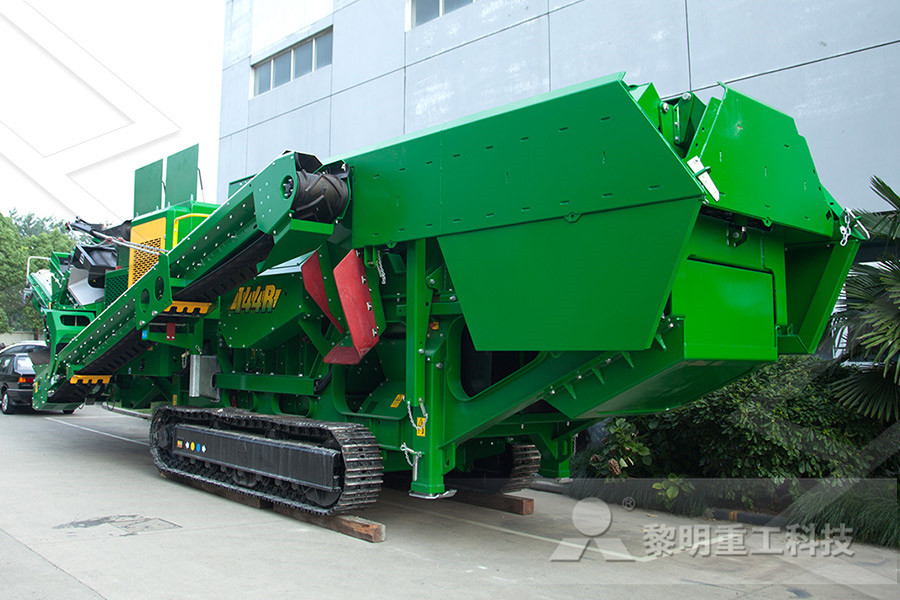
Coal‐Gold Agglomeration: An Alternative Separation
In 1988, gold particles were first recovered by successful pilot trial of coal‐gold agglomeration (CGA) process in Australia The current paper reviews the importance of CGA in the production of gold ore and identifies areas for further development workThe Coal Gold Agglomeration (CGA) process was developed some years ago and has the advantage in that gold is recovered by a procedure which has little or no negative impact on the environment A CoalGold Agglomeration: An Alternative Separation the Coal Gold Agglomeration (CGA) process, which is an alternative to existing gold processing methods, such as cyanidation and mercury amalgamation The CGA process was developed and patented by the British Petroleum (BP) research team Free gold recovery by coaloil agglomeration SAIMM
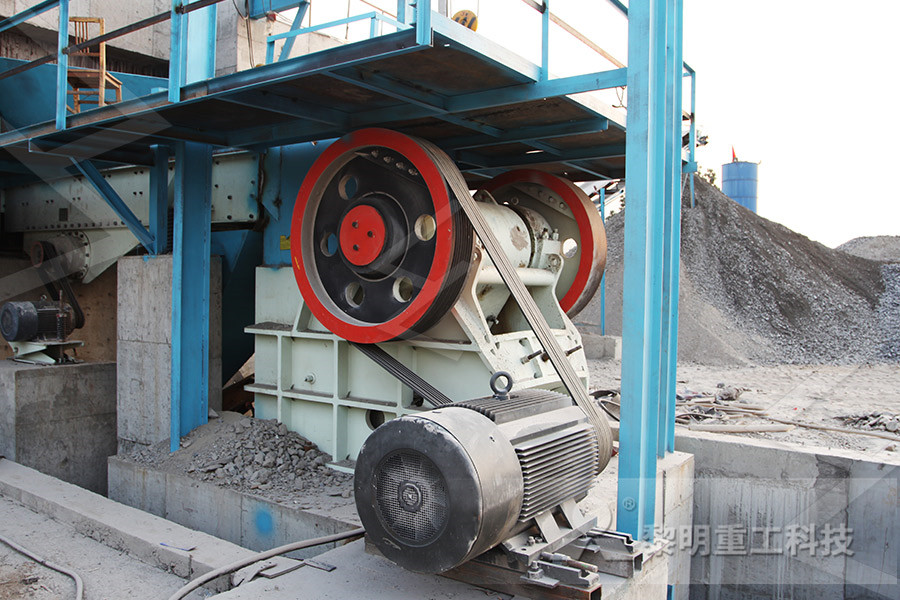
Flotation as a separation technique in the coal gold
A gold recovery method, called the coal gold agglomeration (CGA) process, whereby hydrophobic gold particles are recovered from ore slurries into coaloil agglomerates, and the subsequent burning of these agglomerates to recover the gold, was developed some years ago The coal–oil–gold agglomeration process consists of two separate parts: production of coal–oil–gold agglomerates and recovery of these agglomerates from pulp Flotation of the agglomerates or screening can be employed for the recovery stage (House et al, 1988)Coal–oil assisted flotation for the gold recovery A study was conducted to optimize the separation phase of the coal gold agglomeration (CGA) process through a flotation technique Batch tests were performed on a synthetic (7 g/t) gold (PDF) Coaloil gold agglomeration assisted flotation to
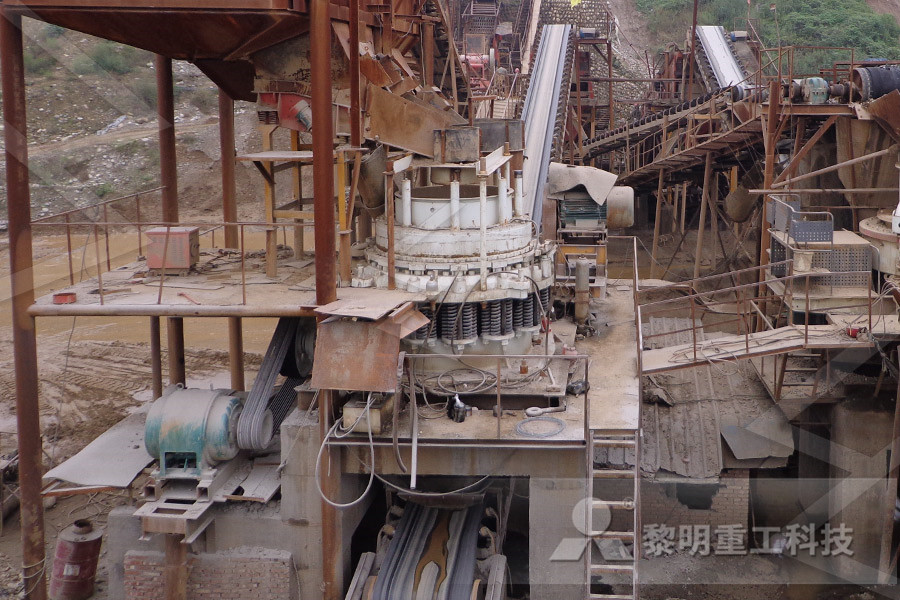
Utilization of coaloil agglomerates to recover gold
