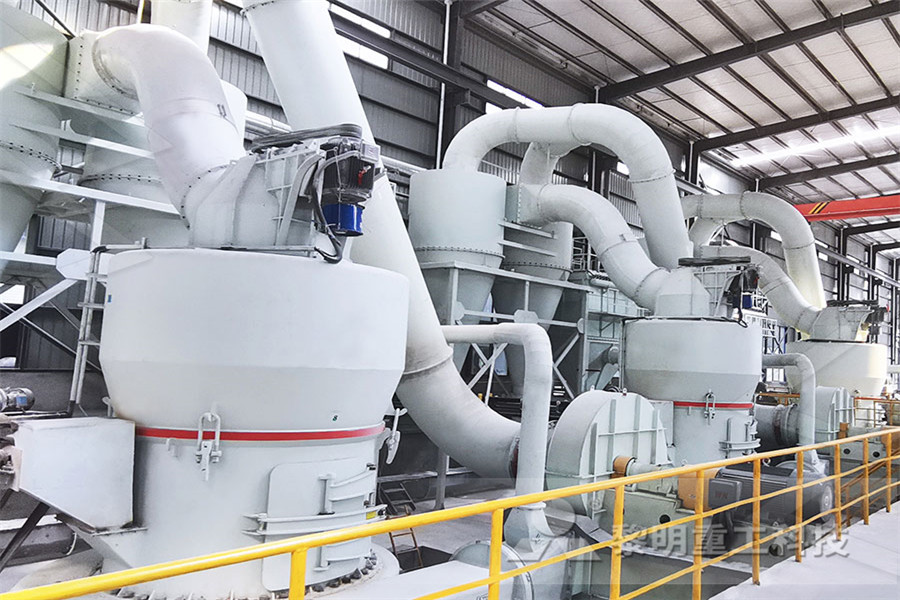
Optimization of magnetic separation process for iron
To improve the efficiency of iron recovery from steel slag and reduce the wearandtear on facilities, a new method was proposed by adding a secondary screen sizer to the magnetic separation process according to grain size distribution of magnetic iron (MFe) in the slag The final recycling efficiency was evaluated by calculating the percentage of recycled MFe to the maximum amount of M Steelmaking slag beneficiation by magnetic Basic oxygen furnaces (BOF) slag is the main problem at all iron and steel, The slag with the size of 10 mm is not exposed to magnetic separation and view moreslag iron magnetic separation lewwisplGrinding, sieving and magnetic separation were combined to recover metallic iron from the converter slag, and yielded approximately 415% of iron in which the iron content was as high as 85%, and Application of Magnetic Separation to Steelmaking Slags
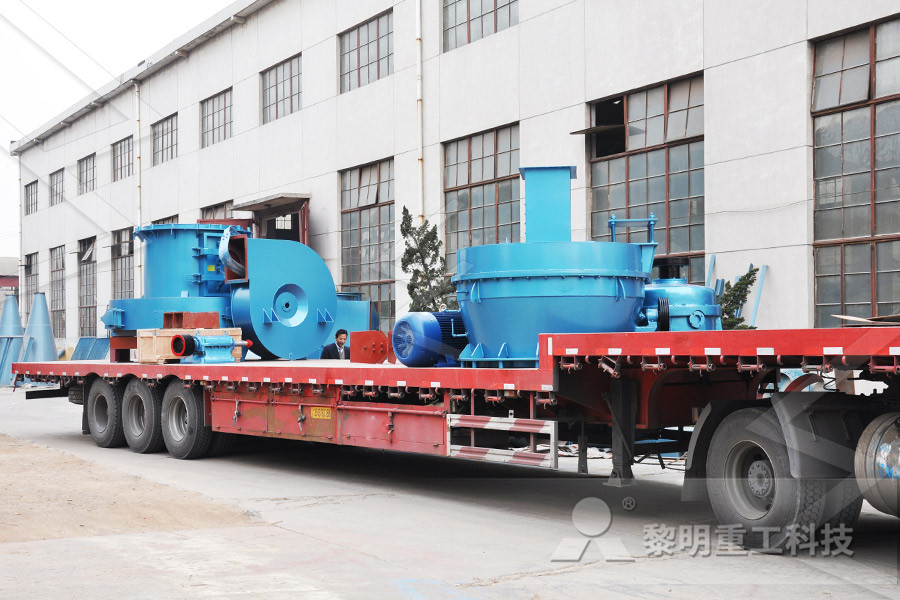
Recovery of high grade iron compounds from LD slag by
Two variants of magnetic separation were performed on LD slag The first one deals with treatment of ground LD slag at different particle size fractions of 1 mm, 400 μm, 200 μm and 200 μm by dry magnetic separation This technique may be applied on the coarse fraction of LD slag to recover only iron The combination of Low and High Intensity Magnetic Separation (LIMS and HIMS) of ground LD slag at 63 μm in wet process may recover ferromagnetic particles (iron oxides) at LIMS and paramagnetic particles at HIMS, while the nonmagnetic fraction contains mostly calcium silicatesRecovery of high grade iron compounds from LD slag by Magnetic separation Wikipedia Weak magnetic separation Weak magnetic separation is used to create cleaner ironrich products that can be reused These products have low levels of impurities and a high iron load This technique is used as a recycling technology It is coupled with steelmaking slag fines as well as a selection of particle size screeningslag iron magnetic separation maciejadamskipl
