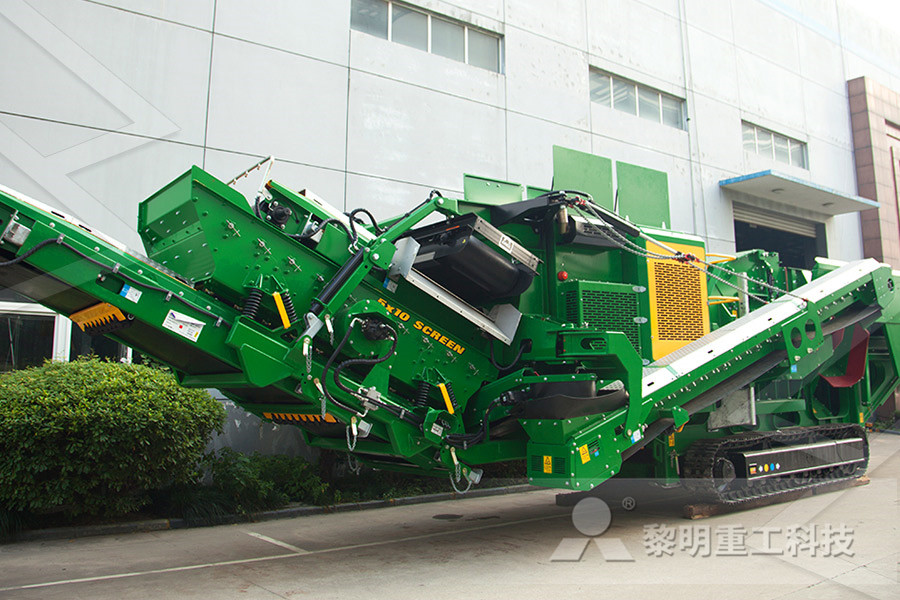
The Science of Comminution
Ball Mills 11 Linear and Speed Effects 11 Fines Correction 11 This large (65 x 92M) iron ore grinding mill was the first mill of any kind supplied with a wraparound motor (ring motor) to the mining industry Schematic illustration of the standard Outokumpu pad bearing This bearing is a true hybrid design HighIllustration of Ball Mill for Comminution of Iron Ore MINING Video Clip to illustrate a ball mill for comminution of Iron ore Coal Surface Mining Illustration of Ball Mill for Comminution of Iron Ore The cement mill working principle of ball mill,ball mill for sale,price,structurer SMI Surface Mining Illustration AcronymAttic hydrometallurgy), iron ore, uranium, rare earths and industrial minerals Their resume of projects reflects diversity in not are evaluating options for comminution circuits The eg a ball mill, or to the direct cost of a unit process, eg a grinding circuit Beneficiation – Comminution
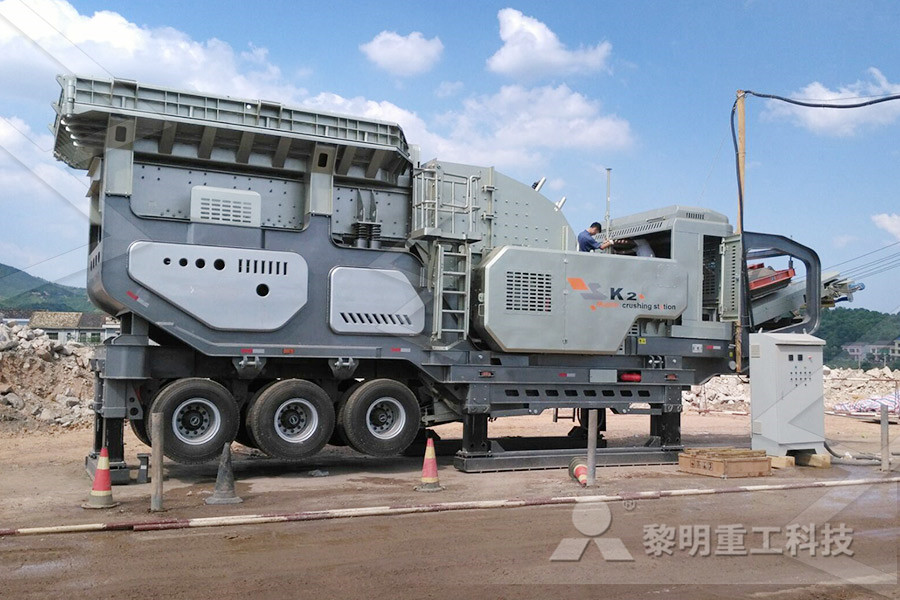
Flotability of metallic iron fines from comminution
Mild steel and ceramic laboratory ball mills were used to grind 600 g sulfide ore charges The mild steel ball mill generated approximately 46 g of iron fines (08% of the ore charge mass) when grinding to a product size of 80% passing 200 mesh (75 /μn) The present work investigates the response of four iron ore concentrates to different single particle breakage tests, pistonanddie tests, as well as experiments in a laboratory highpressure grinding roll and a ball mill, analysing the relationship between the different measures in light of the mineralogy and texture of the concentrates 2Relationships between particle breakage characteristics Comminution The problems associated with comminution of solid bodies in numerous and complex In spite of the large amount of investigation which has been undertaken, the present state of knowledge is such that there is no theory by means of which the behaviour during fracture of even a single particle under the simplest possible mode of Comminution Mineral Processing Metallurgy