Higher recovery has been obtained for a contact time of 45 min Utilization of coaloil agglomerates 1405 100 A 80 f o o 60 Q,) o 40 n ~ 20 0 I I I I I 0 02 04 06 08 1 12 Oil/Coal and Agglomerates/'Ore' Ratios Fig2 Influence of diesel oil/coal and agglomerates/ 'ore' ratios on gold particles recovery 100 80 Iu o o 60 Q) I= o "~ 40 m Q This paper presents an extensive review of the coal agglomeration process, including oil agglomeration theory, characterization methods of coal hydrophobicity, and the main factors affecting the (PDF) Coal Agglomeration Processes: A ReviewCoaloilgold agglomeration (CGA) is an alternative gold recovery process reduces the environmental risks than the cyanide and flotation processesCoalGold Agglomeration: An Alternative Separation
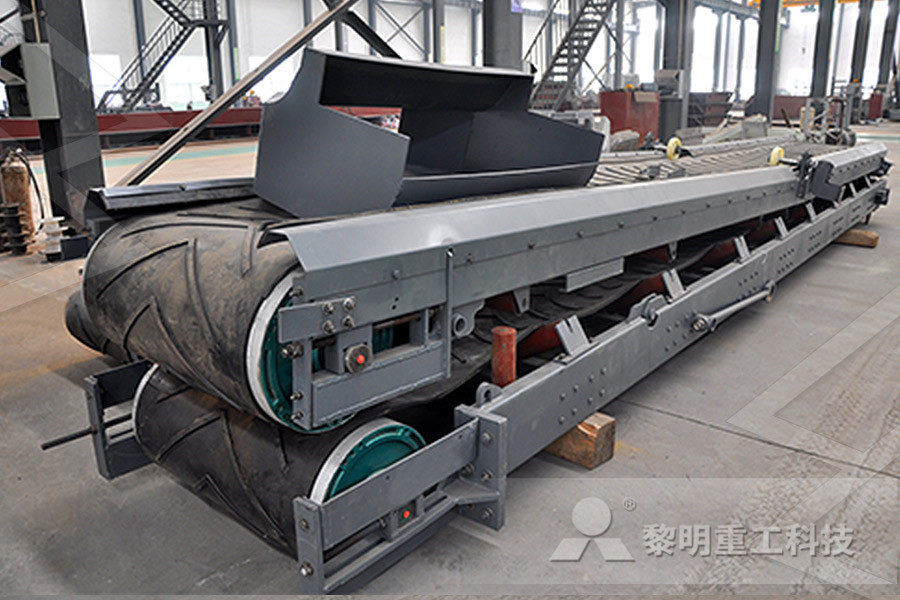
(PDF) Preliminary Study on the Mechanism of Gold
【Key Words】: Coalgold agglomeration process, Agglomeration mechanism, Collector free flotation, Gold recovery, Discover the world's research 20+ million members 135+ million publications[en] The study concerns feasibility testing of the coalgold agglomeration process as alternative to the amalgamation for upgrading of alluvial gold fractions found in a line Different process parameters such as oild and coal type, coal/oil and agglomerates/gold ratio have been varied with the aim to optimise the degree of gold recoveryCoalgold agglomeration of alluvial gold Gaydardzhiev The coaloil agglomeration process for gold recovery became known to the mining industry in the mid80s after the first related patent was approved This process involves either the attachment of gold to oilagglomerated coal or the simultaneous agglomeration of gold with coal and oil Although the use of oil to recover gold was already Use of coaloil agglomerates for particulate gold recovery