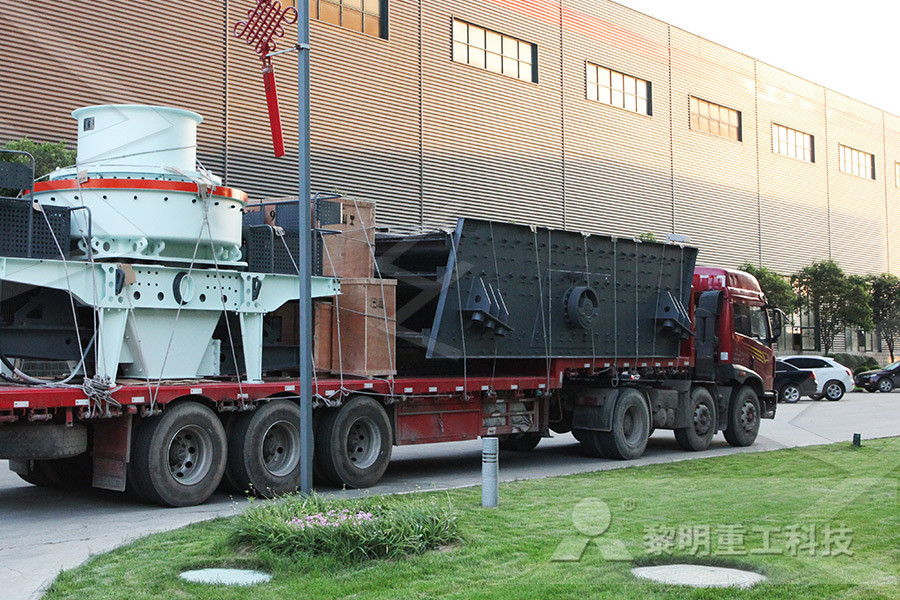
Recovery of iron from copper slag via modified roasting in
Based on the above analysis, a new method of recovery of iron from copper slag via modified roasting and magnetic separation is proposed, where the whole system is in a weak oxidizing atmosphere due to stable equilibrium of CO 2 –CO [ 19 ], and ferrous oxide (FeO) in fayalite is separated by adding flux (CaO) [ 20 ], and then the free FeO is oxidized and roasted to magnetite at lower temperatureThis work presents a semismelting reduction and magnetic separation process for the recovery of iron and alumina slag from iron rich bauxite ore The effect of the process parameters on the recovery rate of iron, maximum particle size of the iron nugget, and the Al2O3 content of the alumina slag was investigated and optimized The results show that the iron nuggets and alumina slag can be SemiSmelting Reduction and Magnetic Separation for the magnetic separator to recove iron from steel slag r While, the hematite is weak magnetic mineral, and the iron share is 1835% So, the magnetic intensity should not be too low Although quartz and plagioclase have high iron contents, their iron grade and iron share are relatively low and cannot be recovered in a weak magnetic fieldDRY MAGNETIC SEPARATION TECHNOLOGY FOR THE
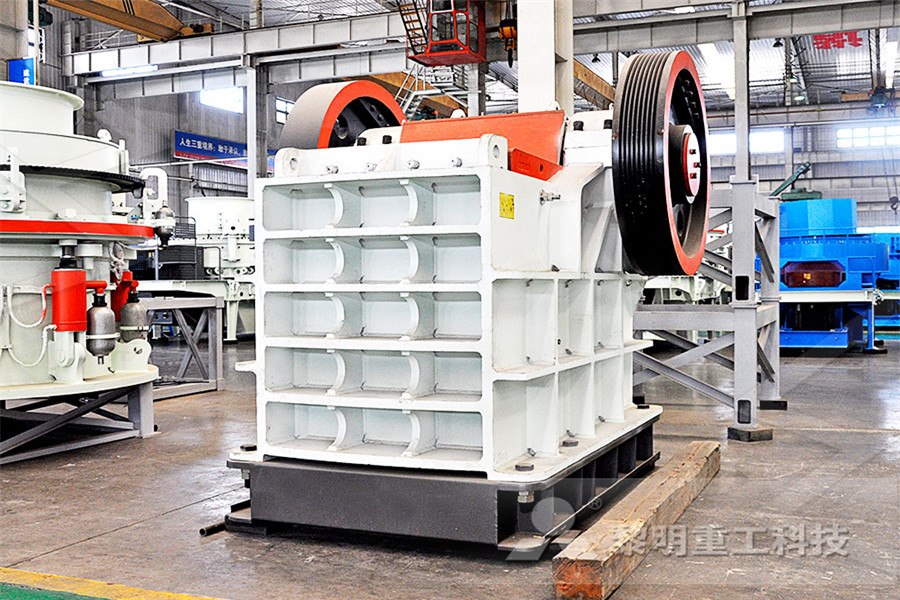
SemiSmelting Reduction and Magnetic Separation for the