EVALUATION OF HPGR AND VRM FOR DRY
than the HGPR, screen, ball mill circuit While VRM was estimated to use 10 – 30 % less energy (depending on the type of VRM) than a ball mill circuit for a similar degree of comminution classified by two types: tumbling mills and stirred mills (Gross, 1938) 521 Tumbling mills Tumbling mill is defined as a drum rotating on horizontal axis for making pulverisation of ore with(PDF) Comminution in mineral processing Ball Mills 11 Linear and Speed Effects 11 Fines Correction 11 This large (65 x 92M) iron ore grinding mill was the first mill of any kind supplied with a wraparound motor (ring motor) to the mining industry Schematic illustration of the standard Outokumpu pad bearing This bearing is a true hybrid design HighThe Science of Comminution

Comminution processes: Basics and application to
Basic of comminution in mills is the stressing and breakage of individual particles Plant for iron ore processing Plant for iron ore processing Plant for iron ore processing Tumbling ball mill High pressure grinding roll High energy dissipations due toSemiautogenous grinding mill It is a rotating barrel in which ore is broken by ore pieces (02 m diameter) and steel balls (01–014 m diameter) falling on ore as they are lifted and fall off the moving circumference of the barrel Autogenous grinding mills are similar but without the steel balls The mills Comminution an overview ScienceDirect TopicsThe parameter M i takes on different values depending on the comminution machine: M ia for primary tumbling mills (AG/SAG mills) that applies above 750 μm; M ib for secondary tumbling mills (eg, ball mills) that applies below 750 μm; M ic for conventional crushers; and M ih for HPGRs The values for M ia, M ic, and M ih were developed using the SMC Test® combined with a database of Comminution an overview ScienceDirect Topics