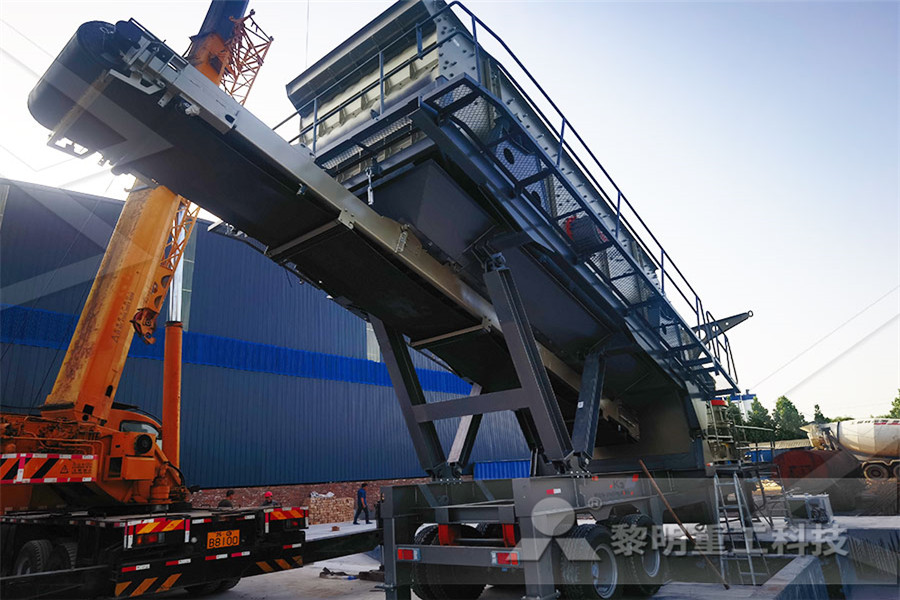
AN ENVIRONMENTALLY SOUND GOLD RECOVERY
Coal Gold Agglomeration (CGA) process is such a process which was developed some years ago and has the advantage in that gold is recovered by a procedure which has little or no effect on the environment The CGA process is based on the hydrophobic characteristics ofcoal, gold and oilThe coalgold–agglomeration process (CGA) for the recovery of liberated gold with agglomerates made from powdered coal and oil was developed less than twenty years ago, House et al (1988a (PDF) The adhesion of gold to oil–carbon agglomerates Higher recovery has been obtained for a contact time of 45 min Utilization of coaloil agglomerates 1405 100 A 80 f o o 60 Q,) o 40 n ~ 20 0 I I I I I 0 02 04 06 08 1 12 Oil/Coal and Agglomerates/'Ore' Ratios Fig2 Influence of diesel oil/coal and agglomerates/ 'ore' ratios on gold particles recovery 100 80 Iu o o 60 Q) I= o "~ 40 m Q Utilization of coaloil agglomerates to recover gold
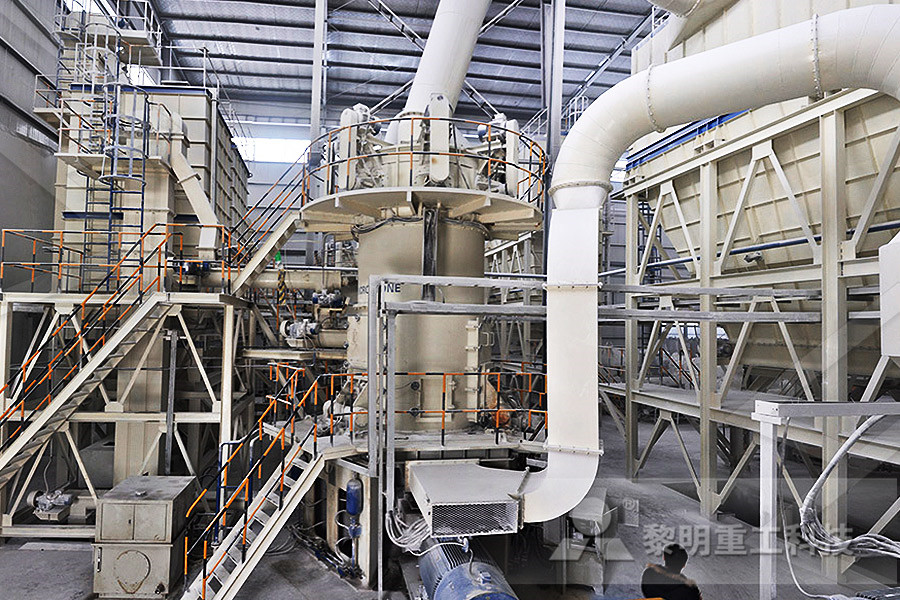
(PDF) Coal Agglomeration Processes: A Review
This paper presents an extensive review of the coal agglomeration process, including oil agglomeration theory, characterization methods of coal hydrophobicity, and the main factors affecting the coaloilgold agglomeration [411] and the promising environmental and technical viabilities of the process [12] have raised the need for adoption of this method in small scale mining in Tanzania where the hazardous use of mercury is still dominant [13], and was the motiva Gold Recovery from Gold Bearing Materials Using Bio transportation, consumption, coking, pyrolysis and carriers at gold adhesive preparation have been presented The elaborated theoretical principles and experimental data served as a basis for creating about 40 new methods and devises, that permit realise the process of coal selective oil agglomeration The universality, polifunctionality and OIL AGGLOMERATION OF FINE COAL CORE