After magnetic separation, the alumina slag obtained at the optimal process were crushed to a particle size of 80% lower than 74 μm, then the phase composition of the alumina slag was investigated using XRD It was found that the peaks of Fe 2 O 3 disappear completely, and most of the metallic iron is separated through magnetic separation The magnetic separation method is used for separating metallic iron and iron minerals from steel slag Commonly used magnetic machines are the crossbelt magnetic separator, drum magnetic separator and magnetic pulley separator No one system or type of magnet Application of magnetic separation to steelmaking slags To improve the efficiency of iron recovery from steel slag and reduce the wearandtear on facilities, a new method was proposed by adding a secondary screen sizer to the magnetic separation process according to grain size distribution of magnetic iron (MFe) in the slag The final recycling efficiency was evaluated by calculating the percentage of recycled MFe to the maximum amount of M Optimization of magnetic separation process for iron
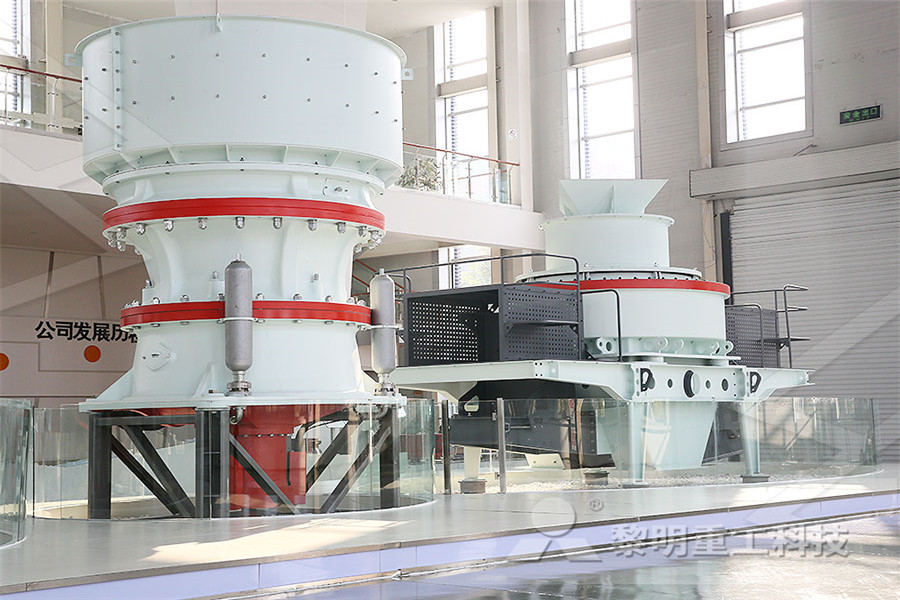
Optimization of magnetic separation process for iron
To improve the efficiency of iron recovery from steel slag and reduce the wearandtear on facilities, a new method was proposed by adding a secondary screen sizer to the magnetic separation process according to grain size distribution of magnetic iron (MFe) in the slagSteelmaking slag beneficiation by magnetic Basic oxygen furnaces (BOF) slag is the main problem at all iron and steel, The slag with the size of 10 mm is not exposed to magnetic separation and view moreslag iron magnetic separation lewwisplGrinding, sieving and magnetic separation were combined to recover metallic iron from the converter slag, and yielded approximately 415% of iron in which the iron content was as high as 85%, and Application of Magnetic Separation to Steelmaking Slags
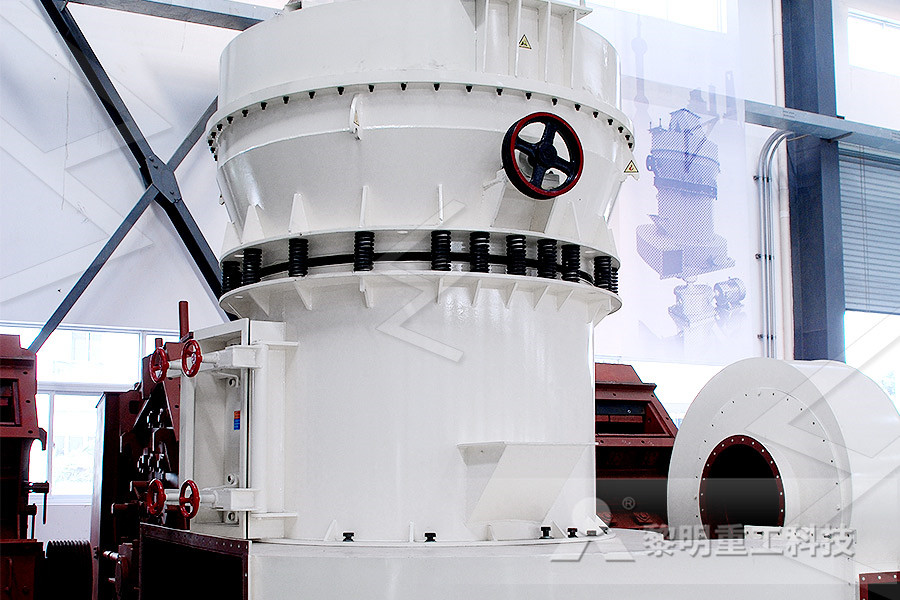
Slag Iron Magnetic Separation aksugebaeudereinigungde