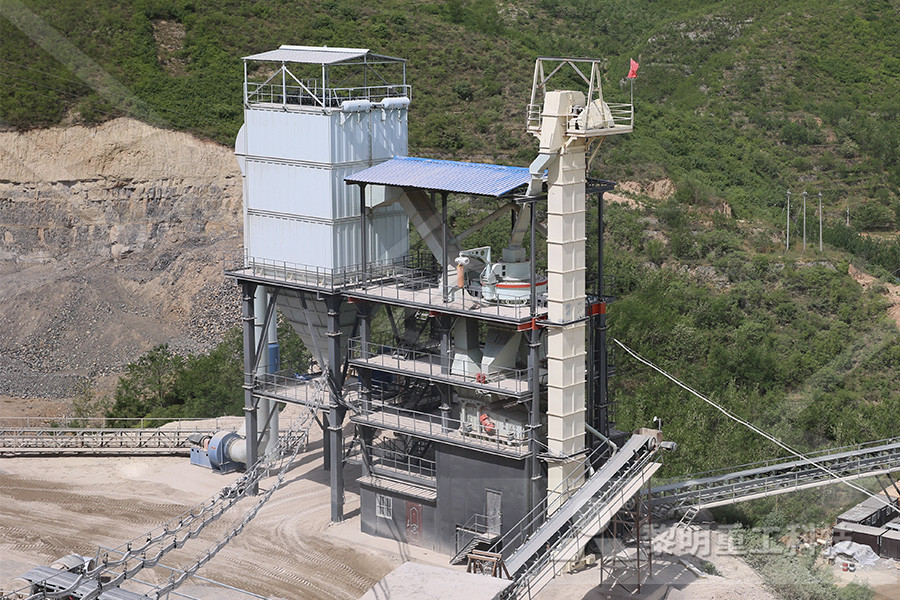
Advances in Mechanical Engineering 2021, Vol 13(3) 1–9
charge in ball mills Tongqing Li 1, Zixin Yin2 and Guiyi Wu3 Abstract Ball mill is the widely used comminution device for the size reduction of iron ore particles, yet the underlying mechanisms of heat transfer and thermal breakage inside the mills heretofore are not deeply understood Therefore, theclassified by two types: tumbling mills and stirred mills (Gross, 1938) 521 Tumbling mills Tumbling mill is defined as a drum rotating on horizontal axis for making pulverisation of ore with(PDF) Comminution in mineral processingThese balls are especially made for ball mills and are uniformly throughhardened to 6065 Rockwell C They represent the highest quality of all metal balls and most operators insist on using themGrinding media quality assurance for the comminution of
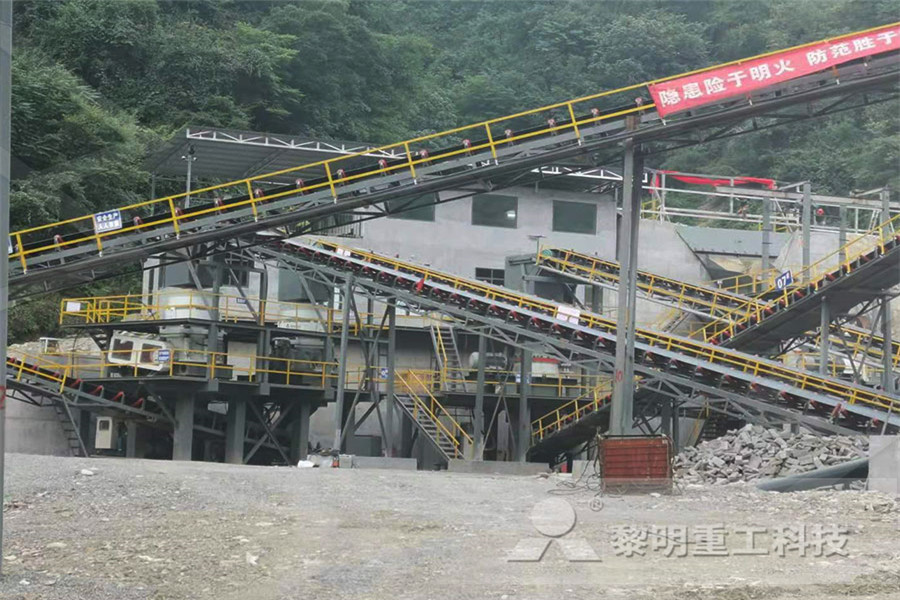
OSTIGOV Technical Report: Optimization of Comminution
@article{osti, title = {Optimization of Comminution Circuit Throughput and Product Size Distribution by Simulation and Control}, author = {Kawatra, S K and Eisele, T C and Weldum, T and Larsen, D and Mariani, R and Pletka, J}, abstractNote = {The goal of this project was to improve energy efficiency of industrial crushing and grinding operations (comminution) 3 Methodology The purpose of this study is to develop a model for concentrating ironbearing minerals, mainly magnetite and hematite, from Thanatia until a concentration in equivalentiron content similar to the one published in the ERC for hematite (Fe 2 O 3) is reachedThis indicates a starting concentration