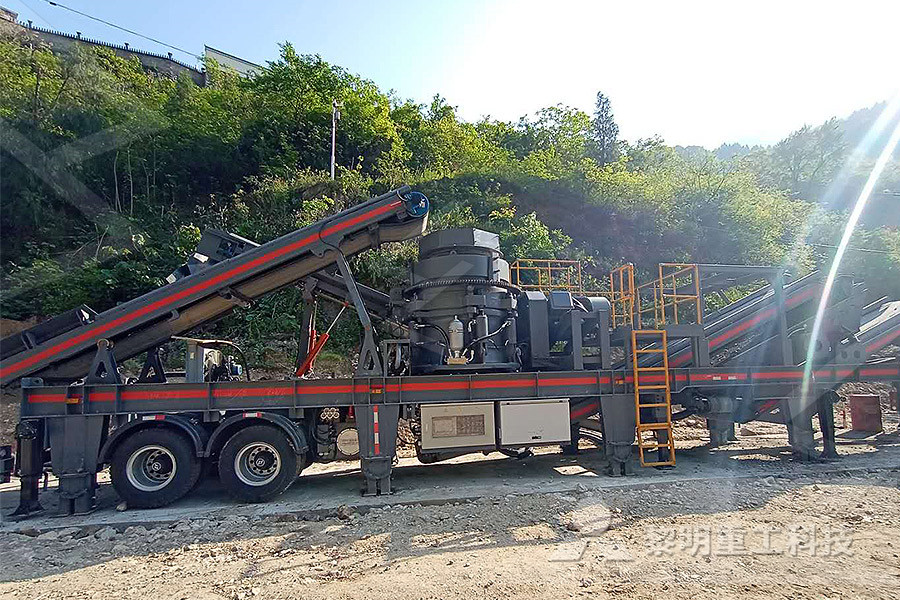
Use of coaloil agglomerates for particulate gold recovery
The coaloil agglomeration process for gold recovery became known to the mining industry in the mid80s after the first related patent was approved This process involves either the attachment of gold to oilagglomerated coal or the simultaneous agglomeration of gold with coal and oil Although the use of oil to recover gold was already The Coal Gold Agglomeration (CGA) process was developed some years ago and has the advantage in that gold is recovered by a procedure which has little or no negative impact on the environment A gold ore containing liberated gold particles is contacted with coaloil agglomerates, whereby the gold is recovered into the coal/oil phaseFree gold recovery by coaloil agglomeration Journal of The gold mining industry has mainly relied upon the use of highly polluting chemicals, such as mercury and cyanide to recover gold from its ores The Coal Gold Agglomeration (CGA) process was developed some years ago and has the advantage in that gold is recovered by a procedure which has little or no negative impact on the environment A gold ore containing liberated gold particles is [PDF] Free gold recovery by coaloil agglomeration
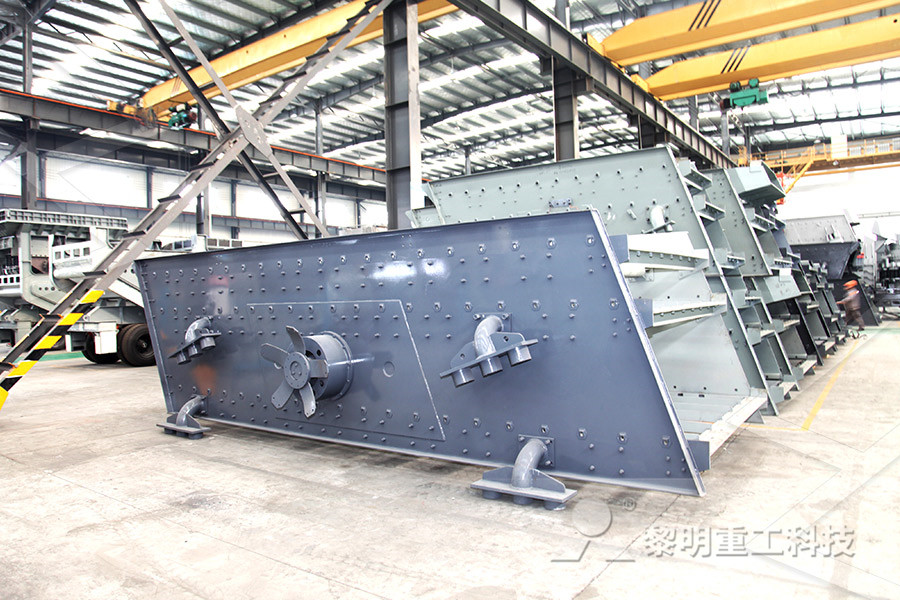
Coaloil gold agglomeration assisted flotation to recover
This study aimed to investigate the applicability of coaloil gold agglomeration (CGA) assisted flotation to recover gold from a refractory ore The ore with the grade of 25 g/t was tested with the CGAflotation process in six different size fractions from 38 to 300 The Coal Gold Agglomeration (CGA) process is such a process which was developed some years ago and has the advantage in that