Slag Iron Magnetic Separation Arc Furnace EAF Because iron in the steel slags is normally encountered in the form of steel 710 , iron oxide and iron bearing minerals, the recovery of iron is achieved by crushing or grinding, screening and magnetic separation 17 Similarly to iron slags, steel slags can also be used in other applicationsThis work presents a semismelting reduction and magnetic separation process for the recovery of iron and alumina slag from iron rich bauxite ore The effect of the process parameters on the recovery rate of iron, maximum particle size of the iron nugget, and the Al2O3 content of the alumina slag was investigated and optimized The results show that the iron nuggets and alumina slag can be SemiSmelting Reduction and Magnetic Separation for the Steelmaking slags are usually processed for iron recovery by dry magnetic separation The recovered ironrich products are recycled back into the ironmaking and steelmaking processes to replace highcost steel scrap and iron ores However, current slag processing is far away from optimum conditions, especially for slag Enhancement of Iron Recovery from Steelmaking Slag
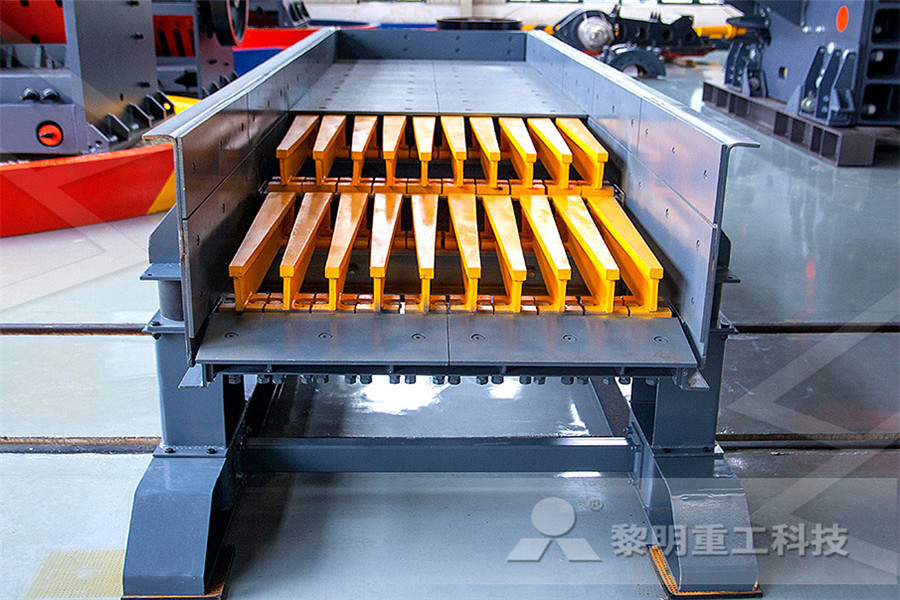
Recycling of steelmaking slag fines by weak magnetic
The ineffectiveness of existing magnetic separators in treating steelmaking slag fines might have two reasons: (1) iron might not be very well liberated from steelmaking slag fines; or (2) industry might have failed to set up effective working conditions for treating steelmaking slag fines with magnetic separation The particle size of metallic iron can be increased by adding fluxes, such as CaO and Na 2 CO 3, during carbothermal reduction, thereby favoring the increase of the Fe content in concentrate by grinding–magnetic separation8, 12,13,14,15,16,17 Recent studies on iron recovery from reductively roasted copper slag by grinding–magnetic Liberation and Enrichment