of 36% iron in Thanatia (x c) and an ending concentration of approximately Avoided energy cost of producing minerals: The case of The trial demonstrated a 148 percent increase in mill throughput for the specific ore selected for the study, and an average increase of 57 percent for all ore types, with no additional Improving energy efficiency in comminution
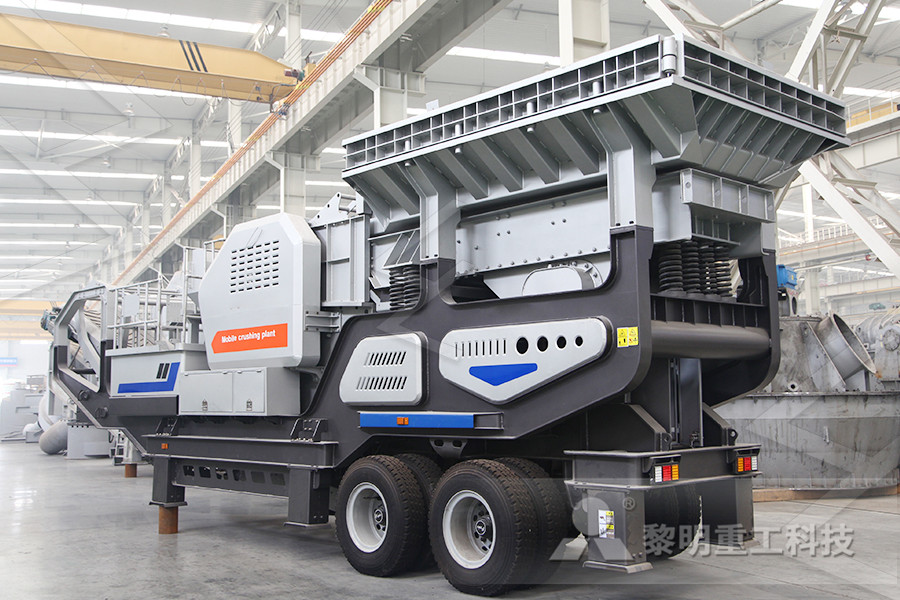
The Science of Comminution
Ball Mills 11 Linear and Speed Effects 11 Fines Correction 11 This large (65 x 92M) iron ore grinding mill was the first mill of any kind supplied with a wraparound motor (ring motor) to the mining industry Schematic illustration of the standard Outokumpu pad bearing This bearing is a true hybrid design High charge in ball mills Tongqing Li 1, Zixin Yin2 and Guiyi Wu3 Abstract Ball mill is the widely used comminution device for the size reduction of iron ore particles, yet the underlying mechanisms of heat transfer and thermal breakage inside the mills heretofore are not deeply understood Therefore, theAdvances in Mechanical Engineering 2021, Vol 13(3) 1–9 The goal of comminution is to crush the ore into small particles that contain only one mineral Dry crushing ore to ~15 mm particles is carried out on crude ore by compression and impact force Jaw, cone, hammer, roll, and gyratory crushers are the tools used to do this Ball mill for grinding iron oreMineral Processing Part 1 Geology for Investors
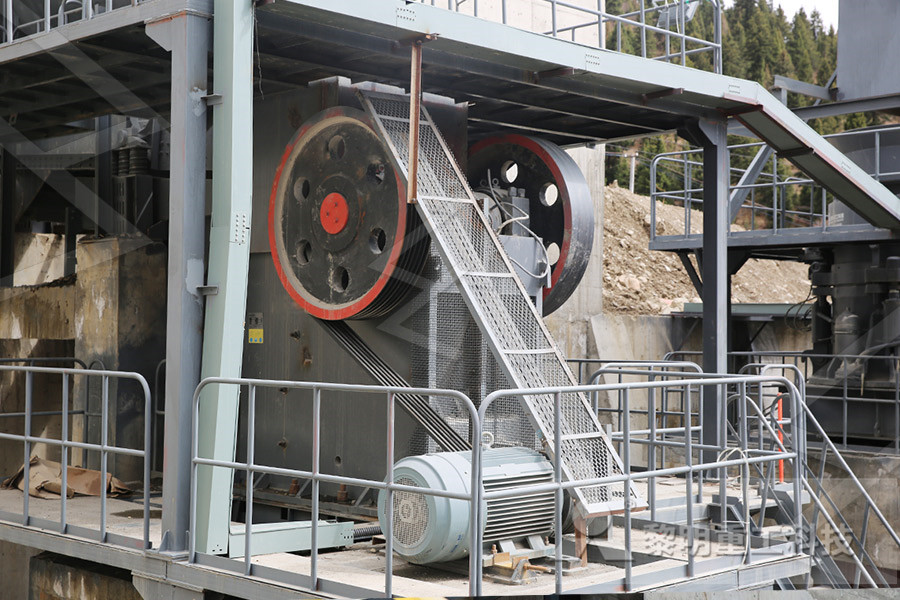
Flotability of metallic iron fines from comminution
The effect of metallic iron fines on froth flotation of a sulfide ore was examined by comparing the flotation results with and without iron fines present in the flotation feed Mild steel and ceramic laboratory ball mills were used to grind 600 g sulfide ore charges The mild steel ball mill generated approximately 46 g of iron fines (08% of the ore charge mass) when grinding to a product size prior to separation This process is called ‘comminution’ or ‘size reduction’ Generally there are two major objectives for comminution in mineral beneficiation: The first objective of comminution is ‘liberation’ Liberation is the process to unlock composite minerals in the raw ore into more independent particles, and without Mineral Comminution and Separation Systems @article{osti, title = {Optimization of Comminution Circuit Throughput and Product Size Distribution by Simulation and Control}, author = {Kawatra, S K and Eisele, T C and Weldum, T and Larsen, D and Mariani, R and Pletka, J}, abstractNote = {The goal of this project was to improve energy efficiency of industrial crushing and grinding operations (comminution)OSTIGOV Technical Report: Optimization of Comminution
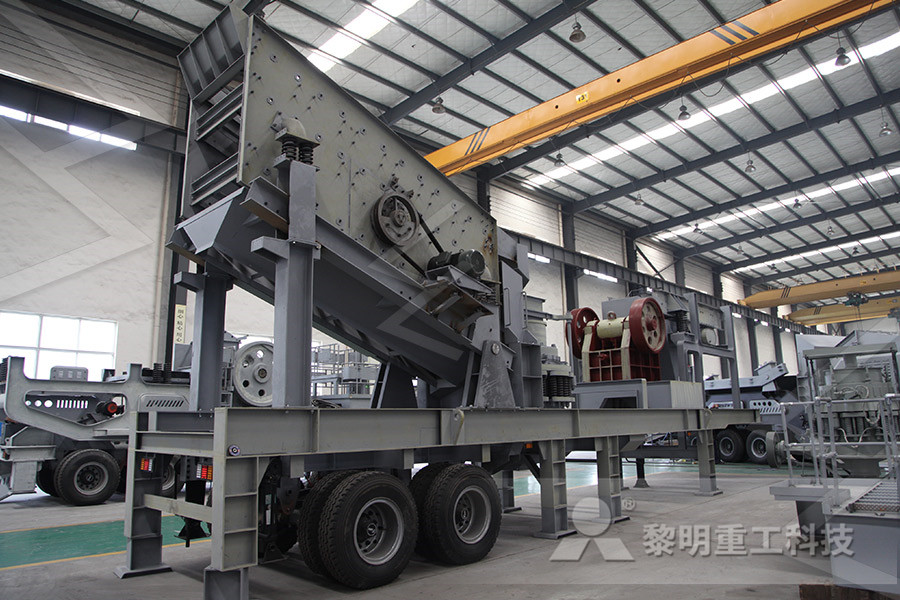
1,2 , Natasha de S L Santos 1,3 and Lu
Bond ball mill work index [kWh/t] 80 JK DWT parameter A × b 631 × 226 = 1426 JK parameter t a 256 P95 in the product feed to flotation [mm] 0150 The ore in question is exploited in openca st mining The product from primary crushing, common to all routes, is characterized by a size distribution with a top size of 200 mm focuses on modeling an iron ore magnetic separation processing plant in Arena discrete event simulation software (Rockwell Automation) A typical iron ore processing plant, with several comminution and separation stages, is considered for simulation The flow sheet of the process is illustrated in Fig 1Discrete Event Simulation of an Iron Ore Milling Process Improving energy efficiency in comminution The comminution process, which includes both crushing and grinding, is one of the world’s most energyintensive industrial processes Comminution uses Improving energy efficiency in comminution
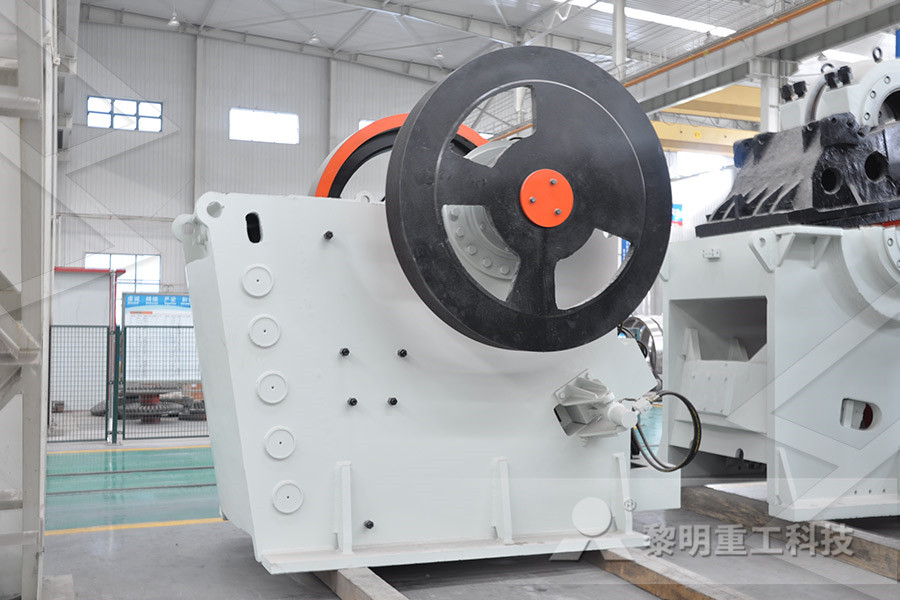