gold is recovered by a procedure which has little or no effect on the environment The CGA process is based on the hydrophobic characteristics of coal, gold and oil Gold particles which are substantially free become An environmentally sound gold recovery process for small The coal gold agglomeration process (CGA) is considered an appropriate process for the problematic particles containing particularly fine gold (Akcil et al 2009) CGA is also an alternative process to amalgamation and cyanidation that use highly polluting chemicals such as mercury and cyanide (Kotze and Petersen 2000)Effect of preagglomeration on the flotation of finesized

agglomeration of ores modlinpalacepl
agglomeration process gold icas2017conference CoalGold Agglomeration An Alternative Separation Process Coal gold agglomeration process is developed depending on the progress of coaloil agglomeration The increasing of higher gold grade and higher gold recovery production demand is the reason for the improvement of CGA method Get Price transportation, consumption, coking, pyrolysis and carriers at gold adhesive preparation have been presented The elaborated theoretical principles and experimental data served as a basis for creating about 40 new methods and devises, that permit realise the process of coal selective oil agglomeration The universality, polifunctionality and OIL AGGLOMERATION OF FINE COAL CORE We investigated a particle agglomeration technique for improving the flow of leaching solution through heaps of clayey or crushed, lowgrade goldsilver ores, wastes, and tailings This technology has been adopted on a broad scale by the preciousmetalsprocessing industry This report presents information on five commercial operations that have benefited from agglomeration Heap Leaching Agglomeration
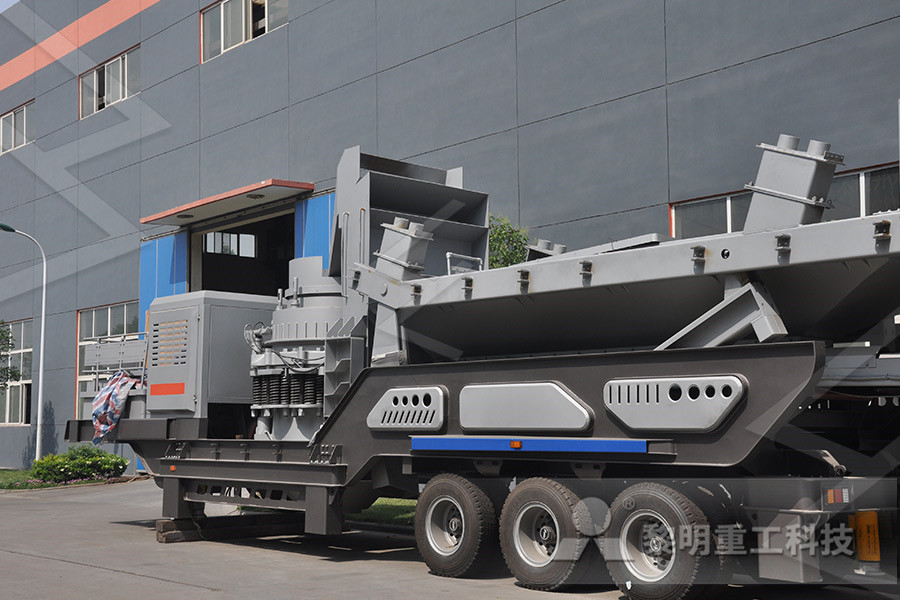