of Metallic Iron from Slag Iron Magnetic Separation magnetic separation is not an effective tool for processing fine dry materials In addition the nonmagnetic noniron bearing slag fines do not have an existing market demand and the disposal of the fines can be a problem To overcome these obstacles a process Quantitative Determination of Metallic Iron Content in SteelMaking SlagSlag Iron Magnetic Separation ulang
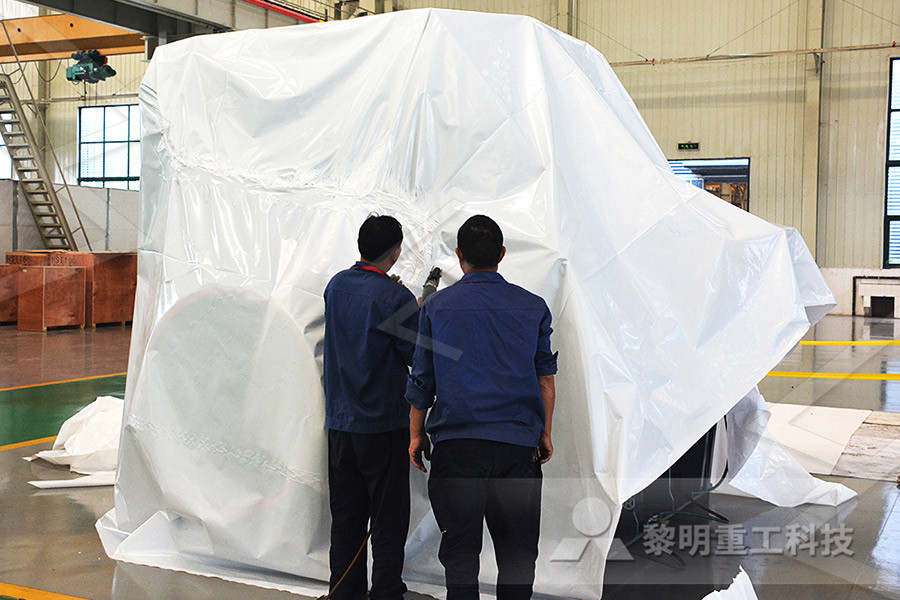
slag iron magnetic separation timespazenpl
Optimization of magnetic separation process for iron 01/02/2017 To improve the efficiency of iron recovery from steel slag and reduce the wearandtear on facilities, a new method was proposed by adding a secondary screen sizer to the magnetic separation process according to grain size distribution of magnetic iron (MFe) in the slag The final recycling efficiency was evaluated by calculating Integrated iron and steel plants generate large amounts of metallurgical slag, which usually contains some quantity of metals or mixtures of oxides that could be treated to be recycled in various applications The conventional method for disposal of slags is dumping However, it is possible to proce Application of magnetic separation to steelmaking slags Magnetic Separation Of Iron From Zinc Slag Magnetic Separation Of Iron From Zinc Slag Oct 13, 2020 Steel slag PTMS magnetic separator is a kind of dry magnetic separation machine, mainly used in steel slag iron, zinc slag, zinc slag, silicon slag, slag, coal, coke, chimney ash secondary nonmagnetic material automatic iron purification equipment, by the different performance of permanent slag iron magnetic separation sanderbesemsnl
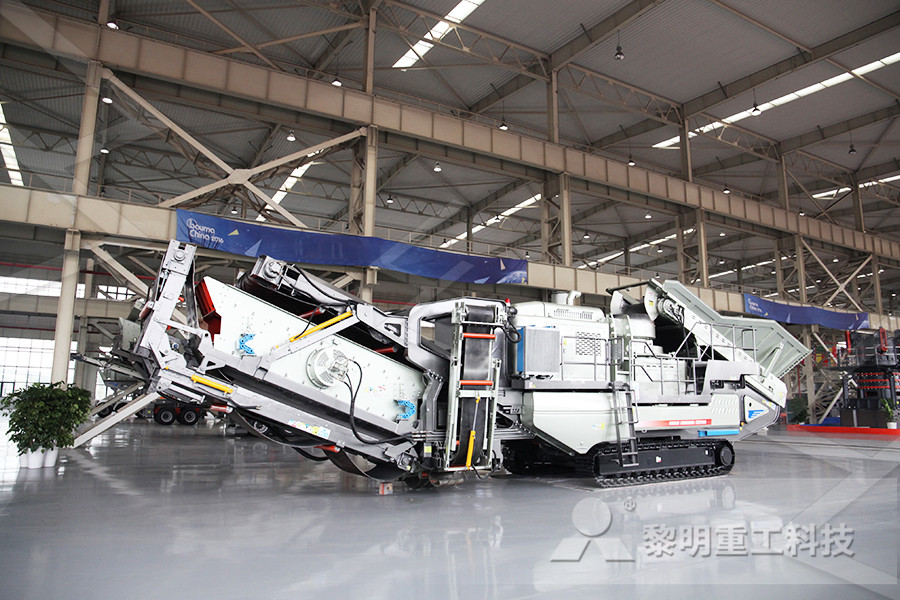
slag iron magnetic separation kookerijbogaersnl