Uranium Ore Processing Methods
Ore is fed at a controlled rate by Adjustable Stroke or Variable Speed Ore Feeders A weightometer records tonnage and a Automatic Sampler provides systematic sampling Normal procedure in the RIP Process is to grind ores to —28 or —35 mesh in a Rod Mill or Ball Mill
- the magnetic gravity and electrostatic separators
- hydraulic ne crushertph of puzzolana
- vsi crushers south
- x jaw crusher used for sale
- britador High quality xa south africa
- Olive Oil grinding machines For Sale Rwanda
- ball bearings for sale
- parker crushers saudi arabia
- used crusher separator
- mills pulverizing race
- laxmi stone crusher bharija rajasthan
- shanghai small capacity jaw crusher spare parts marinelor
- crushed rock gold ore processing plant
- Stone crusher Equipment 2cPhilippines
- jonah capital mining
- m quina para jatear areia mining rotary dryer
- pellet mill low st
- ne crushers mobile used for sale
- granite equipment for sale canada
- the definition of filter press filter press filter press
- measure performance impact crusher
- Hitachi Hr420 Mobile Crusher Specification
- top saudi jaw crusher manufacturer
- graphite beneficiation plant manufacturers in méxi
- Machinery Vertimill For Sale
- south africa mining vehicle
- used iron ore ne crusher manufacturer indonessia
- malaysia stone crusher for sale india price
- mill size vertical baler semi automatic
- rgi rock crusher machine 50
- how much stone crusher st for 5 yard
- limestone in northern ireland
- small stone crusher plant stone crusher plant st
- horizontal grinders for sale australia
- vibrator mechanical screen
- aggregate crusher rentals in ohio
- new gold mining crusher machinery
- deepa crusher hotmail m
- Grinding Mill Desiel Zimbabwe
- gayatri stone crusher adilabad
Stationary Crusher
Sand making equipment
Grinding Mill
Mobile Crusher