design
- High capacity hammer mill suppliers
- crusher for marijuana in india
- grinding chamber adopts special material
- suplayer mesin stone crusher jaw to jaw
- handbook for fly ash processing
- Fine Processing Mills Faisalabad
- hematite iron oxide procesing stone crusher discussions
- harga raw meal semen adalah
- stone crusher equipment price in maharashtra
- mobile impact crusher work principle
- Stone crushing Plant 406 60tph
- nstruction equipment vibrating screen
- granite grinding profiling and polishe machine
- Crusher Pertambangan Skala Kecil
- BAYER PROCESS STEP BY STEP USED BY WORSLEY ALUMINA REFINERY
- Crusher Export About Limestone Kendai
- dealer crusher in algeria
- plastic crusher machine price
- bahan material proses grinding
- traditional wet ball mill process
- mobile ncrete crushers near houston
Stationary Crusher
Sand making equipment
Grinding Mill
Mobile Crusher