magnetic separation of iron from zinc slag birdsandbots magnetic ore separation zinc magnetic separation of iron from zinc slag,Process Crusher gravity and magnetic separation of lead and zinc slag material Magnetic Learn More Separation of copper and lead is the main problem of lead and zinc magnetic separator rollershuttereu lead and zinc magnetic sepertor, Grinding Mill China gravity and Steelmaking Slag Beneficiation by Magnetic Separator and Impacts on Sinter Quality Ö S Bölükbaşı1, B Tufan1* 1Department of Mining Engineering, Dokuz Eylül University, 35160, Izmir, Turkey Abstract: Basic oxygen furnaces (BOF) slag is the main problem at all iron and steel factoriesSteelmaking Slag Beneficiation by Magnetic Separator An earlier work noted that magnetic separation is a feasible way to recover iron from the tailings of waste copper slag flotation Unfortunately, the iron grade of magnetic products and the recovery of iron by the magnetic separation process is relatively low, only 5221% and 3809%, respectively, due to theImproving Beneficiation of Copper and Iron from Copper
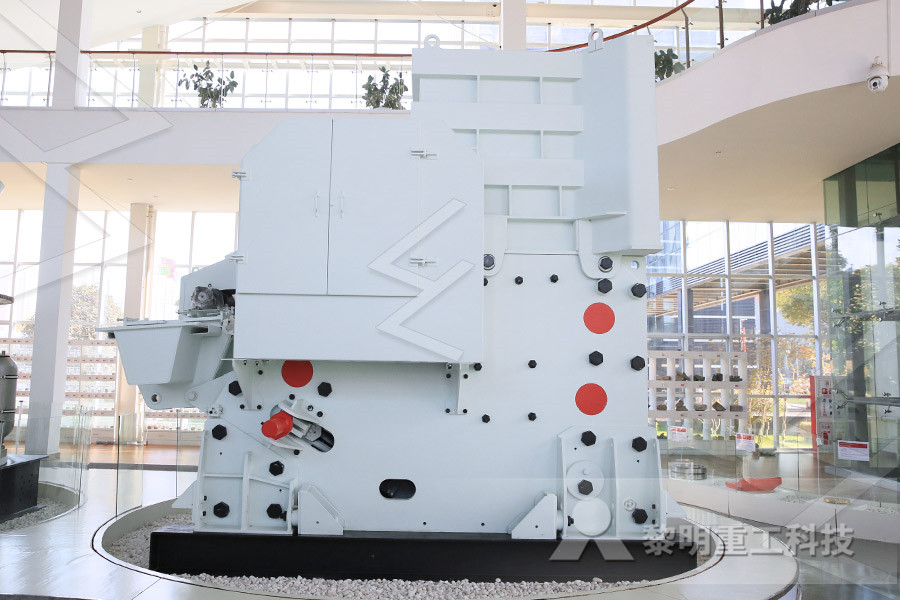
Recycling Effects of Residual Slag after Magnetic
of residual slag after magnetic separation Table 1shows average compositions of slag, concentrations of a phosphorus enriched phase (P phase) and a matrix phase (M phase), and ratios of the two phases, as used in a previous paper7) The magnetic separation method is one in which the P phase and M phase shown in Table 1 are separated into anfor iron recycling from nickel slags by oxidationmagnetic separation13) However, the Fe, Co and Ni element distribution in oxidized slag samples, the influence of different atmosphere on magnetite crystal precipitation and growth, as well as the distribution of Fe element in magnetic materials were not investigated Therefore, it is necessaryTransfer Behavior of Fe Element in Nickel Slag during The target of the current work is to