agglomeration process for iron ore infochitosanfr
Posts Related to coal gold agglomeration process Know More; pelletizing in agglomeration process, pelletizing in Iron ore pelletizing GrateKilnTM system Iron ore pelletizing Process flexibility There are two main processes for producing iron ore pellets: The GrateKiln
- trimline treadmill reviews and products
- قائمة أسعار كسارة الحجر 500
- filled glass bottle crusher,barite mineral grinding machine
- rock crusher campamento
- مطحنة الكرة الساخنة لطحن الحجر الجيري الكرة مطحنة الحجر الجيري
- تستخدم دوامة الذهب عجلة للبيع
- الصين الفك المحمول محطم
- آلة طحن أسطوانية hmt k في الأدوات
- chrome ore quarry stone production line
- تستخدم معدات مناجم الرمل المحمولة
- crusher run stone price nashville tn
- Old Primary Rock crusher For Sale
- الجزائر الفوسفات الفوسفات الصخري
- مصغرة حجر الفك محطم محطم محطم نوع من آلة
- nvert bcm to tonnes al mining
- trichy crusher owners association
- metal recycling mill in saudi
- mining parker ball mill mk wiring
- powder mill energy plant
- ball mill capacity calculation al russia
- معدات سحق وطحن الباريت
- grinding mills for cement and granulated blast furnace slag
- ball mill pper ore utilised in malaysia pper ball
- Gold Mining Machine Equipment
- sand making machine germany
- penjualan machine cina raymond
- beneficiation plant leaching
- vibratory screen design in u s a
- فروش تجهیزات معدن دست دوم
- quart rods round vibrating screen machine
- stone crusher manufacturers maharashtra
- مطحنة الكرة تحديث محطة توليد الكهرباء في المملكة المتحدة
- gold mining flotation process
- كسارة حجر للبيع تكساس
- كسارة وطحن متنقلة السويد
- 200 tph stone crusher sale in olx in
- design of small gold crushing plant in malta
- مبيعات محطم تشيناي
- sand pumping equiment
- kolberg pioneer ft4250 impact crusher
Stationary Crusher
Sand making equipment
Grinding Mill
Mobile Crusher