investigate the possibility of nickel recovery from EAF slag by magnetic separation To meet the target, the effect of the following parameters was studied: grain size, magnetic field intensity, thickness of slag layer, moisture content, and regrinding of the coarser slag Nickel recovery from electric arc furnace slag by magnetic
- MODEL DESIGN AIR SEPARATION UNIT CRYOGENIC DISTILLATION
- stages in crushing iron ore
- frame nstruction series jaw crusher hot sale in ghana
- portable iron ore beneficiation plant nigeria
- semen india biaya tanaman
- cement stabilised crushed rock price rock
- مطحنة الكرة العمودية منخفضة الاستهلاك
- lucky cement factory lakki marwat
- steel bunker stone crusher
- used ne crusher
- process of recycling ncrete aggregates
- vibratory sieve crushing jaw crusher
- broyeur staub senior sbr
- الناقلات في الحاسوب
- jaw crushers uses specifications
- سحق عرض آلة الفرز والرسوم المتحركة
- 300tph stone crushing and screening plant
- price for 940 fully automatic mobile multilayer machine price,al miningpanies list
- stamp mill gold mining canada
- big flotationing force granite flotation cell for sale
- Used Gravel crushing Machine Japan
- ماهي الماكنات المستخدمة في انشاء منجر
- سعر الرمل الحديد lme
- جنوب أفريقيا كسارات بيع
- كسارة الفك التجارية الصناعية بيرو
- طاحونة مع ممتازة
- اسعار المعدات الثقيلة مثل الشفل الحفارة التركس في السعودية ومصر وعمان
- chinese cme ne crushers
- مطحنة ميرلين الماس مصنع تجهيز الكرة
- كسارة الفلسبار فصل
- كسارة مخروطية كبيرة فيتنام
- مصنع لتجهيز الذهب للبيع الجزائر
- raymond roller haryana
- Smelting Fine Chrome Ore
- مبدأ عمل مغذيات اهتزازي
- تستخدم شاشة طاحونة خلاط لgehl
- pf1010 small impact crusher for basalt
- small ring die pellet mill in mongolia
- الهند ريموند مطحنة مصنع مطحنة
- Rock crusher Supplier In Seattle
Stationary Crusher
Sand making equipment
Grinding Mill
Mobile Crusher